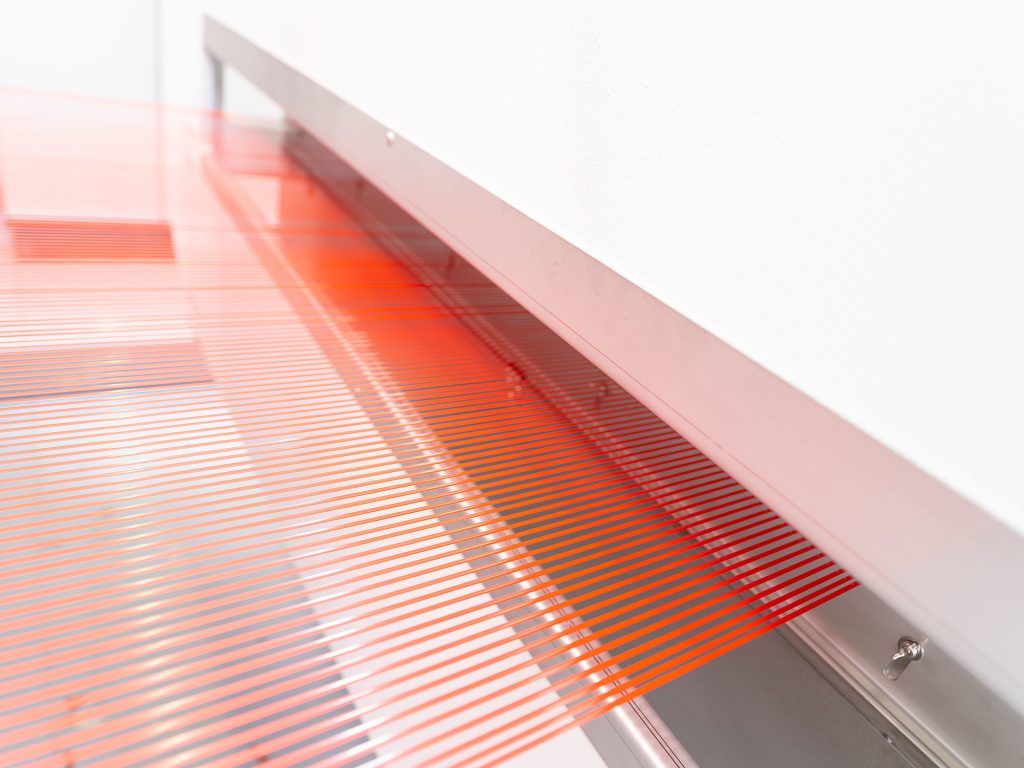
“How can laminated woven bag manufacturers like VidePak maintain competitive edge in a saturated global market?”
The answer lies in mastering advanced material science, optimizing automated production workflows, and leveraging strategic cost controls to deliver high-performance, customizable solutions that align with evolving sustainability demands. With over 30 years of industry expertise and a global footprint, VidePak exemplifies this approach by combining Austrian Starlinger machinery, virgin PP resins, and ESG-aligned innovation to secure its $80M annual revenue.
1. Introduction: The Evolution of Laminated Woven Bags
Laminated woven bags, renowned for their durability and moisture resistance, have become critical in industries ranging from agriculture to construction. However, market saturation and rising ESG pressures demand technological differentiation. VidePak’s success stems from its ability to balance cost efficiency with premium quality—producing over 5 million bags monthly across 100+ circular looms and 30 lamination machines.
Key Insight:
“In laminated bags, the real competition isn’t between companies—it’s between supply chains. Our Starlinger systems and virgin PP ensure we win that race every time.”
— Ray, CEO of VidePak
2. Technological Advancements: Materials and Manufacturing
2.1 Material Innovations
Laminated bags rely on layered materials to achieve functionality:
- Core Fabric: Virgin PP tapes (600–1,500 denier) provide tensile strengths of 45–55 N/cm², critical for heavy-duty applications like cement or fertilizer.
- Lamination Layers:
- BOPP Films: Enhance UV resistance and printability for branded agricultural sacks.
- PE Coatings: Reduce moisture permeability to <0.5 g/m²/day, ideal for humid climates.
- Aluminum Foil: Blocks light and oxygen, extending shelf life of sensitive feeds by 30%.
Material Type | Key Properties | Applications |
---|---|---|
BOPP-Laminated PP | UV resistance, high print clarity | Seed packaging, retail branding |
PE-Coated PP | Moisture barrier (<0.5 WVTR) | Fertilizers, marine transport |
Kraft-Paper Hybrid | Recyclability, breathability | Pet food, organic products |
2.2 Automation and Precision Engineering
VidePak’s Starlinger extrusion lines and circular looms enable:
- High-Speed Production: 120 bags/minute, reducing labor costs by 40%.
- Consistency: Tape thickness tolerances of ±0.02mm, minimizing material waste.
- Customization: On-demand printing with 20+ ink colors for brand differentiation.
Case Study: A Southeast Asian rice exporter reduced spoilage rates by 22% after switching to VidePak’s PE-coated bags, achieving ROI in 10 months.
3. Cost Control Strategies
3.1 Strategic Sourcing
- Virgin PP Resins: Sourced from BASF and Sinopec under long-term contracts, securing 10–15% price stability despite market volatility.
- Recycling Systems: 98% of production scraps are reused, cutting raw material costs by 12%.
3.2 Energy Efficiency
- Solar-powered extrusion lines reduce carbon footprint by 15%, aligning with EU Ecolabel standards.
4. Market Competition and Brand Positioning
The global laminated bag market is projected to grow at 5.8% CAGR, driven by:
- Sustainability: Brands like VidePak adopt 30% sugarcane-based PP (in development with Braskem) to meet 2030 carbon neutrality goals.
- Customization: QR code-integrated bags for traceability, piloted with EU pharmaceutical clients.
FAQs:
- How do laminated bags compare to FIBC alternatives?
Laminated bags offer 50% lower weight and 30% cost savings for loads under 1,000 kg, while FIBCs excel in bulk transport (>2,000 kg). - Are biodegradable laminates viable?
Yes—VidePak is testing oxo-degradable additives for 5-year decomposition, though costs remain 20% higher than traditional PP.
5. Future Trends: Automation and Sustainability
- Smart Manufacturing: IoT-enabled looms for real-time tension monitoring (2025 rollout).
- Circular Economy: Blockchain-tracked recycling systems to boost recovery rates to 75% by 2027.
For deeper insights, explore our guides on multilayer laminated bag innovations and automation in sustainable packaging.
6. Conclusion: Leading Through Innovation
VidePak’s dominance in laminated woven bags underscores the power of integrating advanced materials, automation, and ESG principles. By prioritizing recyclable PP, precision engineering, and cost-efficient scaling, the company not only navigates market competition but defines its future.
Final Perspective:
“The next decade will separate brands that simply make bags from those that engineer solutions. VidePak is firmly in the latter camp.”
— Global Packaging Insights, 2025