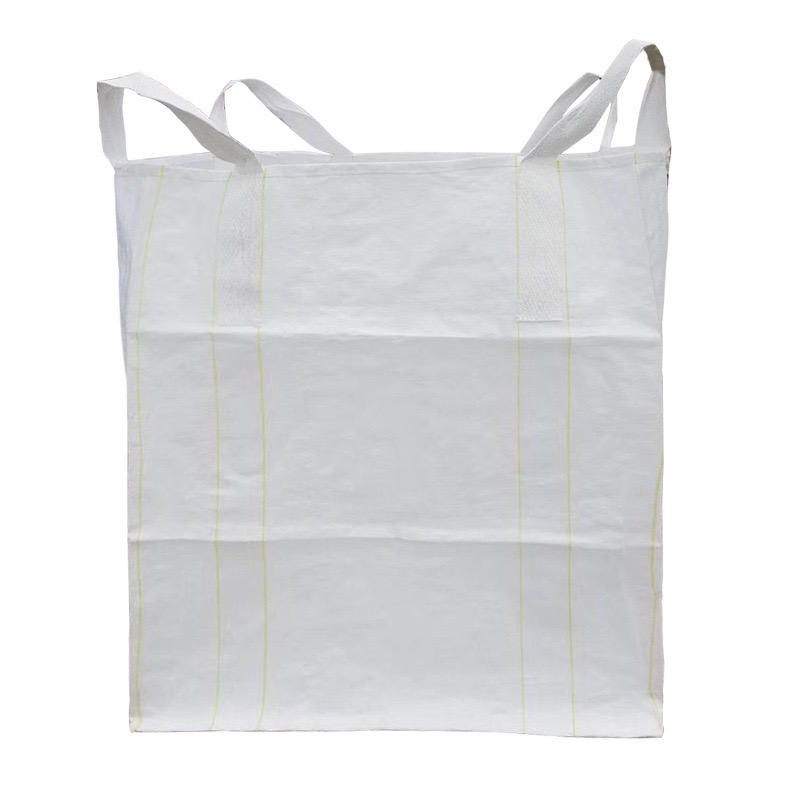
In the world of industrial packaging, FIBC Bags (Flexible Intermediate Bulk Containers), Bulk Bags, Ton Bags, and Jumbo Bags are essential for storing and transporting a wide variety of products, from chemicals and fertilizers to food ingredients and construction materials. These large-capacity bags offer a cost-effective and efficient solution for bulk handling, but their effectiveness largely depends on the manufacturing process, materials used, and design features.
At VidePak, we specialize in the production of high-quality FIBC Bags that are tailored to meet the unique needs of our clients. Our products feature innovative design options such as double loop and four loop configurations, with full customization options for different sizes, capacities, and loading requirements. One of the key elements of our FIBC Bags‘ strength and flexibility lies in the advanced production process, particularly the drawing process that enhances the durability and flexibility of the bags.
In this article, we will explore the significance of the FIBC Bags‘ design, how the drawing process influences the bag’s performance, and the technological advancements that contribute to the efficiency of our manufacturing processes.
Design Customization: Tailoring FIBC Bags to Meet Specific Needs
FIBC Bags are primarily designed for bulk packaging, and their design plays a crucial role in their performance. We offer both double loop and four loop designs, each tailored to different requirements.
- Double Loop Bags: These are ideal for lighter loads or products that do not require a significant amount of structural support. The double loop design is simple and cost-effective, making it a popular choice in industries like agriculture or food packaging.
- Four Loop Bags: Designed for more robust applications, four loop bags are better equipped to handle heavier and more complex products. This design enhances the bag’s load-bearing capacity, providing increased strength and stability. It is commonly used for industrial applications, such as in the transportation of chemicals, construction materials, and other heavy-duty goods.
Both types of bags can be customized in terms of size, shape, and printing to meet client specifications. Customization also extends to the type of closure, such as spout tops or plain tops, and the addition of inner liners to ensure product safety.
The Importance of the Drawing Process in Durability and Flexibility
The drawing process plays a vital role in the manufacture of FIBC Bags. Drawing refers to the technique used to stretch and align polypropylene (PP) fibers during the production of woven fabric. This process significantly impacts the final characteristics of the bag, including its strength, flexibility, and resistance to wear and tear.
