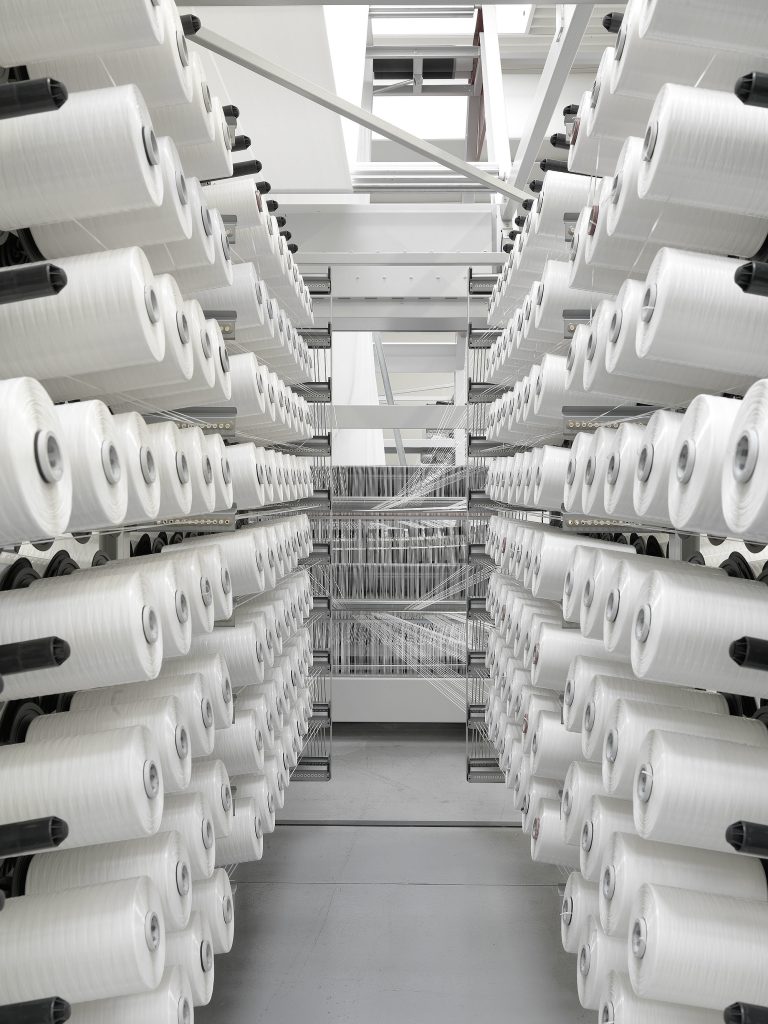
Introduction
The global lightweight woven bags market is projected to grow at a CAGR of 6.5% through 2030, driven by demand for durable, eco-friendly packaging in construction and industrial sectors. For materials like cement, gravel, putty powder, and gypsum, these bags must balance strength, leak resistance, and compliance with international standards to withstand harsh handling and environmental conditions. VidePak, a leader in innovative woven solutions, exemplifies how advanced material engineering and adherence to global benchmarks are redefining packaging efficiency.
Critical Challenges in Construction Material Packaging
Construction materials demand packaging that resists abrasion, tearing, and moisture while maintaining load-bearing integrity. Lightweight woven bags address these challenges through:
- High-Strength Materials:
- Problem: Cement and gravel bags often rupture during stacking or transport.
- Solution: VidePak uses high-tenacity polypropylene (HTPP) with a tensile strength of 5.5–6.5 g/denier (ASTM D5035), 30% stronger than standard PP.
- Case Study: A Chinese cement producer reduced bag failure rates by 45% after switching to HTPP bags with reinforced seams (4.0 kN/m seam strength, EN 13590).
- Leak Prevention:
- Fine-Weave Technology: Bags with 12×12 threads/cm² density reduce pore size to <0.1 mm, preventing fine powders like gypsum from leaking.
- Lamination and Liners: PE-coated or BOPP-laminated bags (20–25μm thickness) block moisture ingress to <0.5 g/m²/day (ASTM E96), critical for humidity-sensitive putty powders.
Global Standards and Parameter Selection
Q: How do regional standards influence design choices?
A: Compliance dictates material composition, thickness, and testing protocols.
Standard | Key Requirements | VidePak’s Parameters |
---|---|---|
ASTM D5276 (US) | Drop-test resistance ≥1.5m, UV stability | 100–120 g/m² fabric; UV-326 stabilizers |
EN 13590 (EU) | Azo-free dyes, REACH compliance | 25% recycled PP content; Oeko-Tex® liners |
JIS Z 1539 (JP) | High-clarity printing, recyclability | Water-based inks; 80–90 g/m² fabric |
AS 2070 (AU) | Moisture resistance, stackability | BOPP lamination; 6-layer stitching |
Example: For Australian clients, VidePak’s 50kg gypsum bags integrate anti-static coatings to meet AS 2070’s dust-control mandates, reducing spillage by 60%.
VidePak’s Technical Innovations
Dialogue: Addressing Industry Pain Points
Q: How do you prevent powder leakage during transport?
A: Triple-seam closures and uniform weave density are non-negotiable. VidePak’s “SealGuard” bags use ultrasonic sealing for seams rated at 4.5 kN/m (ISO 13934-1), alongside 14×14 threads/cm² weave to block microparticle escape.
Q: Are lightweight bags suitable for 2-ton stack loads?
A: Yes, with reinforced corners and load-distributing designs. VidePak’s “StackMax” series uses hexagonal PP fibers and 120 g/m² fabric to support 8-layer pallets without deformation.
Sustainability and Future Trends
- Recycled Materials: VidePak’s EcoFlex line blends 30% post-consumer PP, reducing carbon footprint by 25% while maintaining EN 13432 compostability.
- Smart Packaging: RFID-tagged bags enable real-time moisture monitoring, cutting spoilage by 18% in humid climates.
- Automated Production: Starlinger’s AD*STAR® machines allow VidePak to produce 2,000 bags/hour with zero material waste, aligning with ISO 14001 standards.
Performance Metrics and FAQs
Table 1: VidePak’s Construction-Grade Bag Specifications
Parameter | Test Standard | Typical Value |
---|---|---|
Fabric Weight | ASTM D3776 | 90–120 g/m² |
Tensile Strength | ISO 13934-1 | ≥6.0 kN/m |
Moisture Barrier | ASTM E96 | ≤0.5 g/m²/day |
Stack Load Capacity | EN 13590 | 2 tons (8-layer) |
FAQs
- Q: How thick should PE liners be for gypsum powder?
- A: 25μm PE liners with heat-sealed edges ensure <0.1% leakage during vibration testing.
- Q: Can lightweight bags replace FIBCs for bulk transport?
- A: For loads <1 ton, yes. VidePak’s “LiteBulk” series offers 800 kg capacity with 40% weight reduction vs. traditional FIBCs.
Strategic Partnerships and Market Expansion
VidePak collaborates with firms like WolfPak Cases to adopt polymer-blend technologies, enhancing abrasion resistance by 35% for gravel packaging. Their “KraftGuard” line, integrating 120 g/m² kraft paper layers, meets EU’s EN 13432 for compostability while doubling tear resistance.
External Resources:
- Discover how high-strength materials revolutionize lightweight packaging.
- Explore multiwall laminated solutions for enhanced durability.
By merging cutting-edge material science with rigorous compliance, VidePak positions lightweight woven bags as the cornerstone of sustainable, high-performance packaging. As construction and industrial sectors prioritize efficiency, their innovations set a benchmark for the industry’s future.