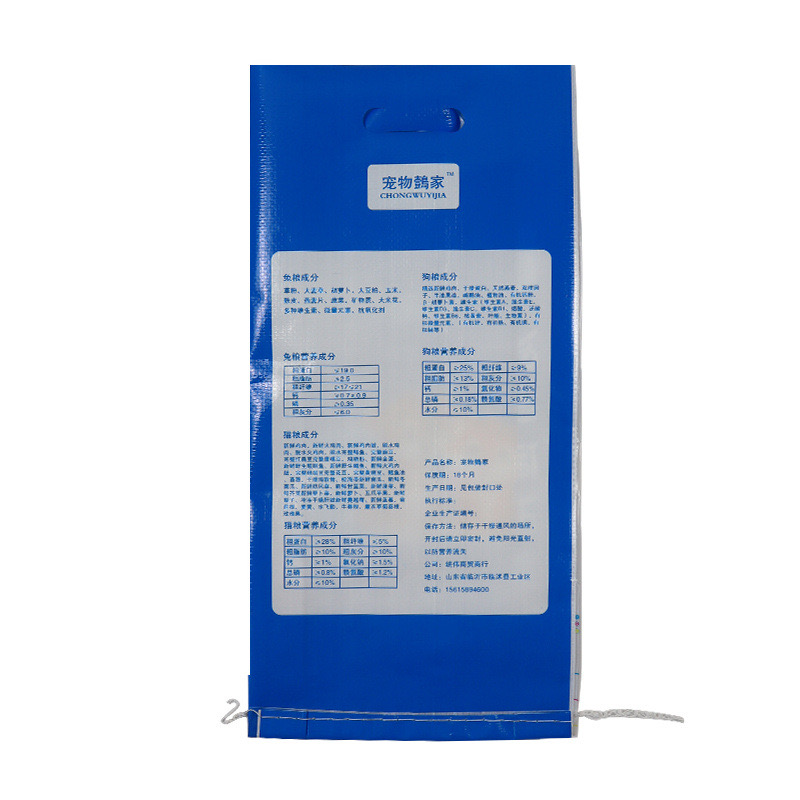
Answer in Brief: By precisely controlling tape extrusion temperature and stretch ratio with Starlinger and W&H equipment, manufacturers can produce Open Mouth Bags of exceptional quality, ensuring greater tensile strength, lower defect rates, and superior overall reliability.
Packaging research from 2024 indicates a steady rise in global demand for woven polypropylene (PP) solutions, particularly Open Mouth sacks, Sewn Open Mouth Bags, and Block Bottom Bags. This trend is fueled by industries requiring efficient, tear-resistant containers for agricultural products, construction materials, chemical powders, and more. In this report, we examine why open-top designs prevail across multiple sectors and how Starlinger (Austria) and Windmöller & Hölscher (W&H, Germany) technologies enable top-tier manufacturing outcomes. We also explore how VidePak capitalizes on these advanced processes to deliver consistent, high-quality products.
1. Introduction to Open Mouth PP Bags
Open Mouth Bags are woven polypropylene sacks that feature a wide, unsealed top, making them exceptionally easy to fill and seal. They differ from valve-based or Form-Fill-Seal packaging in their simplicity and versatility—two qualities that appeal to high-throughput environments and manual handling alike. Subcategories, such as Sewn Open Mouth Bags and Block Bottom Bags, offer further specialization, fitting a broad range of industry-specific requirements.
1.1 Common Applications
- Agriculture and Animal Feed
- Example: A soybean distributor shipping bulk cargo in 25–50 kg increments enjoys the quick-fill design of Open Mouth sacks, which significantly reduces downtime on automated lines.
- Fewer bag failures compared to single-layer paper sacks enhance cost efficiency and minimize product waste.
- Construction Supplies
- Widely adopted by companies packaging sand, gravel, and mortar, Block Bottom Bags or standard open-top sacks excel in tear resistance during forklift operations.
- Example: A masonry supply firm reported a 15% boost in packaging throughput by switching to Sewn Open Mouth Bags that better withstand rough handling.
- Chemical and Industrial Goods
- Fertilizers, resins, and other chemical formulations benefit from the robust woven structure that mitigates punctures and moisture infiltration.