When FIBC Bags are manufactured, high-quality PP fibers are drawn to create a strong, uniform fabric that is both durable and flexible. The drawing process increases the fiber’s tensile strength, enabling the fabric to withstand heavy loads and resist tearing or breaking. The stretching of the fibers also contributes to the bag’s flexibility, allowing it to bend and adapt to different storage conditions without compromising its structural integrity.
The level of drawing is carefully controlled to balance strength and flexibility. Too little drawing can result in a fabric that is too weak and prone to failure, while excessive drawing can reduce the bag’s flexibility, making it less suitable for certain applications.
Automation and Technology: The Role of Starlinger and W&H Equipment
To ensure the highest standards of quality and efficiency in our FIBC Bags production, VidePak relies on cutting-edge machinery from renowned suppliers like Starlinger (Austria) and W&H (Germany). These high-tech systems are designed for high-speed, automated manufacturing, ensuring precision and consistency in every batch.
- Starlinger Equipment: Known for its expertise in producing high-performance woven fabrics, Starlinger’s machinery enables us to create woven polypropylene fabrics with a high degree of uniformity. This is crucial for ensuring the strength and durability of our FIBC Bags.
- W&H Equipment: The W&H machinery specializes in the extrusion and lamination of polypropylene films, which are key components in the production of FIBC Bags. These systems ensure that the laminated fabrics are well-bonded and resistant to environmental factors such as moisture or UV exposure.
Both Starlinger and W&H provide high levels of automation, which significantly reduces human error and improves production speed. The line speed of over 200 pieces per minute, along with multi-machine interconnection, allows us to produce large volumes of FIBC Bags efficiently, maintaining high standards while minimizing costs.
Key Features of Our FIBC Bags
At VidePak, our FIBC Bags are built to withstand the harshest conditions. The following table summarizes the key features of our FIBC Bags, Bulk Bags, Ton Bags, and Jumbo Bags:
Feature | Description |
---|---|
Design | Customizable double loop or four loop designs for varied applications. |
Material | High-quality, durable polypropylene (PP) fabric. |
Customization | Available in various sizes, colors, and printing options. Inner liners and specialized closures can be added. |
Load Capacity | Supports a range of load capacities, from light-duty products to heavy industrial materials. |
Drawing Process | Optimized to enhance strength and flexibility through controlled stretching of polypropylene fibers. |
Equipment | Produced using advanced Starlinger and W&H machinery for maximum precision and efficiency. |
Applications | Suitable for agriculture, chemicals, food, construction, and more. |
FAQs: Addressing Common Questions about FIBC Bags
Here are some frequently asked questions about FIBC Bags, Bulk Bags, Ton Bags, and Jumbo Bags:
Q1: What is the difference between a double loop and a four loop FIBC bag?
A1: The primary difference lies in the number of lifting loops. A double loop FIBC bag is ideal for lighter loads and basic applications, while a four loop bag provides additional support and is designed for heavier and more complex materials.
Q2: Are your FIBC Bags customizable in size?
A2: Yes, we offer full customization of FIBC Bags in terms of size, capacity, and design. This ensures that the bags are perfectly suited to your specific application.
Q3: How does the drawing process affect the performance of FIBC Bags?
A3: The drawing process increases the tensile strength and flexibility of the polypropylene fibers, ensuring that the bags are both strong and adaptable to varying load conditions.
Q4: What industries use FIBC Bags?
A4: FIBC Bags are used in a variety of industries, including agriculture, construction, chemicals, food processing, and logistics. They are ideal for storing and transporting bulk materials safely and efficiently.
Q5: How do you ensure the quality of your FIBC Bags?
A5: We use state-of-the-art equipment from Starlinger and W&H to produce high-quality woven fabric. Our automated systems ensure consistent quality and efficiency across all production lines.
Q6: Can FIBC Bags be recycled?
A6: Yes, FIBC Bags are made from polypropylene, a recyclable material. We encourage responsible recycling practices to reduce environmental impact.
Conclusion
At VidePak, we understand that the performance of FIBC Bags, Bulk Bags, Ton Bags, and Jumbo Bags depends not only on their design and material but also on the manufacturing process that goes into producing them. Our use of high-end technology from Starlinger and W&H, combined with expert craftsmanship, ensures that our FIBC Bags offer unmatched strength, durability, and flexibility. Whether you need customized bags for light or heavy-duty applications, we have the expertise and equipment to meet your needs efficiently and cost-effectively.
For more information on FIBC Bags and their role in bulk packaging solutions, check out the detailed exploration of FIBC Bags and the Benefits of Fine Yarn Technology and FIBC Bags and the Versatility of Bulk Packaging.