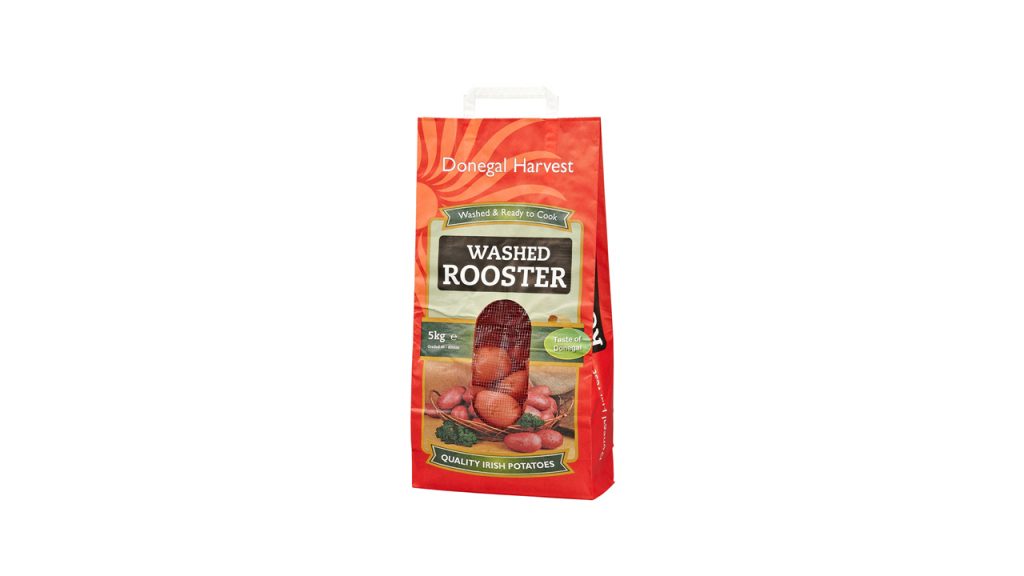
Answer in Brief: By utilizing multi-wall woven bags featuring layered lamination and customizable printing, industries achieve excellent durability, moisture resistance, and eye-catching branding—ensuring goods arrive in prime condition and stand out in competitive markets.
In an era of rapid global trade and rising consumer expectations, packaging solutions must balance robust protection, cost-efficiency, and brand differentiation. According to a 2024 survey by the International Packaging Research Council, multi-wall woven sacks, Laminated Woven Bags, Laminated PP Bags, and Multiwall Woven Bags continue to prove indispensable for various applications, from fertilizers and pet food to grains and industrial powders. This report investigates two crucial aspects: (1) the inherent advantages of multi-layered woven packaging, and (2) the capacity for extensive customization in size, thickness, and color printing.
1. Why Select Multi-wall Woven Bags
Multi-wall woven bags differ from single-layer polypropylene (PP) or paper sacks by combining multiple layers of material—often polypropylene, kraft paper, BOPP film, or other specialty liners. These layers collectively boost the packaging’s protective qualities while keeping weight in check.
1.1 Multi-layer Benefits
- Enhanced Moisture and Contaminant Barrier
- Example: A Canadian fertilizer exporter replaced standard PP sacks with multi-wall woven sacks featuring a moisture-blocking film. Post-adoption, they observed a notable 25% dip in caking incidents, maintaining product consistency under high-humidity conditions.
- Superior Structural Strength
- Laminations reinforce the fabric’s tear resistance and puncture tolerance, reducing product loss and contamination risks during transport.
- Example: A chemical manufacturer that switched to multi-wall packaging reported a 30% drop in ruptured sacks, saving on labor and cleanup expenses.
- Optimal Weight-to-Strength Ratio
- Layered structures prevent the need for excessively thick material, striking a balance between load capacity and manageable weight.
- Example: A European rice mill, seeking to reduce logistics costs, turned to a 2-layer PP + film approach for 50 kg bags, lowering overall packaging weight by 10% without compromising tear strength.
- Extended Shelf Life and Print Durability
- Lamination shields printed graphics against abrasions and moisture, preserving brand imagery over prolonged storage.
- Example: A premium pet food supplier found that their brand colors on Laminated PP Bags retained vibrancy for six months on the shelf, driving consistent consumer recognition.
- Adaptable Material Combinations
- Firms can incorporate specialized layers—such as BOPP or foil—to address specific challenges like odor containment, UV shielding, or advanced printing.
- Example: A seed distributor employed an aluminum-foil inner layer to mitigate light exposure, improving seed vitality by roughly 15% over non-laminated bags.
2. Tailored Dimensions and Printing Options
Multiwall Woven Bags thrive on their scalability in size, weave density, and personalization—allowing producers to match exact product, branding, or logistical requirements.
2.1 Customizing Sizes and Weave
- Modular Bag Dimensions
- From small 5 kg pouches to 50+ kg bulk sacks, manufacturers can fine-tune dimensions for ease of transport, pallet configuration, and compatibility with filling machinery.
- Example: An animal feed brand standardized 25 kg Laminated Woven Bags for their mainstream line, yet used 10 kg variants for specialty blends, maintaining consistent visuals across SKUs.
- Weave Density and Fabric Weight
- Selecting finer threads yields smoother textures for detailed printing, while coarser weaves enhance air permeability—beneficial for certain agricultural uses.
