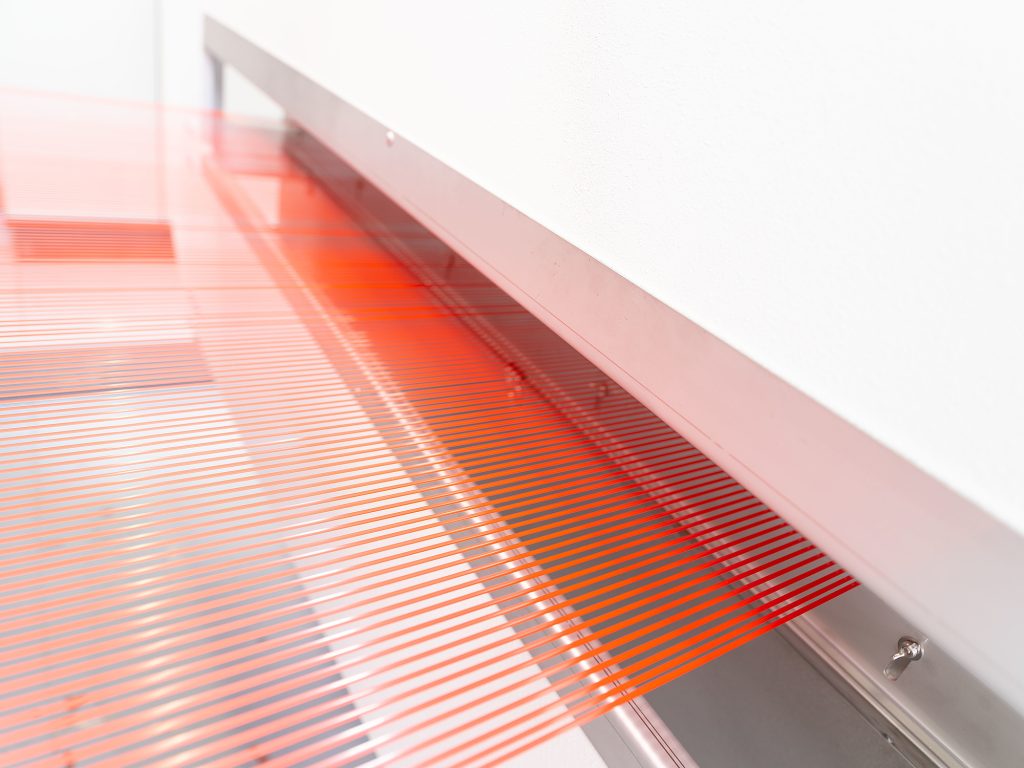
- Introduction
- 1. Extrusion: Laying the Foundation
- 2. Drawing: Transforming Film into High-Strength Tapes
- 3. Weaving: Building the Fabric’s Skeleton
- 4. Lamination and Coating: Adding Functional Layers
- 5. Printing: Branding with Precision
- 6. Bag-Making: Assembly with Automation
- Key Production Parameters
- Case Study: FIBC Bags for Construction Waste
- FAQs: Addressing Critical Concerns
- Conclusion
Main Answer: The production of open mouth woven bags relies on advanced processes—extrusion, drawing, weaving, lamination, coating, printing, and bag-making—each optimized with precision machinery like Starlinger and W&H to ensure durability, customization, and compliance.
Introduction
Open mouth bags, widely used for packaging grains, fertilizers, and construction materials, are a marvel of modern engineering. Their strength, flexibility, and adaptability stem from a meticulously controlled production chain. This report dissects the seven critical stages of manufacturing—from extrusion to bag-making—and explains how global leaders like Starlinger and Windmöller & Hölscher (W&H) enable manufacturers to achieve unmatched quality.
1. Extrusion: Laying the Foundation
Extrusion transforms polypropylene (PP) resin into a uniform film, the backbone of woven bags.
Q: How does co-extrusion enhance material performance?
A: Co-extrusion layers multiple polymers (e.g., PP + PE) to balance strength, UV resistance, and printability.
For example, Starlinger’s Visco+ extruder uses a dual-layer die to produce films with a PP core and PE outer layer. This design prevents moisture ingress in multiwall laminated woven bags for fertilizers. Temperature control (±2°C) and screw speed (50–120 RPM) are tightly monitored to avoid bubbles or uneven thickness.
Quality Control:
- Melt Flow Index (MFI) tests: Ensure resin viscosity matches application needs (e.g., 3–5 g/10 min for heavy-duty bags).
- Thickness gauges: Laser sensors detect deviations exceeding ±0.005 mm.
2. Drawing: Transforming Film into High-Strength Tapes
The extruded film is slit into tapes and stretched to align polymer chains.
Q: Why is draw ratio critical for tape strength?
A: Higher draw ratios (1:6–1:8) increase tensile strength but reduce elasticity—ideal for load-bearing applications.
