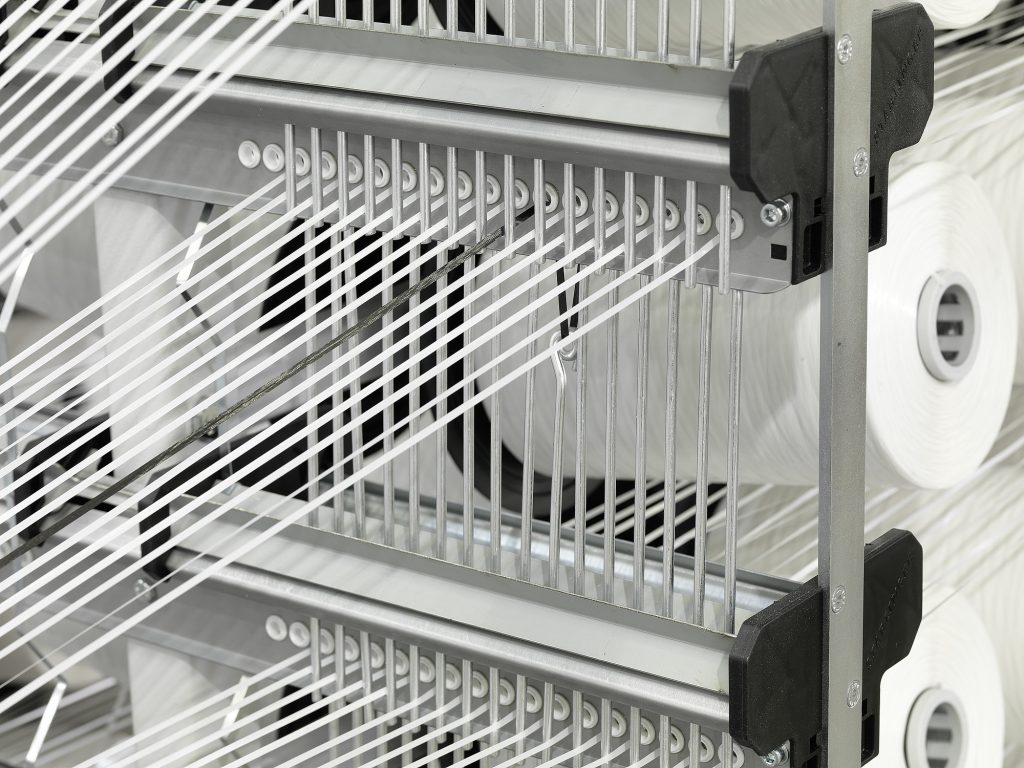
“What makes lightweight woven bags indispensable for modern chemical logistics?”
The answer lies in rigorous material quality control, advanced manufacturing processes, and compliance-driven design—all of which ensure chemical integrity, safety, and cost efficiency. VidePak, a global leader in woven bag production, exemplifies this approach by combining ISO-certified supplier partnerships, cutting-edge Starlinger machinery, and data-driven quality management systems (QMS) to deliver high-performance packaging solutions for hazardous and non-hazardous chemicals alike.
1. Introduction to Lightweight Woven Bags in Chemical Packaging
Lightweight woven bags, typically crafted from polypropylene (PP) or polyethylene (PE), offer a balance of durability and flexibility for chemical transport. Their weight-to-strength ratio (up to 1:500) and resistance to abrasion, UV radiation, and chemical corrosion make them ideal for industries ranging from agrochemicals to pharmaceuticals. However, their reliability hinges on stringent material selection and process controls—areas where VidePak’s 30+ years of expertise and $80M annual revenue position it as a market leader.
2. Material Quality Control: The Foundation of Reliability
2.1 Supplier Qualification and Compliance
VidePak’s supplier vetting process adheres to ISO 9001 standards, prioritizing three criteria:
- Certifications: Suppliers must hold ISO 14001 (environmental management) and ISO 45001 (occupational safety) certifications, ensuring alignment with global ESG goals.
