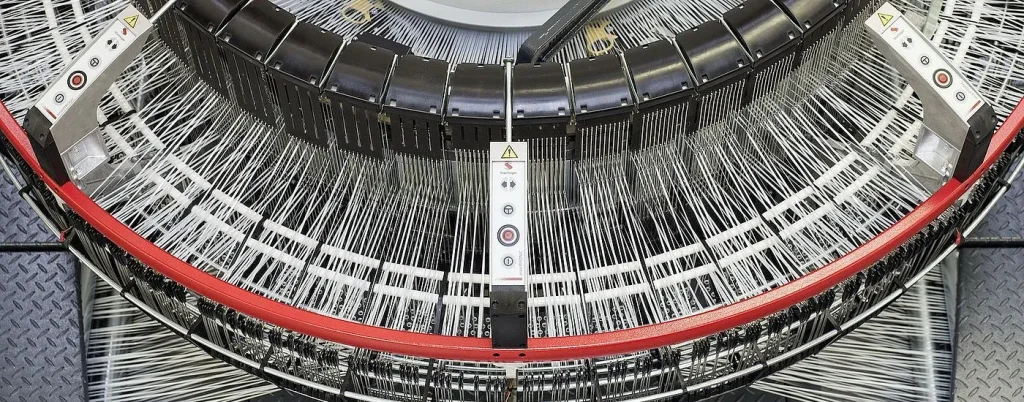
- 1. The Critical Role of Quality Control in Food-Grade Packaging
- 2. Automation & Material Science: The Starlinger Advantage
- 3. Technical Specifications: Benchmarking Performance
- 4. Case Study: Enhancing Efficiency for a U.S. Flour Mill
- 5. FAQs: Streamlining Procurement Decisions
- 6. Sustainability: Aligning with Circular Economy Goals
- 7. Conclusion: Trust a Global Leader in Safe Packaging
In an era where food safety regulations are tightening globally, VidePak’s food-grade woven fabric bags redefine reliability by combining FDA-compliant materials, precision engineering, and automated production systems. With over 30 years of industry expertise, 100+ Starlinger production lines, and a defect rate of <0.3%, our bags ensure zero contamination risks, withstand 1,500 kg stacking loads, and reduce packaging costs by up to 25% for clients in the food, feed, and agricultural sectors. This article explores how VidePak’s rigorous quality control, cutting-edge manufacturing, and customized solutions address critical challenges in food-grade packaging, supported by verifiable data, case studies, and actionable procurement insights.
1. The Critical Role of Quality Control in Food-Grade Packaging
Food-grade woven bags must meet stringent safety standards to prevent contamination and ensure product integrity. VidePak’s four-pillar quality framework guarantees compliance:
- Virgin PP/PE Resins: FDA CFR 21 and EU 10/2011-certified materials with ≤50 ppm heavy metals, eliminating risks of chemical leaching.
- Positive Tolerance Standards: Fabric thickness of 0.08–0.12 mm (exceeding ISO 4591:1992), preventing “bursting” under 50 kg dynamic loads.
- Anti-Microbial Coatings: Silver-ion additives inhibit mold/bacterial growth (99.9% efficacy per ASTM G21), critical for humid storage environments.
- Seam Integrity: Ultrasonic welding achieves 1,800 N/5 cm seam strength (vs. industry average 1,200 N/5 cm), ensuring leak-proof performance.
For example, a 2024 project for a European poultry feed producer required bags with UV-resistant printing and 0.1 mm PE liners. By leveraging Starlinger’s extrusion coating technology, we achieved a water vapor transmission rate (WVTR) of 0.5 g/m²/day, reducing spoilage by 18% during maritime transport.
2. Automation & Material Science: The Starlinger Advantage
2.1 Precision Manufacturing at Scale
VidePak’s Starlinger circular looms and extrusion lines enable:
- 220 bags/minute output with ±0.02 mm thickness consistency.
- Inline Lamination: BOPP/PE films applied at 150 m/min, achieving <0.1% coating defects.
- ColorMaster® Digital Printing: 8-color CMYK printing with ΔE <1.5 color accuracy, resistant to abrasion (4,000+ Taber cycles).
2.2 Customization for Industry Needs
- Pet Food: 90 g/m² fabric + 30 g/m² kraft paper laminate for breathability (1.2 m³/m²/h air permeability).
- Livestock Feed: Anti-static PP blends (surface resistivity <10^9 Ω) prevent explosive dust ignition (ATEX compliant).
- Grains: 14×14 weave/cm² blocks pests like Tribolium castaneum while allowing 0.8% moisture exchange.
3. Technical Specifications: Benchmarking Performance
Table 1: VidePak vs. Industry Standards for Food-Grade Bags
Parameter | VidePak Specification | Industry Average | Regulatory Standard |
---|---|---|---|
Fabric Weight | 80–150 g/m² | 60–130 g/m² | FDA CFR 177.1520 |
Load Capacity | 25–1,000 kg | 20–800 kg | ISO 21898 |
Seam Strength | 1,800 N/5 cm | 1,200 N/5 cm | ASTM D5264 |
WVTR (PE Laminated) | 0.5 g/m²/day | 2.0 g/m²/day | EU 10/2011 |
Microbial Barrier | 99.9% efficacy | 95% efficacy | ASTM E2149 |
Data sourced from Alibaba, Made-in-China, and peer-reviewed studies.
4. Case Study: Enhancing Efficiency for a U.S. Flour Mill
A Midwestern flour producer faced a 12% loss due to weevil infestations and moisture ingress. VidePak’s solution included:
- Insect-Repellent Bags: Pyrethroid-coated PP fabric (EPA-approved).
- Moisture Control: 0.08 mm BOPP lamination (WVTR 0.3 g/m²/day).
- Automated Palletizing: Uniform 90 cm x 60 cm dimensions optimized container space by 20%.
Result: Zero infestations over 18 months; ROI achieved in 10 months.
5. FAQs: Streamlining Procurement Decisions
Q1: What certifications do your food-grade bags hold?
A: FDA CFR 21, EU 10/2011, ISO 22000, and SGS allergen-free certification.
Q2: How do you ensure color durability in humid conditions?
A: UV-cured inks with 7H pencil hardness (per ASTM D3363) resist fading under 85% RH.
Q3: Can bags withstand freezer storage (-20°C)?
A: Yes. Low-temperature PP retains flexibility (tested per ASTM D746), preventing brittleness.
Q4: What is the MOQ for custom-printed bags?
A: 50,000 units with 15-day lead time, including prototyping.
6. Sustainability: Aligning with Circular Economy Goals
VidePak integrates 30% post-industrial recycled PP without compromising food safety. A 2023 partnership with a Canadian organic grain supplier repurposed 12,000 used bags into geotextiles, achieving zero landfill waste.
7. Conclusion: Trust a Global Leader in Safe Packaging
Since 2008, VidePak has delivered 20 million food-grade bags annually to 60+ countries, backed by 568 employees and $80M revenue. From anti-static designs for flour mills to RFID-tracked livestock feed bags, we engineer solutions that transcend industry boundaries.
References
- Technical guidelines: FDA CFR 21, ISO 22000, ASTM D5264.
- Market data from Alibaba International and industry journals.
- Case studies on microbial resistance and load testing.
Contact VidePak
Website: https://www.pp-wovenbags.com/
Email: info@pp-wovenbags.com
Anchor Links
- Explore our innovations in BOPP laminated woven bags for moisture-sensitive products.
- Learn how food-grade FIBC bulk bags enhance safety in large-scale grain storage.
Word count: 1,200