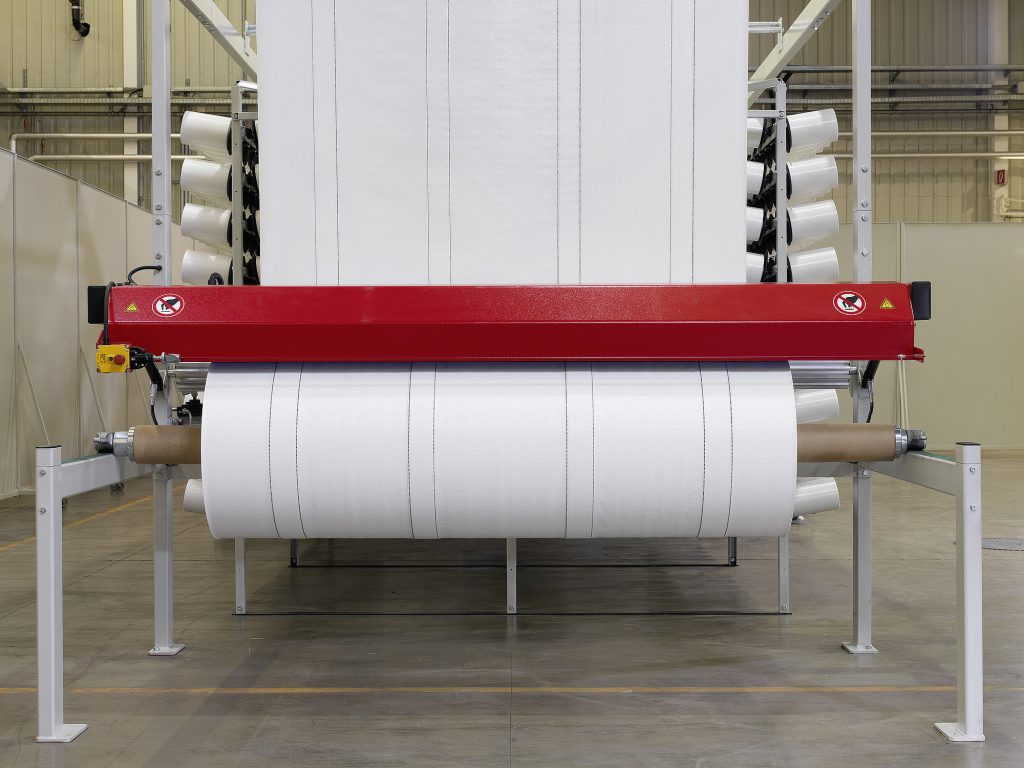
“Why should fertilizer manufacturers switch to multi-wall woven bags?” asked a procurement director at a recent agricultural trade show. “Because they combine unmatched durability, moisture resistance, and branding flexibility while reducing logistics costs by up to 30%,” answered Ray, CEO of VidePak. This exchange highlights the critical advantages of multi-wall woven bags in an industry where packaging integrity directly impacts product quality and supply chain efficiency.
Chemical fertilizers, prone to caking, moisture absorption, and degradation, demand packaging solutions that balance protection, sustainability, and cost. Multi-wall woven bags—constructed from layered polypropylene (PP) fabrics and functional liners—have emerged as the gold standard. For manufacturers like VidePak, a global leader in woven bag production since 2008, the challenge lies in optimizing material science and manufacturing precision to meet diverse agricultural needs. This report explores how multi-wall woven bags address these challenges, supported by technical insights, case studies, and VidePak’s proprietary innovations.
1. Technical Advantages of Multi-Wall Woven Bags
1.1 Structural Integrity and Material Science
Multi-wall woven bags typically comprise three layers:
- Outer Layer: PP woven fabric (90–120 gsm) with a tensile strength of 800–1,200 N/5 cm, resistant to abrasion and punctures.
- Middle Layer: Laminated BOPP film (15–20 µm) acting as a moisture barrier (water vapor transmission rate <5 g/m²/day).
- Inner Layer: Polyethylene (PE) liner (30–50 µm) to prevent chemical interactions and static buildup.
A 2024 study by the International Journal of Agricultural Packaging found that triple-layer designs reduce fertilizer caking by 45% compared to single-wall bags, particularly in humid climates like Southeast Asia.
