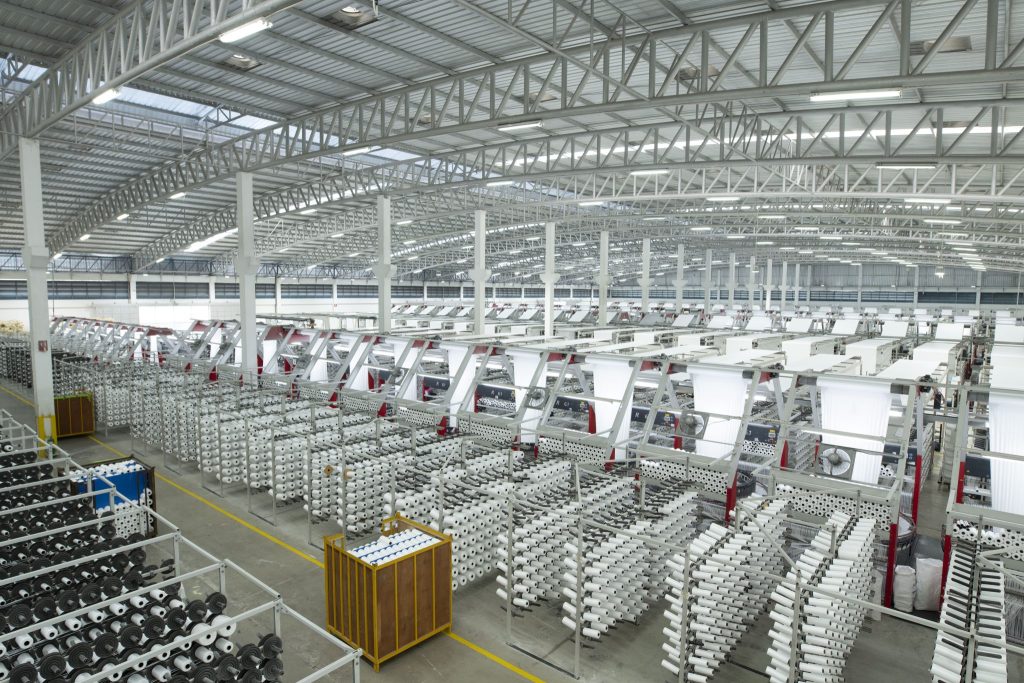
Introduction
China’s laminated woven bags market is experiencing transformative growth, driven by advancements in polypropylene (PP) material science, adherence to global standards, and innovative additive technologies. With a projected CAGR of 6.8% (2023–2030), the sector is reshaping packaging solutions for industries like agriculture, construction, and chemicals. This report explores how PP resin selection, compliance with international standards, and additive integration are redefining quality in laminated woven bags.
Market Dynamics and Key Applications
Laminated woven bags, primarily made from PP woven fabric coated with BOPP (Biaxially Oriented Polypropylene), dominate China’s packaging industry. These bags are valued for their tensile strength (4.5–5.5 g/denier), moisture resistance, and adaptability to high-speed filling systems. Major applications include:
- Cement and construction materials: 60% of China’s cement packaging relies on laminated PP bags due to their stackability and puncture resistance.
- Agricultural products: Customizable breathability (e.g., 50 mbar air permeability) ensures safe storage for fertilizers and seeds.
- Food-grade packaging: Compliance with FDA and EU regulations for low cadmium and azo-free dyes enables global exports.
Case Study: Tianjin Huajin Group, a leading manufacturer, produces 200,000 tons annually, serving 130+ countries. Their AD*STAR® bags, made with Starlinger machinery, achieve 1.5m drop-test resilience and 6-color printing precision.
Selecting PP Resins: Aligning with Global Standards
Q: How do international standards influence PP resin selection for laminated woven bags?
A: PP grade choice hinges on regional regulations and end-use requirements. Here’s a comparative analysis:
Standard | Key Requirements | Recommended PP Grade |
---|---|---|
ASTM (US) | Tensile strength ≥5.0 g/denier, UV resistance | Homopolymer PP (MFI 2–4) |
EN (EU) | REACH compliance, low heavy metals | Copolymer PP (MFI 3–6) |
JIS (JP) | High clarity, recyclability | Random copolymer PP |
GB (CN) | Azo-free dyes, CE certification | Impact copolymer PP |
Example: For EU markets, Huajin uses copolymer PP with 18–26% elongation to meet EN 13590:2023 standards, ensuring tear resistance during automated filling.
Additives and Fillers: Enhancing Performance
Q: What additives are critical for optimizing laminated woven bags?
A: Anti-UV stabilizers, antioxidants, and nucleating agents are pivotal for durability and compliance.
- Anti-UV Additives:
- Function: Prevent PP degradation under sunlight (common in agricultural storage).
- Data: Bags with 0.5% UV-326 additive retain 90% tensile strength after 1,000 hours of UV exposure.
- Case: Huajin’s “Anti-Skidding” bags integrate UV stabilizers for Australian grain exports, reducing waste by 15%.
- Antioxidants:
- Function: Inhibit thermal oxidation during lamination (temperatures up to 200°C).
- Example: Irganox 1010 (0.3% dosage) extends bag lifespan by 30% in high-humidity environments.
- Nucleating Agents:
- Benefit: Improve crystallinity for better printability and stiffness.
- Impact: Reduces lamination defects by 20% in high-speed production lines.
Compliance and Sustainability
Dialogue: Addressing Common Concerns
Q: How do manufacturers balance cost and regulatory compliance?
A: Tiered production strategies are key. For instance:
- Premium lines: Use FDA-approved PP resins and REACH-compliant dyes for EU/US markets.
- Economy lines: Opt for GB-standard materials with recycled PP content for domestic use.
Q: What sustainability trends are emerging?
A: Recyclable PP blends (e.g., 30% post-consumer resin) and biodegradable additives (e.g., TDPA™) are gaining traction. Huajin’s “EcoStar” line reduces carbon footprint by 40% while maintaining DIN 53857 tensile benchmarks.
Technical Parameters and FAQs
Table 1: Performance Metrics of Laminated Woven Bags
Parameter | Typical Value | Test Standard |
---|---|---|
Tensile Strength | 5.5 g/denier | DIN 53857 |
Air Permeability | 50 mbar | ISO 5636-5 |
Drop Test Resistance | 1.5m height | ASTM D5276 |
Printing Colors | Up to 6 | Pantone Matching System |
FAQs
- Q: How to verify PP resin quality?
- A: Conduct MFI (Melt Flow Index) tests and FTIR spectroscopy to confirm polymer consistency.
- Q: Can laminated bags withstand -20°C storage?
- A: Yes, impact-modified PP grades (e.g., Moplen HP548R) maintain flexibility below freezing.
Future Outlook
China’s laminated woven bag market is poised for innovation, with advancements in smart coatings (e.g., moisture sensors) and automated production (e.g., Starlinger’s AD*STAR® technology) driving efficiency. For brands, aligning with standards like ISO 17025 for lab testing ensures global competitiveness.
External Resources:
- Explore advancements in BOPP laminated woven bags for branding insights.
- Learn how Starlinger technology enhances production scalability.
This report synthesizes technical rigor and market insights to position laminated woven bags as a cornerstone of China’s packaging evolution.