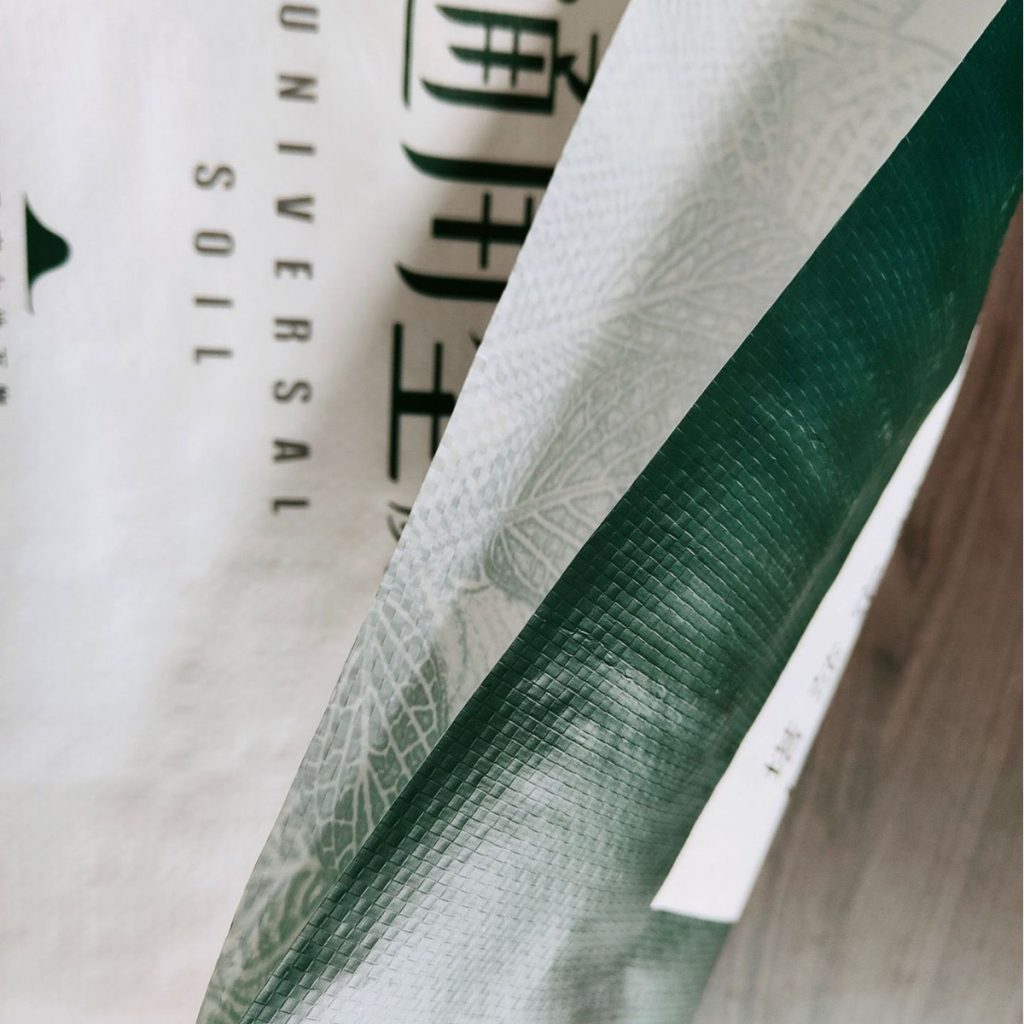
Introduction
SOM PP Fabric Bags are transforming the packaging industry with their exceptional design and functionality. Known as SOM Bags or Sewn Open Mouth Bags, these versatile bags offer superior durability and ease of use, making them ideal for various applications. This report explores the different types of SOM sacks, the stringent quality control and standardization processes, and the role of advanced equipment from Starlinger in ensuring top-notch quality. By utilizing new PP and PE particles, adequate product thickness, and specialized printing techniques, Woven Bag Manufacturers are setting new standards in the industry.
Types of SOM PP Fabric Bags
Understanding the different types of SOM Bags is crucial for selecting the right bag for your needs.
1. Standard SOM Bags
Standard SOM Bags feature a simple sewn open mouth design, perfect for general bulk packaging.
Example: A grain distributor uses SOM sacks to transport large quantities of wheat. The sewn open mouth allows for easy filling and pouring, reducing handling time and improving efficiency.
2. Reinforced SOM Bags
Reinforced Sewn Open Mouth Woven Bags are designed for heavier loads, providing extra strength and durability.
Example: A construction materials supplier opts for reinforced SOM Bags to package cement. These bags can withstand the heavy weight without tearing, ensuring safe transportation and storage.
3. Custom Printed SOM Bags
Custom printed Open Mouth Bags offer branding opportunities while maintaining functionality.
Example: A beverage company uses custom printed Sewn Open Mouth Woven Bags for packaging their raw materials. The durable printing process ensures that logos and information remain clear and vibrant throughout the product’s lifecycle.
Quality Control and Standardization
High-quality SOM Bags are essential for reliability and customer satisfaction. Key quality control measures include using superior materials, precise manufacturing processes, and advanced equipment.
1. Use of New PP and PE Particles
High-grade polypropylene (PP) and polyethylene (PE) particles enhance the strength and durability of SOM Bags.
Example: A chemical manufacturer chooses SOM sacks made from new PP and PE particles. This ensures the bags are resistant to tearing and can handle harsh chemicals without degrading.
