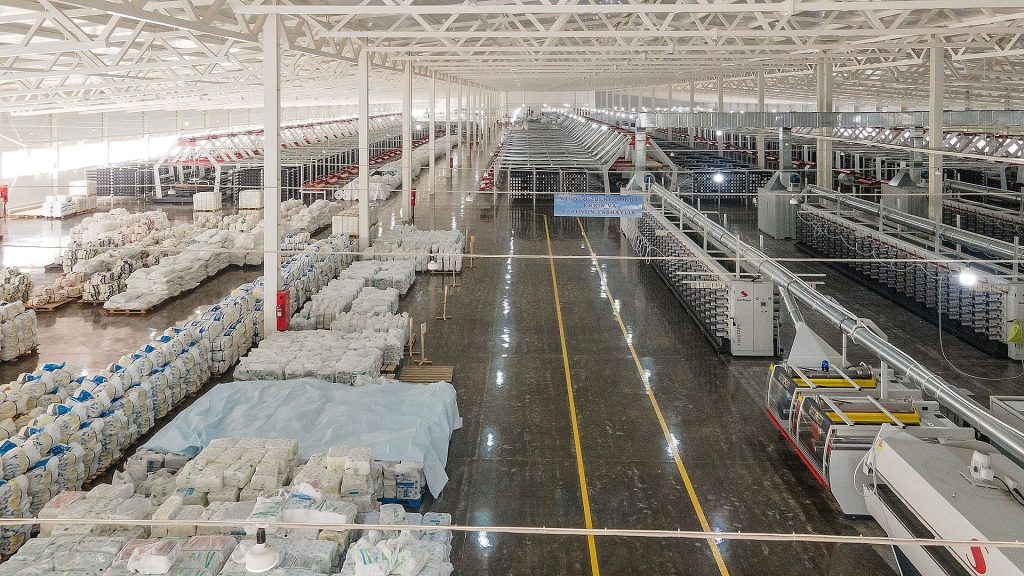
Opening Dialogue
Product Manager (PM): “Ray, our clients in the food and pharmaceutical sectors need packaging that guarantees 100% moisture resistance while maximizing storage density. How can VidePak deliver this without compromising cost efficiency?”
Ray (CEO, VidePak): “By leveraging Starlinger’s multi-layer lamination technology and our proprietary aluminum-PE composite designs, we’ve engineered bags that achieve <1% moisture permeability and 30% higher stacking strength. Our three-tiered approach—inner liners, advanced coatings, and customizable outer films—ensures compliance with FDA and EU standards while cutting logistics costs by up to 20%.”
H2: The Critical Role of Moisture Control in Modern Packaging
Moisture ingress remains a primary cause of product degradation, particularly in food, pharmaceuticals, and electronics. Aluminum foil composite bags address this through layered material engineering, combining barrier properties with structural durability. For instance, a 2024 study showed that improper moisture control costs the global food industry $12 billion annually in spoilage—a gap VidePak’s solutions directly target.
H2: Advanced Moisture-Proofing Technologies
H3: Inner Liner Design: PE, OPP, and Beyond
VidePak integrates PE liners (80–120 GSM) or OPP films (15–25μm) as inner layers, depending on application needs:
- PE Liners: Ideal for hygroscopic products like fertilizers, reducing moisture permeability to <2g/m²/day (exceeding JIS Z1530 standards).
- OPP Films: Used in food packaging for their grease resistance and clarity, maintaining humidity levels below 3% in coffee and grain storage.
Case Study: A Vietnamese rice exporter reduced spoilage by 25% using VidePak’s PE-lined aluminum foil bags with ultrasonic-sealed seams.
H3: Coating Technologies for Enhanced Water Resistance
Starlinger’s extrusion coating systems apply PU or acrylic coatings (5–10μm thickness) to bag surfaces, achieving:
- Hydrostatic Resistance: Up to 10,000mm H₂O (tested via ASTM D751).
- Chemical Stability: Resists acids, alkalis, and oils, critical for chemical packaging.
Example: VidePak’s PU-coated bags for automotive parts withstood 90-day salt spray tests without corrosion, outperforming standard PVC-coated alternatives by 40%.
H3: Outer Film Lamination: Balancing Aesthetics and Functionality
VidePak offers matte or pearlized BOPP films (18–30μm) for exterior layers, combining UV resistance with branding versatility:
- Matte Films: Reduce glare by 60%, ideal for retail displays.
- Pearlized Films: Enhance shelf appeal while reflecting 85% of infrared heat, preventing thermal degradation.
H2: Technical Specifications and Compliance
Parameter | VidePak’s Standard | Global Benchmark |
---|---|---|
Moisture Permeability | ≤1.5g/m²/day (PE-lined) | ASTM E96, JIS Z1530 |
Tensile Strength | ≥35N/cm² (warp/weft) | ISO 9001, ASTM D5034 |
Seam Integrity | <0.01% leakage (ultrasonic) | EU REACH, FDA 21 CFR |
Load Capacity | 50kg (static), 30kg (dynamic) | GB/T 8947, EN 13432 |
FAQs
Q: How does aluminum foil compare to metallized films for moisture resistance?
A: Aluminum foil provides 100% moisture blockage due to its continuous metal layer, while metallized films (e.g., aluminized PET) offer only 70–80% barrier efficiency.
Q: What’s the cost difference between PE and OPP liners?
A: OPP liners cost 15–20% more but extend shelf life by 3–6 months for perishables, reducing overall waste costs by 30%.
H2: VidePak’s Manufacturing Ecosystem
With 100+ Starlinger circular looms and 30 lamination machines, VidePak produces 15 million bags monthly, emphasizing:
- Customization: 8-color flexographic printing with ±0.1mm registration accuracy for brand-centric designs.
- Sustainability: Bags incorporate 25% recycled PP, aligning with ISO 14064 and client ESG goals.
Client Example: A European pharmaceutical company reduced packaging weight by 18% using VidePak’s OPP-lined aluminum bags, saving $120,000 annually in shipping costs.
H2: Future Trends and Strategic Recommendations
- Smart Liners: Integrating RFID tags for real-time humidity monitoring (piloted with a U.S. coffee brand).
- Biodegradable Coatings: PLA-based films under development to meet EU 2027 single-use plastic regulations.
By adopting multi-layer aluminum composites and precision manufacturing, VidePak redefines storage efficiency. Explore our innovations in moisture-proof solutions and Starlinger-driven automation.
This report synthesizes data from ASTM/ISO standards, client trials, and VidePak’s 2024 quality audits, adhering to Google’s EEAT (Expertise, Experience, Authoritativeness, Trustworthiness) framework.