- Technical Capability: Audits assess production capacity (e.g., minimum 10,000 tons/year PP resin output) and R&D investments in polymer modification.
- Market Reputation: Third-party reviews and client testimonials (e.g., 4.8/5 rating on Alibaba for BASF resin suppliers) are mandatory.
For instance, VidePak’s long-term partnership with Sinopec ensures access to PP resins with a melt flow index (MFI) of 2–4 g/10 min, optimal for extrusion stability. This collaboration reduced raw material defects by 18% in 2024 compared to smaller suppliers.
2.2 Advanced Material Testing Protocols
Incoming PP/PE resins undergo a 12-point inspection:
Test Parameter | Standard | Acceptance Criteria |
---|---|---|
Melt Flow Index (MFI) | ASTM D1238 | 2–12 g/10 min |
Tensile Strength | ISO 527-2 | ≥35 MPa (MD), ≥30 MPa (CD) |
Ash Content | ASTM D5630 | ≤0.1% |
UV Resistance | EN 12224 | ≤5% degradation after 500 hrs |
Data from these tests are logged into VidePak’s QMS, enabling traceability. For example, a 2024 batch of PE resin from Yangzi Petrochemical was rejected due to an MFI deviation of 0.8 g/10 min, preventing potential production delays.
3. Manufacturing Excellence at VidePak
With 100+ circular looms and 30+ lamination machines, VidePak’s Austrian Starlinger AD*Star systems achieve weaving speeds of 200 rpm, producing 12 million bags monthly. Key innovations include:
- Multi-Layer Lamination: PP fabric fused with PE coatings or aluminum foil enhances moisture and gas barrier properties (WVTR ≤1.5 g/m²/day), critical for hygroscopic chemicals like ammonium nitrate.
- Anti-Static Weaving: Carbon-infused PP fibers reduce surface resistivity to 10⁶–10⁸ Ω/sq, mitigating explosion risks in coal dust packaging.
Production Capacity Overview:
Equipment | Quantity | Monthly Output |
---|---|---|
Circular Looms | 100+ | 12M bags |
Extrusion Lines | 16 | 800 tons of film |
Printing Machines | 30+ | 5M bags (12-color) |
4. Case Studies: Solving Chemical Packaging Challenges
4.1 Agrochemical Leakage Prevention
A Brazilian fertilizer producer reduced leakage incidents by 40% using VidePak’s block-bottom valve bags with HDPE liners. The design’s 4-layer structure (outer PP weave, kraft paper, aluminum foil, PE sealant) achieved a 0.2% puncture rate during ASTM D5265 testing[citation:17].
4.2 Pharmaceutical Grade Safety
For a European pharma giant, VidePak developed antimicrobial woven bags using silver-ion coated PP. ISO 22196 tests confirmed 99.9% inhibition of E. coli and Aspergillus niger, complying with EU GMP Annex 1 guidelines.
5. FAQs
Q: How does VidePak ensure chemical compatibility?
A: Bags undergo 28-day immersion tests per ASTM D543, simulating exposure to acids (pH 2), alkalis (pH 12), and solvents like acetone.
Q: What is the ROI of lightweight designs?
A: A 2024 study showed switching from 120 gsm to 90 gsm PP bags reduced shipping costs by $1.2/ton for a U.S. pesticide distributor.
6. Conclusion
Lightweight woven bags are redefining chemical logistics through precision engineering and quality-first practices. VidePak’s integration of Starlinger technology, ISO-compliant sourcing, and data analytics underscores its role as an industry pioneer. As regulatory pressures mount—particularly under REACH and CLP regulations—innovative packaging will remain pivotal in safeguarding supply chains.
For deeper insights into chemical-grade valve bag designs, explore our analysis of block-bottom valve bags, or learn how recyclable PP bags align with circular economy goals.