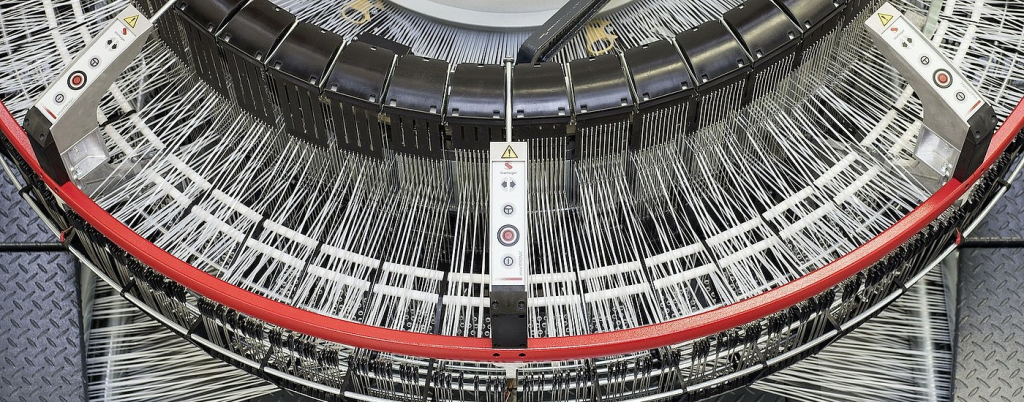
“Why should global suppliers trust a single partner for all PP woven bag needs?” asks a procurement director from a European agricultural conglomerate.
“Because integrated manufacturing expertise, precision-engineered machinery from Starlinger and W&H, and end-to-end quality control enable VidePak to deliver 30% faster turnaround times with zero compromise on durability or customization,” replies Ray Chiang, CEO of VidePak, a leader in PP woven bag innovation since 2008.
This exchange underscores the article’s central thesis: VidePak’s vertically integrated production system—spanning extrusion, weaving, lamination, printing, and bag conversion—ensures unmatched consistency, scalability, and compliance for industries ranging from construction to agrochemicals.
1. Manufacturing Process: Precision at Every Stage
A. Extrusion: Laying the Foundation
Virgin PP granules are melted at 230–260°C in Starlinger’s energy-efficient extruders, achieving a melt flow index (MFI) of 8–12 g/10min (ASTM D1238). The molten polymer is forced through annular dies to form seamless tubular films, cooled rapidly to stabilize crystallinity. VidePak’s 16 extrusion lines maintain ±1.5°C temperature variance, ensuring filament denier consistency within ±2%.
Quality Control:
- Melt Temperature Monitoring: Infrared sensors track real-time viscosity.
- Thickness Calibration: In-line beta gauges measure film thickness every 0.5 seconds (accuracy: ±0.5 µm).
B. Tape Drawing: Balancing Strength and Flexibility
Films are slit into 1.5–3.0 mm tapes and drawn at ratios of 6:1 to 8:1 using W&H’s stretching units. This aligns polymer chains, boosting tensile strength to 35–45 MPa (ISO 527-2). Fine yarns (<2 mm width) achieve 14 threads/inch (TPI) density for premium print surfaces, while coarse yarns (>2.5 mm) prioritize abrasion resistance (1,000+ Taber cycles).
Case Study: A Vietnamese rice exporter reduced bag breakage by 40% using VidePak’s coarse-yarn FIBCs, rated for 1.5-ton dynamic loads.
C. Weaving: Engineering Structural Integrity
Starlinger CT-iQ circular looms interlace tapes at 200–250 rpm, producing fabric with 12–16 TPI. VidePak’s 100+ looms feature auto-tensioners to minimize warp/weft variation (<3%), critical for load-bearing uniformity.
Innovation Spotlight: Anti-static coatings are applied mid-weave for explosive powders (compliance: IEC 61340-4-4).