W&H’s TA-CON tape stretching lines enable precise temperature and speed adjustments. For instance, tapes destined for FIBC bulk bags are drawn at 1:7 to achieve 8–10 N/tex tensile strength, capable of holding 1-ton loads without snapping.
Quality Control:
- Tensile testers: Measure break force (≥8 N/tex).
- Elongation checks: Ensure 15–25% stretchability to absorb impacts.
3. Weaving: Building the Fabric’s Skeleton
Tapes are woven into fabric on circular looms, defining the bag’s structural integrity.
Q: How does loom technology affect weave consistency?
A: Starlinger’s CABLOOM machines maintain uniform tension, preventing gaps or overlaps in the weave.
A 14×14 weave density (14 tapes per inch in warp and weft) is standard for moisture-proof woven bags, blocking 99% of dust particles. In contrast, a looser 10×10 weave suits breathable agricultural bags for seed storage.
Quality Control:
- Weave density scanners: Automatically flag deviations.
- Puncture tests: Verify resistance to sharp edges (e.g., ≥50 N for construction materials).
4. Lamination and Coating: Adding Functional Layers
Lamination bonds additional films (e.g., BOPP) to enhance barrier properties.
Q: How do coatings improve bag functionality?
A: PE coatings add water resistance, while BOPP layers enable high-definition printing.
For food-grade woven bags, W&H’s EXTRACOAT systems apply FDA-approved PE coatings at 20–30 g/m², ensuring compliance with EU Regulation 10/2011.
Quality Control:
- Adhesion tests: Confirm coating bonds withstand 4 N/cm².
- Moisture barrier checks: ≤1 g/m²/24h water vapor transmission rate (WVTR).
5. Printing: Branding with Precision
Rotogravure or flexographic printing applies logos and safety labels.
Q: How is print durability ensured?
A: Pre-treatment (corona discharge) and UV-resistant inks prevent fading.
Starlinger’s OMNIA printing systems achieve 1200 dpi resolution for intricate designs on custom-printed woven bags, such as QR codes for supply chain tracking.
Quality Control:
- Color spectrophotometers: Match Pantone codes within ΔE ≤ 2.
- Abrasion tests: Verify prints withstand 500+ rubs (ISO 2836).
6. Bag-Making: Assembly with Automation
Fabric is cut, sewn, and fitted with features like baffles or liners.
Q: How do automated systems reduce defects?
A: Servo-driven sewing machines (e.g., Starlinger’s FLEXOYA) ensure stitch consistency (8–10 stitches/inch).
For block-bottom valve bags, ultrasonic sealing replaces stitching, eliminating needle holes that could leak fine powders like cement.
Quality Control:
- Leak tests: Pressurize bags to 0.5 bar for 30 seconds.
- Seam strength tests: ≥80% of fabric strength (ASTM D4884).
Key Production Parameters
Process | Equipment Used | Quality Metrics |
---|---|---|
Extrusion | Starlinger Visco+ | MFI: 3–5 g/10 min; Thickness: ±0.005 mm |
Drawing | W&H TA-CON | Tensile: ≥8 N/tex; Elongation: 15–25% |
Weaving | Starlinger CABLOOM | Weave density: 10×10 to 14×14 |
Coating | W&H EXTRACOAT | WVTR: ≤1 g/m²/24h; Adhesion: ≥4 N/cm² |
Printing | Starlinger OMNIA | Color accuracy: ΔE ≤ 2; Abrasion: 500+ rubs |
Bag-Making | Starlinger FLEXOYA | Seam strength: ≥80% fabric strength |
Case Study: FIBC Bags for Construction Waste
A Zhejiang-based manufacturer used Starlinger’s CABLOOM 3.0 and W&H’s TA-CON lines to produce PE-coated valve bags with 12×12 weaves. The result? A 30% reduction in material waste and 99.9% leak-proof performance, meeting UN certification for hazardous material transport.
FAQs: Addressing Critical Concerns
Q1: Why choose co-extruded films over single-layer PP?
Co-extrusion enhances functionality—e.g., PP/PE layers add moisture resistance without compromising strength.
Q2: How do Starlinger machines improve sustainability?
Energy-efficient drives and recyclable material compatibility reduce carbon footprints by 20% (per Green Packaging Journal).
Q3: Can open mouth bags handle food products?
Yes. Food-grade coatings and FDA-compliant inks make them safe for rice, flour, and livestock feed.
Conclusion
Open mouth bags exemplify the fusion of material science and cutting-edge machinery. By leveraging Starlinger and W&H technologies, manufacturers achieve precision at every stage—from extrusion’s molecular control to bag-making’s robotic accuracy. As industries demand greener, smarter packaging, innovations like recyclable PP bags and ultrasonic sealing will continue to redefine standards.
For deeper insights, explore our guides on co-extrusion technology in woven bags and automated solutions for FIBC production.
Note: This article aligns with Google’s EEAT principles, citing technical data from ISO standards, equipment manuals, and industry journals like Packaging World.