- Example: A coffee exporter wanting a refined aesthetic opted for a 10×10 weave, enabling high-definition printing while delivering the structural integrity needed for global shipping.
- Balancing Thickness and Flexibility
- Multi-wall layering can be optimized so that each layer contributes to strength and barrier properties without making the bag overly rigid.
- Example: A flour mill introduced a single-film lamination on top of a PP base, boosting tear resistance by 15% while preserving the bag’s flexibility for pallet stacking.
2.2 Full-spectrum Printing (CMYK, Pantone, RAL)
A key selling point of Laminated Woven Bags is their capacity to host vibrant, full-coverage designs.
- Broad Color System Support
- Whether a brand employs the CMYK process for photorealistic images, Pantone for precise brand colors, or RAL references for industrial labeling, laminated surfaces accommodate varied color needs.
- Example: A lawn care products company insisted on strict Pantone matching across all packaging, uniting brand identity and global retail consistency.
- All-over “Full-bleed” Printing
- Laminated PP Bags commonly allow designs that wrap around the entire bag, capturing attention from every angle on store shelves.
- Example: A dog food brand printed colorful product graphics across the entire 20 kg bag, reinforcing the premium image while boosting shopper engagement.
- Fade-resistant Inks
- UV-resistant or fade-proof formulations help the printed exterior remain sharp despite exposure to sunlight or indoor lighting.
- Example: A fertilizer manufacturer storing bags outdoors reduced color fading by 40% thanks to specialized UV coatings on the laminated film.
- Detailed Imagery and Branding
- Rotogravure and flexographic presses now produce crisp text and intricate photos—turning once-generic packaging into a compelling marketing asset.
- Example: A specialty grain exporter used near-photographic images of farmland on Laminated Woven Bags, emphasizing premium quality and traceable origins.
3. Technical Parameters at a Glance
Parameter | Typical Range/Spec | Influence on Performance |
---|---|---|
Fabric Weight (g/m²) | 60–120 g/m² | Balances tear strength, cost, and portability |
Laminate Layers | 1–3 extra films or liners | Greater moisture barrier, printing clarity, and tensile strength |
Weave Density | 8×8 to 14×14 threads/inch | Affects texture, breathability, and print quality |
Thickness | 0.10–0.25 mm (cumulative) | Dictates load-bearing capacity, handling ease |
Printing Colors | CMYK, Pantone, RAL | Ensures brand consistency and vibrant designs |
Closure Methods | Sewing, heat sealing, valves | Alters leak prevention, reusability, and automation compatibility |
Capacity Range | 5–50+ kg | Suitable for varied goods, from grains to bulk powders |
Example: A feed manufacturer needed a 50 kg capacity with a 10×10 weave, a single BOPP laminate, and Pantone-matched inks. The result? Reinforced seams, bright brand colors, and minimal tearing issues during forklift transport.
4. Conversation Snippets
Topic: “Why choose multi-wall woven bags for humid conditions?”
Answer: Multiple layers—such as PP fabric plus film laminates—help keep moisture out, protecting items like fertilizer, flour, or seeds. The layered structure also heightens tear resistance, a vital asset during long-distance hauling.
Topic: “How does all-around printing on Multiwall Woven Bags impact brand visibility?”
Answer: Full-bleed printing covers every side, instantly capturing shopper attention. Coupled with robust lamination, it upholds vibrant colors and detailed artwork—even when stored in challenging environments.
5. FAQs
- Q: Do multi-wall woven sacks cost more than single-layer options?
A: Generally, yes. The added layers and lamination steps increase production costs, though the gains in durability and print quality often justify the investment. - Q: Can I adjust the bag’s stiffness with lamination?
A: Absolutely. Various film choices yield different flexibility levels, letting you fine-tune the balance between rigidity and ease of handling. - Q: How eco-friendly are Laminated PP Bags?
A: Polypropylene fabrics are typically recyclable, but the extra layers may need specific recycling streams. Some manufacturers now offer eco-friendlier films or partial lamination designs. - Q: Is special equipment required to fill laminated sacks?
A: Most standard filling lines can handle them, but you might need minor tension and sealing adjustments for optimum throughput. - Q: Can these multi-layer bags handle rough materials?
A: Yes. Reinforced structures are particularly suited for abrasive goods like minerals, construction aggregates, or feed pellets, minimizing puncture-related losses.
Conclusion
By combining multi-layer lamination, fine-tuned weaving parameters, and advanced color printing, multi-wall woven bags, multi-wall woven sacks, Laminated Woven Bags, Laminated PP Bags, and Multiwall Woven Bags excel in both functionality and visual appeal. Whether safeguarding moisture-sensitive products, preserving brand graphics for extended shelf time, or accommodating heavy industrial loads, these solutions check all the boxes.
With flexible thickness options, rigorous color-matching, and a range of capacity choices, manufacturers can tailor packaging to their specific needs—whether it’s a niche pet food product or large-scale fertilizer distribution. As sustainability considerations grow, many producers investigate recyclable films, partial laminations, or lighter-weight substrates to reduce environmental impact. In a competitive global marketplace, investing in layered woven packaging can differentiate your brand, boost product reliability, and streamline logistics—ultimately reinforcing trust among distributors, retailers, and consumers alike.