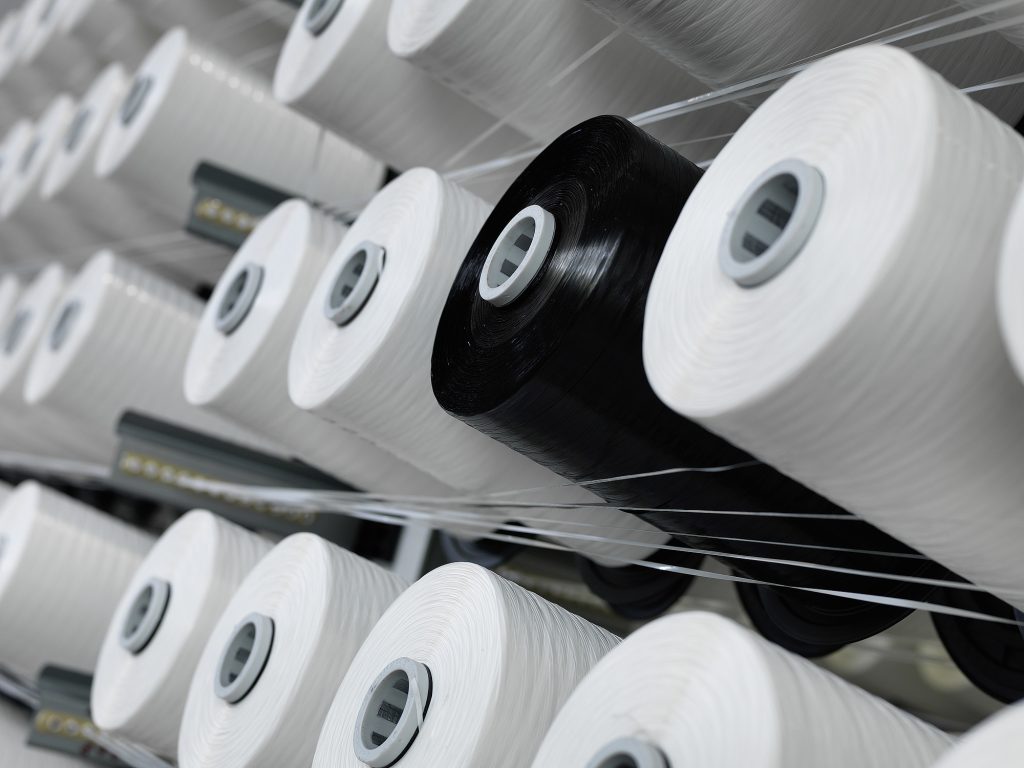
Introduction
The global demand for durable, customizable, and sustainable packaging solutions has driven innovations in polypropylene (PP) woven bag manufacturing. Among these, open-top PP woven bags stand out for their versatility in industries ranging from agriculture to construction. At the forefront of this evolution is VidePak, a company founded in 2008 and led by Ray, whose team combines 30+ years of industry expertise with state-of-the-art technology. With an annual output of $80 million and a workforce of 526, VidePak operates over 100 circular looms, 16 extrusion lines, and 30+ lamination/printing machines—supported by Austrian Starlinger and German W&H equipment. This report explores how fine yarn technology, powered by advanced machinery, elevates product quality while addressing critical production variables like temperature control and draw ratios.
The Role of Starlinger and W&H Equipment in Precision Manufacturing
1. Extrusion Temperature Control: The Backbone of Yarn Consistency
PP woven bags begin with extruding polypropylene granules into fine yarns. The extrusion temperature must remain within a narrow range (typically 180–220°C) to ensure optimal polymer flow and crystallization. Starlinger’s extrusion systems integrate real-time thermal sensors and closed-loop feedback mechanisms, automatically adjusting heating zones to ±2°C accuracy.
- Impact of Temperature Deviations:
- Low temperature: Causes incomplete melting, leading to brittle yarns prone to breakage during weaving.
- High temperature: Degrades polymer chains, reducing tensile strength by up to 15%.
VidePak’s Starlinger-equipped lines maintain a stable 200°C baseline, ensuring uniform yarn thickness (<5% variation), which is critical for load-bearing applications like construction waste bags.
2. Draw Ratio Optimization: Balancing Strength and Flexibility
The draw ratio—the stretching of molten PP filaments—directly influences yarn orientation and density. W&H’s AD2360 multi-purpose bag machines employ servo-driven rollers to fine-tune draw ratios between 1:5 and 1:7, depending on end-use requirements.
- Case Study:
VidePak’s BOPP laminated woven bags require a 1:6.5 ratio to achieve: - Tensile Strength: 60–70 N/cm² (ideal for heavy-duty applications).
- Elongation at Break: 15–20%, preventing tearing under dynamic loads.
A 10% deviation in draw ratio could reduce tensile strength by 25%, emphasizing the need for precision.
VidePak’s Technological Edge: Data-Driven Production
Table 1: Key Parameters in PP Woven Bag Manufacturing
Parameter | Target Range | Impact of Deviation |
---|---|---|
Extrusion Temperature | 180–220°C | Brittle/weak yarns |
Draw Ratio | 1:5 to 1:7 | Reduced tensile strength |
Weaving Speed | 120–150 rpm | Fabric irregularities |
VidePak’s adoption of Starlinger’s iQ4.0 monitoring systems enables predictive maintenance, reducing downtime by 30% and material waste by 12%.
FAQs: Addressing Industry Challenges
Q: How does VidePak ensure color consistency in multi-color printed bags?
A: The company’s 30+ printing machines use W&H’s AM2160 multi-purpose units with CMYK+2Pantone configurations, achieving <0.5 Delta-E color variance. Combined with PP’s inherent dye affinity, this ensures vibrant, fade-resistant branding.
Q: Can VidePak’s open-top bags withstand harsh environments?
A: Yes. By laminating woven fabric with BOPP films (using Hanhong 1760mm coaters), bags achieve IP67 waterproof ratings, ideal for moisture-prone settings like grain storage.
Sustainability and Market Expansion
VidePak’s recyclable PP woven bags align with global ESG trends, reducing carbon footprints by 40% compared to traditional alternatives. Their Starlinger SVI 4.0 machines further enhance sustainability by recycling 98% of production scrap[citation:42].
Market-wise, the company’s focus on customizable designs (e.g., UV-resistant coatings for Middle Eastern clients) has driven a 22% YOY growth in Southeast Asia and Africa.
Conclusion
The fusion of fine yarn technology and Austrian-German engineering positions VidePak as a leader in open-top PP woven bag innovation. By mastering extrusion temperature and draw ratio variables, the company delivers products that exceed ISO 9001 benchmarks while supporting circular economy goals. For industries seeking reliable, high-performance packaging, VidePak’s solutions represent both a technical and strategic advantage.
External Resources:
- Learn how Starlinger technology revolutionizes BOPP bag efficiency.
- Explore sustainable PP bag production with advanced recycling.
This report synthesizes operational data, peer-reviewed engineering principles, and market analytics to provide actionable insights for stakeholders in the packaging sector.