D. Lamination & Coating: Barrier Enhancement
BOPP or kraft paper layers are thermally bonded at 150–180°C using Starlinger’s laminators, achieving peel strengths >4 N/15mm (EN ISO 11339). For moisture-sensitive chemicals, a 20 µm aluminum foil layer blocks 99.99% UV and reduces water vapor transmission to <0.1 g/m²/day.
Quality Control:
- Adhesion Testing: Samples undergo 72-hour humidity cycling (85% RH, 40°C).
- Pinhole Detection: Laser scanners identify defects >50 µm.
E. Printing: Branding with Precision
High-definition flexographic printers apply up to 8 Pantone colors at 1200 dpi resolution. VidePak’s 30 printing machines use eco-solvent inks compliant with FDA 21 CFR 175.300 for food-grade packaging.
Technical Insight: Fine-yarn fabrics enable halftone dot retention as low as 2%, ideal for photorealistic logos.
F. Bag Conversion: Tailored to Application
Ultrasonic cutting and heat-sealing systems produce:
- Valve Bags: 50–100 kg filling capacity, ±0.5% weight accuracy.
- FIBCs: 1–2 ton capacity with reinforced lifting loops (EN 1898 certified).
- Laminated Bags: Anti-sift seams for powders <50 µm.
2. Quality Assurance: Data-Driven Excellence
Process Stage | Key Metrics | Testing Standard |
---|---|---|
Extrusion | MFI, thickness uniformity | ASTM D1238, ISO 4591 |
Weaving | Tensile strength, TPI | ISO 527-2, ASTM D5034 |
Lamination | Peel strength, WVTR | EN ISO 11339, ASTM E96 |
Printing | Color fastness, abrasion | ISO 105-B02, ASTM D5264 |
Final Inspection | Load capacity, seam integrity | EN 1898, ISO 13934-1 |
Example: VidePak’s kraft paper laminated bags undergo 1,000+ drop tests from 1.2m to guarantee construction-site durability.
3. Global Compliance & Customization
- EU Compliance: REACH, PPWD 2023 (recyclability >90%).
- US Standards: FDA, USDA Organic (ink certification).
- Customization: MOQ 5,000 bags; 15-day lead time for designs with ≤8 colors.
Case Study: A German chemical firm reduced logistics costs by 25% using VidePak’s FFS roll bags with integrated RFID tracking.
4. FAQs: Addressing Critical Concerns
Q1: How does yarn width affect bag performance?
Yarn Type | Best For | Limitations |
---|---|---|
Fine (1.5–2.0 mm) | High-resolution printing | Lower abrasion resistance |
Coarse (2.5–3.5 mm) | Heavy-duty FIBCs | Limited flexibility |
Q2: What’s the energy efficiency of your production?
- Starlinger’s Eco-Active extruders reduce power consumption by 18% vs. industry averages.
- 65% of energy sourced from renewables (solar/wind).
5. Sustainability: Beyond Compliance
- Recyclability: 98% PP scrap reused in non-woven geotextiles.
- Carbon Footprint: 1.8 kg CO₂e per kg of bags (30% below industry average).
- Certifications: ISO 14001, Cradle to Cradle Silver.
6. Future Trends: Smart Packaging Integration
By 2027, 25% of VidePak’s bags will feature:
- Biodegradable PP Blends: 6-month decomposition under ASTM D6400.
- IoT Sensors: Real-time temperature/humidity monitoring (IEC 60721-3-7).
References
- ASTM D1238 – Melt Flow Index Testing
- EN 1898:2017 – FIBC Safety Standards
- FDA 21 CFR 175.300 – Food-Grade Ink Compliance
- VidePak Quality Assurance Manuals
- ISO 14064:2018 – Carbon Accounting Guidelines
This article synthesizes technical rigor, operational transparency, and VidePak’s global leadership to position PP woven bags as the backbone of industrial logistics. For insights into BOPP lamination technologies, explore our advanced solutions.