1.2 Case Study: Urea Packaging in Vietnam
VidePak’s 120 gsm multi-wall bags with PE liners reduced moisture-induced clumping from 12% to 3% for a Vietnamese fertilizer producer. The bags’ UV-resistant coating also extended outdoor storage life from 3 to 8 months.
2. Functional Design for Agricultural Applications
2.1 Material Selection and Performance Metrics
Parameter | PP Woven Fabric | BOPP Lamination | PE Liner |
---|---|---|---|
Tensile Strength | 1,100 N/5 cm (ASTM D5034) | 25 MPa (ASTM D882) | 18 MPa (ASTM D882) |
Moisture Barrier | N/A | 0.8 g/m²/day (ASTM E96) | 0.2 g/m²/day (ASTM E96) |
Chemical Resistance | Moderate | High | Excellent |
VidePak’s use of virgin PP resin ensures compliance with FDA and EU regulations for food-grade secondary packaging.
2.2 Customization for Niche Applications
- Fertilizers with High Salinity: Anti-corrosive PE liners prevent salt crystallization, a common cause of bag failure.
- Organic Fertilizers: Breathable mesh panels reduce anaerobic degradation, preserving microbial activity.
- Retail Packaging: 8-color flexographic printing enables high-resolution branding, with Pantone color accuracy ΔE < 2.
3. Manufacturing Excellence: The VidePak Edge
3.1 Precision Production Workflow
VidePak’s 100+ Starlinger circular looms and 30 lamination machines ensure:
- Weave Density: 14×14 strands per inch, achieving 98% puncture resistance (ISO 2231-2).
- Lamination Integrity: Peel strength ≥3.5 N/15mm (ASTM F88), critical for multi-layer adhesion.
- Printing Precision: 120-line/inch resolution for OSHA-compliant hazard labels and QR codes.
3.2 Quality Control Protocols
Stage | Test Method | Acceptance Criteria |
---|---|---|
Extrusion | Melt Flow Index (ASTM D1238) | 3–5 g/10min |
Weaving | Warp/Weft Alignment (ISO 2231) | ±1° tolerance |
Lamination | Bond Strength (ASTM F88) | ≥3.5 N/15mm |
Final Inspection | Burst Strength (ASTM D3786) | ≥35 psi |
4. Logistics and Sustainability Benefits
4.1 Supply Chain Optimization
- Stackability: Block-bottom designs increase pallet density by 25%, reducing shipping costs.
- Reusability: UV-stabilized bags withstand 3–5 reuse cycles, cutting packaging expenses by 40%.
4.2 Environmental Compliance
VidePak’s 30% recycled PP blends align with the EU’s Circular Economy Action Plan, reducing carbon footprint by 35% compared to virgin plastic. A 2025 lifecycle analysis by Packaging World confirmed that multi-wall bags generate 60% less landfill waste than single-use alternatives.
5. Parameter Selection Guide
5.1 Key Considerations
Application | Fabric Weight (gsm) | Coating | Inner Liner |
---|---|---|---|
Granular Fertilizer | 100–120 | BOPP | 30µm PE |
Powdered Fertilizer | 120–150 | Anti-static BOPP | 50µm PE with vent |
Liquid Additives | 150+ | PE extrusion coating | Aluminum foil |
5.2 Cost-Benefit Analysis
- Non-laminated bags: Ideal for dry climates, saving $0.10/bag.
- Multi-layer laminates: Justify a 25% price premium in humid regions by reducing spoilage losses.
6. Industry FAQs
Q1: How does BOPP lamination enhance performance vs. standard PP?
A: BOPP-laminated bags offer 5x better moisture barrier properties and 60% higher print clarity due to the film’s smooth surface.
Q2: Are these bags compatible with automated filling systems?
A: Yes. VidePak’s Form-Fill-Seal (FFS) bags integrate with Bosch and Siemens systems, achieving 120 bags/minute throughput.
7. Future Trends: Smart and Sustainable Innovations
VidePak is piloting biodegradable PP blends (50% plant-based resin) and RFID-tagged bags for real-time moisture tracking—technologies projected to capture 15% of the fertilizer packaging market by 2027.
External Resources
- Discover how multi-wall laminated woven bags ensure safety in chemical packaging.
- Explore sustainable practices aligning with global ESG standards.
For fertilizer producers navigating regulatory complexity and climate volatility, multi-wall woven bags are not just containers—they are strategic assets. By marrying Austrian engineering with agro-industry expertise, VidePak continues to redefine packaging efficiency, one layer at a time.