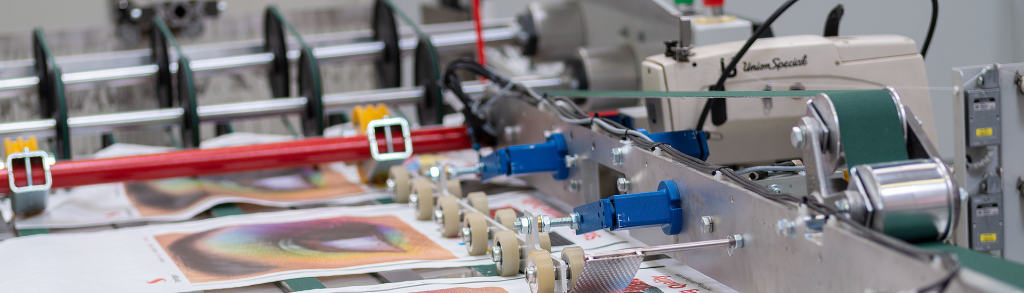
Lightweight woven bags represent the perfect synergy between cutting-edge innovation, regulatory compliance, and sustainability. These versatile packaging solutions address diverse industrial needs while advancing towards eco-friendly and cost-efficient practices.
The Evolution of Lightweight Woven Bags
Technological Advancements Driving Innovation
The lightweight woven bag industry has undergone remarkable transformations, largely driven by advancements in materials and production technologies.
- Material Innovations:
- Polypropylene (PP): Known for its lightweight and high tensile strength, PP is the cornerstone of woven bag production.
- High-Density Polyethylene (HDPE): HDPE’s flexibility and resistance to environmental stress make it a preferred choice for specific applications.
- Recycled Polymers: To meet growing sustainability demands, manufacturers increasingly use recycled materials without compromising bag performance.
- Manufacturing Techniques:
- Precision Weaving: Automated circular looms ensure consistent fabric quality and reduced material waste.
- Advanced Lamination: Multi-layer coatings provide added moisture and UV resistance, essential for outdoor storage.
- Seamless Integration of Ultrasonic Sealing: Eliminates stitching imperfections, enhancing strength and durability.
Current Market Trends and Global Characteristics
Automation and Smart Manufacturing
Automation has streamlined lightweight woven bag production, reducing operational costs and ensuring consistent quality. For instance, AI-driven quality control systems detect imperfections early in the manufacturing process, improving overall efficiency.
Sustainability Initiatives
The focus on environmental responsibility has led to the widespread adoption of recyclable and biodegradable materials in woven bags. Features like single-material construction simplify the recycling process, aligning with the global push for circular economies.
Global Market Dynamics
Region | Market Demands | Technical Focus |
---|---|---|
North America | High standards for branding and regulatory compliance. | Advanced printing technology for market differentiation. |
Europe | Emphasis on sustainability and minimal carbon footprint. | Use of recycled polymers and energy-efficient manufacturing. |
Asia-Pacific | Cost-effectiveness and scalability for agricultural uses. | Efficient production processes and durable coatings. |
Middle East & Africa | Resistance to extreme temperatures and bulk industrial needs. | UV-resistant materials and moisture-proof designs. |
Key Features and Advantages
Feature | Description | Advantages |
---|---|---|
Material Composition | Woven PP or HDPE, often laminated for added protection. | Lightweight, durable, and customizable. |
Load Capacity | Designed to hold weights up to 50 kg or more. | Suitable for both industrial and retail applications. |
Eco-Friendly Options | Bags made from recycled or single-material polymers. | Reduces environmental impact while maintaining quality. |
Customization | Options include size, color, lamination, and branding. | Tailored solutions for diverse market needs. |
For specialized uses, such as moisture-sensitive applications, woven bags with PE liners offer an excellent solution by combining durability with added protection.
Cost Management and Future Innovations
Controlling Production Costs
- Material Optimization: Advances in weaving technology reduce the amount of raw material required without sacrificing strength.
- Localized Sourcing: Procuring raw materials locally minimizes transportation costs and delays.
- Scalable Automation: Automated systems lower labor costs while increasing production throughput.
Anticipating Future Trends
- Smart Packaging: Incorporating RFID technology for inventory management and tracking.
- Biodegradable Alternatives: Enhanced focus on environmentally sustainable materials.
- 3D Printing in Customization: Using additive manufacturing for tailored bag designs and components.
FAQs About Lightweight Woven Bags
Q1: Are lightweight woven bags compliant with environmental regulations?
Yes, many lightweight woven bags are made from recyclable materials, aligning with global sustainability standards.
Q2: What industries benefit most from these bags?
They are widely used in agriculture, retail, construction, and logistics due to their versatility and durability.
Q3: Can these bags be customized?
Absolutely. Customizations include size, color, branding, and additional features like UV protection or lamination.
Q4: How do manufacturers ensure quality?
Quality control measures such as tensile strength testing, UV resistance evaluation, and thickness tolerance checks ensure high performance and reliability.
Q5: What certifications are available for these bags?
Lightweight woven bags often meet ISO standards for safety and performance, as well as specific certifications for food-grade or hazardous material packaging.
Regulatory Compliance and Quality Assurance
Manufacturers adhere to rigorous quality testing processes to ensure the reliability of lightweight woven bags. Common assessments include:
- Tensile Strength Testing: Verifies the bag’s ability to withstand heavy loads.
- UV Resistance Evaluation: Ensures durability in outdoor environments.
- Thickness Tolerance: Guarantees consistent material distribution to minimize waste.
- Food-Grade Certification: Required for packaging agricultural products and consumables.
Additionally, premium options like kraft paper bags laminated with woven fabric offer a sustainable yet durable alternative for eco-conscious industries.
Conclusion: The Role of Lightweight Woven Bags in a Sustainable Future
Lightweight woven bags have redefined packaging solutions across industries, offering unparalleled versatility, cost-efficiency, and sustainability. With continued advancements in automation and material science, these bags are poised to lead the market in aligning innovation with regulatory and environmental standards. Manufacturers like VidePak remain at the forefront, providing tailored solutions that cater to diverse global needs.