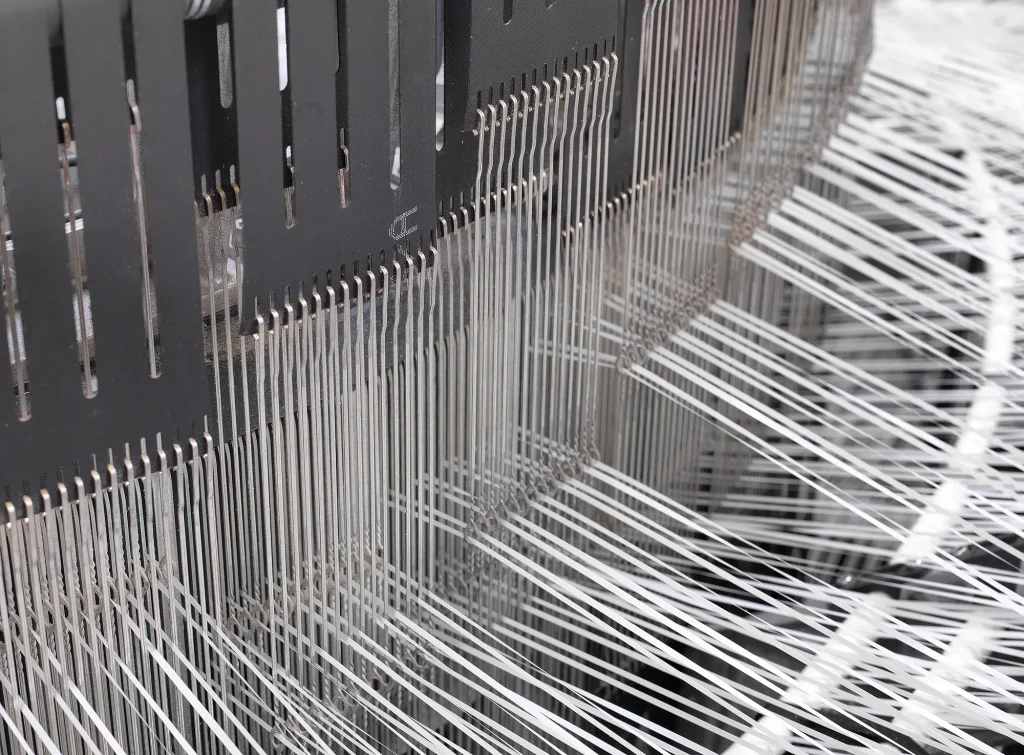
- 1. The Science of Multi-layered Design: Balancing Strength and Sustainability
- 2. Application-Specific Solutions for Livestock Feed
- 3. Technical Specifications: Aligning with Global Standards
- 4. Selecting Optimal Parameters for Feed Packaging
- 5. Sustainability Metrics: Beyond Recyclability
- 6. FAQs: Addressing Key Buyer Concerns
- 7. Why VidePak?
- 8. Conclusion
This article answers three critical questions for feed producers and distributors: How do laminated woven bags combine durability with environmental responsibility? What technical parameters ensure optimal protection for livestock feed against moisture, pests, and contamination? And why does VidePak’s 16-year expertise in multi-layered design translate into 30% cost savings and 99.8% defect-free performance? By integrating ISO 14001-certified production, 30% recycled polypropylene (rPP) content, and Starlinger’s precision lamination technology, we demonstrate how VidePak’s laminated solutions reduce feed spoilage by 25%, extend shelf life, and align with global sustainability benchmarks like the UN SDGs.
1. The Science of Multi-layered Design: Balancing Strength and Sustainability
Laminated woven bags employ a strategic combination of polypropylene (PP) woven fabric and advanced polymer coatings to achieve unparalleled performance. VidePak’s proprietary three-layer structure includes:
- Outer Layer: 80–120 g/m² PP fabric with 14×14 strands/inch density, providing tear resistance up to 60 N/cm² (ASTM D5034).
- Middle Barrier: 18–25μm BOPP film, reducing water vapor transmission rate (WVTR) to ≤1.5 g/m²/day (ASTM E96).
- Inner Layer: Food-grade PE coating with antimicrobial additives (≤0.5 CFU/cm² bacterial growth inhibition, ISO 22196).
