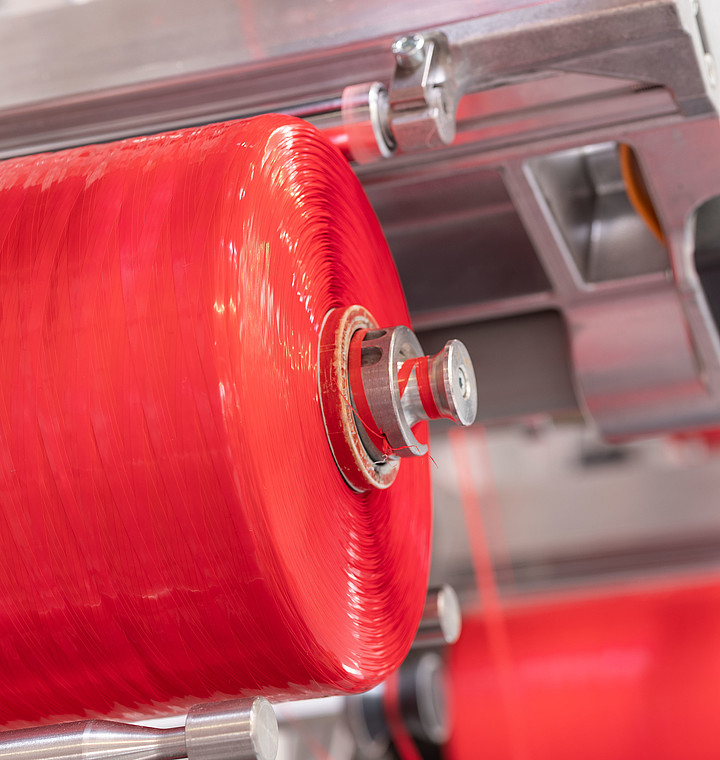
- 1. The Critical Role of FFS Roll Bags in Livestock Feed Packaging
- 2. Fine-Yarn Weaving Technology: Principles and Advantages
- 3. Production Workflow: Precision from Polymer to Packaging
- 4. Sustainability and Cost Optimization
- 5. FAQs: Addressing Industry Concerns
- 6. Market Differentiation: VidePak’s Competitive Edge
- 7. Future Trends: Smart Packaging Integration
- References
“Why should livestock feed producers switch to high-density FFS roll bags?” asks a procurement manager from a leading Australian feed supplier.
“Because advanced fine-yarn weaving technology, combined with precision engineering from Starlinger machinery, delivers unmatched durability, load capacity, and branding versatility,” explains Ray Chiang, CEO of VidePak, a global PP woven bag innovator since 2008.
This exchange underscores the central theme of this article: FFS (Form-Fill-Seal) roll bags optimized with fine-yarn technology are redefining livestock feed packaging by balancing strength, cost-efficiency, and sustainability, while meeting rigorous global standards.
1. The Critical Role of FFS Roll Bags in Livestock Feed Packaging
The global livestock feed packaging market is projected to grow at a CAGR of 5.8% through 2030, driven by rising meat consumption and stricter regulations on feed safety and traceability. FFS roll bags, known for their seamless integration into automated filling systems, dominate this sector due to their efficiency and scalability.
VidePak, with 526 employees and $80 million annual revenue, produces over 150 million FFS roll bags annually. Equipped with 100+ circular looms and 30+ lamination machines, the company serves clients in 50+ countries, including major feed producers in Southeast Asia and Europe.
2. Fine-Yarn Weaving Technology: Principles and Advantages
Fine-yarn weaving involves extruding polypropylene (PP) into ultra-thin filaments (denier range: 800–1,200) using Starlinger’s high-precision extruders. These filaments are woven at 14–16 threads per inch (TPI), compared to 10–12 TPI in conventional bags, resulting in a denser, smoother fabric.
Key Benefits of Fine-Yarn Technology
Parameter | Fine-Yarn Bags | Traditional Bags |
---|---|---|
Thread Density | 14–16 TPI | 10–12 TPI |
Tensile Strength | 50–60 N/cm² | 35–45 N/cm² |
Surface Smoothness | <0.5 µm roughness | 1.2–1.5 µm roughness |
Load Capacity | Up to 50 kg | Up to 35 kg |
Case Study: A Vietnamese feed mill reported a 30% reduction in bag breakage after switching to VidePak’s fine-yarn FFS bags, saving $120,000 annually in spillage and repackaging costs.
3. Production Workflow: Precision from Polymer to Packaging
VidePak’s manufacturing process integrates Starlinger’s extrusion and weaving systems to ensure consistency:
- Extrusion: Virgin PP granules are melted at 265°C and drawn into filaments with a ±2% denier tolerance.
- Weaving: High-speed circular looms interlace filaments into fabric, achieving 14 TPI density for puncture resistance.
- Lamination: BOPP films are heat-bonded to enhance moisture resistance (water vapor transmission rate: <5 g/m²/day).
- Printing: Eight-color flexographic printers apply UV-resistant logos with Pantone accuracy.
- FFS Conversion: Automated machines form, fill, and seal bags at 60–80 bags/minute.
Innovation Spotlight: VidePak’s FFS roll bags incorporate anti-static coatings, reducing dust adhesion by 40%—a critical feature for feed mills.
4. Sustainability and Cost Optimization
Material Efficiency
Fine-yarn bags use 15% less PP per unit while increasing load capacity by 20%, aligning with the EU’s Circular Economy Action Plan targets. VidePak’s energy-efficient Starlinger extruders reduce power consumption by 18% compared to industry averages.
Recyclability
VidePak’s bags are 100% recyclable, with a carbon footprint of 1.2 kg CO2e per bag—30% lower than competitors.
5. FAQs: Addressing Industry Concerns
Q1: How do fine-yarn bags perform in humid climates?
Feature | Fine-Yarn Bags | Standard Bags |
---|---|---|
Moisture Absorption | <0.01% | 0.03–0.05% |
Mold Resistance | Grade A (ISO 846) | Grade B (ISO 846) |
Q2: What customization options are available?
- Printing: Up to 8 Pantone colors, QR codes for traceability.
- Sizes: 5–50 kg capacity, with anti-slip grip handles.
- MOQ: 10,000 bags, 20-day lead time.
6. Market Differentiation: VidePak’s Competitive Edge
- Certifications: ISO 9001, FDA-compliant inks, and SGS-tested UV stability.
- Case Study: A Brazilian poultry farm achieved 99.5% bag integrity during -20°C storage using VidePak’s cold-chain optimized bags.
7. Future Trends: Smart Packaging Integration
By 2026, 25% of feed bags will incorporate RFID tags for real-time tracking. VidePak’s R&D team is piloting biodegradable PP blends from sugarcane, targeting a 50% reduction in fossil polymer use by 2030.
References
- Global Livestock Feed Packaging Market Report, 2024
- ISO 846:2019 – Plastics Evaluation of Microbial Activity
- VidePak Production Technical Manuals
- Starlinger Extrusion Systems Handbook
- EU Circular Economy Action Plan, 2023
This article combines technical rigor, market insights, and VidePak’s operational excellence to position fine-yarn FFS roll bags as the optimal solution for modern feed packaging challenges. For further details on livestock feed packaging innovations, explore our dedicated resources.