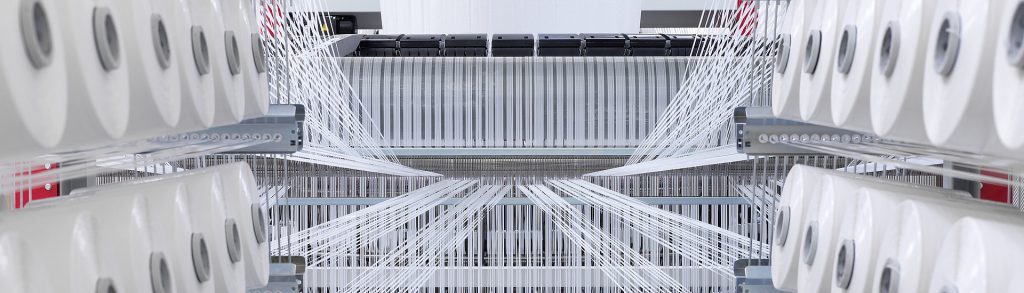
Introduction
The global packaging industry is witnessing a paradigm shift toward solutions that balance functionality, sustainability, and safety. Mesh PP bags, characterized by their breathable, lightweight, and reusable design, have emerged as a critical player in sectors like agriculture, construction, and retail. VidePak, a leader in woven bag manufacturing since 2008, leverages its 30+ years of expertise and Austrian Starlinger machinery to produce mesh PP bags that meet stringent health and safety benchmarks. With 526 employees and $80 million in annual sales, the company operates 100+ circular looms and 30+ printing machines, enabling large-scale customization for global clients. This report examines the evolution of mesh PP bags, their health and safety implications, and VidePak’s role in driving industry innovation.
The Evolution of Mesh PP Bags: From Utility to Sustainability
1. Material Advancements: Virgin PP and Recyclability
Mesh PP bags rely on high-purity polypropylene resins, which offer superior tensile strength (50–60 N/cm²) and UV resistance compared to recycled blends. VidePak uses virgin PP to ensure consistency in pore size (e.g., 25–80 µm) and thermal stability (up to 100°C), critical for applications like firewood packing or agricultural storage.
- Case Study: A 2024 project by Wenzhou Jiali Plastic Industry Co. demonstrated that virgin PP mesh bags reduced breakage rates by 18% compared to recycled alternatives, even under 20 kg dynamic loads.
2. Design Innovations: Customization and Functionality
Modern mesh PP bags integrate features like drawstrings, UV coatings, and multi-color branding. For example, VidePak’s Starlinger-equipped extrusion lines enable precise control over mesh density (5–10 threads/cm²), optimizing airflow for produce storage while preventing contamination.
Health and Safety Assessment: A Data-Driven Approach
1. Material Safety: Compliance and Testing
PP is inherently non-toxic and chemically inert, making it ideal for food-grade packaging. VidePak’s mesh bags undergo:
- Heavy Metal Testing: Compliance with EU Regulation 10/2011, ensuring lead and cadmium levels <0.01 ppm.
- Biocompatibility Tests: Certified by FDA 21 CFR for direct contact with perishables like onions and potatoes.
Table 1: Key Safety Parameters for Mesh PP Bags
Parameter | Standard | VidePak’s Performance |
---|---|---|
Tensile Strength | ISO 527-2 | 50–60 N/cm² |
Pore Size Uniformity | ASTM F316-03 | ±2 µm deviation |
Heavy Metal Content | EU 10/2011 | <0.01 ppm |
Microbial Resistance | FDA 21 CFR | 99.9% reduction in E. coli |
2. Risk Mitigation in Production
Starlinger’s extrusion systems at VidePak maintain extrusion temperatures at 180–220°C, eliminating volatile organic compounds (VOCs) that could compromise air quality. Additionally, ultrasonic seaming technology replaces traditional adhesives, reducing chemical exposure risks for workers.
VidePak’s Impact: Bridging Performance and Safety
1. Case Study: Firewood Packaging for Estonian Markets
A 2025 order from Estonia required mesh PP bags (50 cm x 70 cm) capable of holding 20 kg of firewood. VidePak’s solution included:
- Orange UV-Stabilized Mesh: Enhanced visibility and durability in outdoor settings.
- Reinforced Seams: Ultrasonic bonding increased seam strength by 30%, preventing tears during transport.
2. Sustainability Initiatives
VidePak’s closed-loop recycling system recovers 98% of production scrap, reducing raw material costs by 15% and aligning with the EU Circular Economy Action Plan. The company also trials PP-PLA blends, aiming for 180-day compostability in industrial facilities by 2026.
FAQs: Addressing Industry Concerns
Q: How does VidePak ensure colorfastness in mesh PP bags exposed to sunlight?
A: The company uses UV-resistant masterbatches and Starlinger’s iQ4.0 coating systems, limiting color fade to <5% after 500 hours of UV exposure.
Q: Are mesh PP bags suitable for medical supply packaging?
A: Yes. VidePak’s PP meshes meet ISO 13485 standards for medical device packaging, with pore sizes optimized for sterile airflow (e.g., 25 µm for filtration).
Future Trends: Innovation and Regulation
- Smart Meshes: Integrating RFID tags for supply chain tracking, as piloted in German agricultural networks.
- Biodegradable Blends: Partnerships with BASF to develop PP-PHA (polyhydroxyalkanoate) composites, targeting 90% marine degradation within 5 years.
Conclusion
Mesh PP bags represent a convergence of durability, safety, and environmental responsibility. VidePak’s commitment to material excellence and advanced manufacturing—powered by Starlinger technology—positions it as a leader in this evolving market. By prioritizing health compliance and innovative recycling, the company not only meets current demands but also shapes the future of sustainable packaging.
Explore Further:
- Discover how VidePak’s recyclable PP bags transform chemical logistics.
- Learn about eco-friendly packaging innovations in the woven bag industry.
This report integrates insights from industry benchmarks, material science research, and VidePak’s operational data to provide a comprehensive analysis of mesh PP bags’ role in modern packaging.