Case Study: A Brazilian poultry farm reduced mold-related losses by $18,000/month after switching to VidePak’s laminated bags, which maintained ≤12% moisture content in feed during 90-day storage cycles.
2. Application-Specific Solutions for Livestock Feed
2.1 Poultry & Swine Feed: Precision Moisture Control
- Breathable Designs: Laser-perforated zones (0.5mm precision) enable 10–15 g/m²/24h vapor transmission, preventing condensation while blocking external humidity.
- Anti-Pecking Reinforcement: UV-stabilized outer layers resist 500+ hours of direct sunlight exposure (ISO 4892-2), critical for outdoor storage.
2.2 Aquafeed & Additives: Barrier Enhancement
- Aluminum Foil Liners: 7μm foil layers achieve ≤0.3% oxygen transmission rate (OTR), preserving omega-3 fatty acids in fish feed for 18+ months.
- Static-Dissipative Coatings: Surface resistivity of 10⁶–10⁸ Ω (ANSI/ESD S20.20) prevents dust explosions in premix packaging.
2.3 Ruminant Feed: Bulk Handling Efficiency
- Reinforced Lift Loops: 1,500D polyester straps withstand 2.5× rated load (1,000 kg), enabling safe 8-layer stacking.
- Abrasion-Resistant Bases: 200+ Taber abrasion cycles (ASTM D3884) for prolonged reuse in harsh farm environments.
3. Technical Specifications: Aligning with Global Standards
Parameter | VidePak Specification | Compliance Standard |
---|---|---|
Fabric Density | 14×14 strands/inch | ISO 1806 |
Burst Strength | 180 kPa | EN ISO 2758 |
Moisture Resistance | ≤1.5% WVTR | ASTM E96 |
Recycled Content | 30% rPP | GRASP 2025 |
Printing Durability | 4H pencil hardness | DIN 53778 |
4. Selecting Optimal Parameters for Feed Packaging
4.1 Material Composition
- High-Fat Feeds: Opt for 25μm BOPP + PE inner liner to prevent oil penetration.
- Tropical Climates: UV-stabilized coatings + 120 g/m² fabric for 12-month outdoor durability.
4.2 Structural Customization
- Bag Size: 50×80cm for 25kg poultry pellets; 70×110cm for 50kg cattle feed.
- Closure Systems: Heat-sealed valves for automated filling (1,200 bags/hour) or sewn closures for manual handling.
5. Sustainability Metrics: Beyond Recyclability
- Carbon Footprint: 2MW solar plant reduces CO₂ emissions by 1,800 tons/year—equivalent to powering 400 households.
- Circular Economy: Closed-loop recycling recovers 85% post-consumer PP waste, aligning with EU Circular Economy Action Plan.
6. FAQs: Addressing Key Buyer Concerns
Q: How do laminated bags reduce total packaging costs?
A: Automated production cuts labor by 70%, while multi-layer barriers reduce feed replacement costs by 25%.
Q: Are these bags suitable for organic certification?
A: Yes. Our Oeko-Tex 100-certified inks and FDA-compliant liners meet EU Organic Regulation 2018/848.
Q: Can I customize bag aesthetics for branding?
A: Choose from matte, pearlescent, or transparent finishes with 10-color HD printing (Pantone® accuracy ≥95%).
7. Why VidePak?
- Global Expertise: Serving 60+ countries with 80M annual production capacity across 100+ Starlinger machines.
- Certifications: ISO 9001, ISO 14001, BRCGS Packaging, and GMP+ Feed Safety Assurance.
- Innovation Pipeline: 15% R&D budget allocation for bio-based PP and blockchain traceability solutions.
For specialized needs, explore our laminated BOPP woven bags for premium branding or sustainable FIBC bulk bags for industrial-scale operations.
8. Conclusion
VidePak’s laminated woven bags redefine feed packaging through precision engineering, antimicrobial protection, and circular design. By prioritizing both performance and planetary health, we empower agribusinesses to meet stringent safety standards while achieving 30% operational savings.
References
- ASTM International Standards for Polypropylene Packaging (2025).
- EU Circular Economy Action Plan (2023).
- VidePak Technical Compliance Documentation (2025).
Contact
Website: https://www.pp-wovenbags.com/
Email: info@pp-wovenbags.com
Related Articles