2. Sufficient Product Thickness
Adequate thickness prevents bag rupture and extends the lifespan of the bags, especially when handling heavy or abrasive materials.
Example: A fertilizer producer selects Sewn Open Mouth Bags with increased thickness. This prevents the bags from rupturing during transport, ensuring safe and efficient delivery of fertilizers.
3. Positive Tolerance Standards
Adhering to positive tolerance standards ensures that all bag dimensions meet specified criteria, eliminating defects and ensuring consistency.
Example: A pharmaceutical manufacturer relies on SOM Bags that comply with positive tolerance standards. This ensures precise packaging, minimizing material wastage and maintaining high product quality.
4. Preventing Package Failures
Strict quality control and reinforced materials help prevent package failures, ensuring safety during handling and storage.
Example: An explosive materials distributor uses SOM Bags with reinforced seams and proper ventilation. This prevents pressure buildup, ensuring safe transportation of explosive materials.
5. Special Printing Processes
Advanced printing techniques ensure that labels and branding on the bags remain clear and durable, even under harsh conditions.
Example: A beverage company uses Sewn Open Mouth Woven Bags with UV-resistant printing. This prevents the print from fading during long storage periods, maintaining brand visibility.
6. Starlinger Equipment for Stability
Using advanced equipment from suppliers like Starlinger ensures consistent and high-quality production of SOM Bags.
Example: A leading Woven Bag Manufacturer partners with Starlinger to utilize their full suite of equipment. This guarantees uniform quality and minimizes production errors, enhancing customer trust and satisfaction.
Dialogue: Ensuring Quality in SOM Bags
Client: “How do your Sewn Open Mouth Bags prevent leaks and ensure durability?”
Manufacturer: “We use high-grade PP and PE particles combined with sufficient product thickness. Additionally, our bags adhere to positive tolerance standards and are produced using Starlinger’s advanced equipment, ensuring consistent quality and reliability.”
Selecting the Right SOM PP Fabric Bags Parameters and Design
Choosing the appropriate SOM Bags involves considering various factors to meet specific needs and comply with industry standards.
Key Parameters:
Parameter | Description | Importance |
---|---|---|
Material Thickness | Ensures durability and load capacity | Prevents tearing and extends bag lifespan |
Valve Type | Determines ease of use and application | Matches specific packaging requirements |
Closure Mechanism | Method of sealing the valve (e.g., sewn) | Prevents leakage and contamination |
Printing Quality | Durability and resistance of printed labels | Maintains branding and information clarity |
Manufacturing Standards | Adherence to positive tolerance and safety standards | Ensures consistency and safety in packaging |
Example: A fertilizer producer in India selects SOM PP Fabric Bags with reinforced thickness and high-quality printing. These features ensure the bags can handle heavy loads, prevent leaks, and maintain clear labeling throughout the supply chain.
FAQs
Q1: What are SOM Bags used for?
A1: SOM Bags are used for packaging and transporting bulk materials such as grains, fertilizers, chemicals, and construction materials. Their sewn open mouth design allows for easy filling and dispensing, enhancing efficiency.
Q2: How do Sewn Open Mouth Woven Bags prevent leakage?
A2: Sewn Open Mouth Woven Bags use secure sewn closures that tightly seal after filling. This design prevents leaks and contamination, ensuring the integrity of the packaged materials.
Q3: Why choose a Woven Bag Manufacturer with Starlinger equipment?
A3: Using Starlinger’s advanced equipment ensures high-quality, consistent production of SOM Bags. This results in durable, reliable bags that meet stringent quality standards.
Comparative Analysis of SOM Bag Types
Bag Type | Durability | Ease of Use | Cost | Ideal Use Case |
---|---|---|---|---|
Standard SOM Bags | High | Easy to use | Low | General bulk packaging |
Reinforced SOM Bags | Very High | Moderate ease | Medium | Heavy materials like cement and chemicals |
Custom Printed SOM Bags | High | Easy to use | Higher | Branding and product identification |
Conclusion
SOM Bags, including SOM sacks and Sewn Open Mouth Woven Bags, are essential for efficient and safe packaging in various industries. By understanding different types of valves and implementing rigorous quality control measures, Woven Bag Manufacturers can produce reliable and high-performance bags. Utilizing advanced materials, adhering to positive tolerance standards, and employing specialized printing processes ensure that Open Mouth Bags meet the highest quality standards. Partnering with reputable manufacturers that use Starlinger’s equipment further enhances product stability and trust. As industries demand more efficient and sustainable packaging solutions, SOM Bags will remain indispensable in meeting these evolving needs.
For more information on aligning SOM Bags with sustainability standards, visit SOM Bags. To explore advanced manufacturing processes and expertise in Sewn Open Mouth Bags, check out Sewn Open Mouth Bags.
Additional FAQs
Q4: How can businesses ensure their SOM Bags meet quality standards?
A4: Businesses should work with reputable Woven Bag Manufacturers who use high-grade materials and advanced equipment. Regular quality inspections and compliance with international standards also help maintain high quality.
Q5: What are the environmental benefits of using Sewn Open Mouth Bags?
A5: Sewn Open Mouth Bags are reusable and recyclable, reducing the need for single-use packaging and minimizing environmental impact. Their durability also means fewer replacements and less waste overall.
References:
- Industry reports on polypropylene packaging
- Research papers on valve technology in packaging
- International standards for woven bags
- Case studies from leading construction and agricultural companies