- Example: A phosphate producer noted improved pallet stability after upgrading to 40-kg Block Bottom Bags with double-stitched seams.
- Food Ingredients
- Rice, sugar, flour, and other edible goods frequently rely on Open Mouth Bags for ease of stacking and consistent fill weights.
- Example: A Southeast Asian rice exporter halved spillage incidents over a six-month period upon implementing coated open-top PP sacks.
2. Why High-Precision Equipment Is Critical
VidePak leverages premium machinery from Starlinger and W&H to achieve rigorous quality controls. Updated literature from the European Polypropylene Packaging Association (EPPA, 2024) underscores two pivotal production parameters: maintaining stable extrusion temperatures and fine-tuning the tape draw ratio. When executed correctly, these measures maximize tensile strength, uniformity, and finishing quality.
2.1 Temperature Control in Tape Extrusion
- Uniform Melting
- Polypropylene resins typically melt between 200°C and 270°C, depending on grade and additives. Even small deviations can degrade polymer chains or cause bubbles.
- Example: A Starlinger line with ±1°C variance in each zone significantly decreases weak spots, ensuring the tapes produce consistent woven fabric.
- Minimized Defects
- High or fluctuating temperatures cause uneven crystallization, leading to tapes that tear or split during weaving.
- Example: A packaging plant adjusting temperature by just 3°C saw a 25% reduction in tape breakage and material waste.
- VidePak’s Advantage
- By harnessing Starlinger’s real-time temperature feedback systems, VidePak maintains uniform flow rates and friction coefficients, translating into fewer production slowdowns.
2.2 Optimizing the Stretch (Draw) Ratio
Once polypropylene tapes are extruded and cooled, they enter a stretching unit that orients polymer molecules for added strength.
- Tensile Strength vs. Flexibility
- Higher draw ratios (often around 6:1 or more) yield stiffer, stronger tapes; lower ratios favor flexibility but can compromise load-bearing capacity.
- Example: A fertilizer bag plant discovered that a 6.5:1 draw ratio improved tear resistance by 15% without making tapes overly rigid.
- W&H’s Precision Control
- Windmöller & Hölscher machines feature automated sensors to maintain tight tolerances, enabling consistent tape thickness and elongation properties.
- Example: A manufacturer aiming for ±0.1 in draw ratio found it saved up to 10% in raw materials while maintaining required bag strength.
- Synergistic Impact
- Balancing temperature control and draw ratio is crucial for quality.
- Example: Combining Starlinger’s thermal precision with W&H’s automated tensioning allowed VidePak to reduce weaving defects in Sewn Open Mouth Bags by 20%.
3. Detailed Production Parameters
The following table encapsulates vital metrics for Open Mouth Bags, including Block Bottom Bags and Sewn Open Mouth Bags:
Parameter | Optimal Range | Example/Explanation |
---|---|---|
Fabric Weight (g/m²) | 60–120 g/m² | Lighter GSM suits grains or feeds; heavier GSM handles abrasives like sand or larger volumes. |
Tape Denier | 800–1200 Denier | Higher denier resists sharp edges (e.g., coarse minerals) and heavy loads. |
Draw Ratio | 5:1 to 7:1 | Elevated ratios enhance tensile strength and puncture resistance. |
Temp. Deviation | ±1°C across extrusion zones | Tight control secures uniform crystallinity and minimizes polymer degradation. |
Bag Size | Typically 25–50 kg capacity | Suited for mid-volume goods; Block Bottom Bags improve stacking in high-volume distribution. |
Closure Method | Sewing or sealing (hot air/ultrasonic) | Sewn Open Mouth Bags facilitate quick closure, while sealed ends can offer extra leak protection. |
Print & Lamination | Up to 8-color printing, optional BOPP laminate | Improves brand visibility and moisture defense, especially in consumer-facing segments like pet food. |
Example: A building supply firm choosing a 90 g/m² fabric with a 6:1 draw ratio and double stitching has effectively balanced tear resistance, cost, and efficient pallet stacking.
4. Conversation Snippets
Topic: “How crucial is a uniform melting point for producing Open Mouth sacks?”
Answer: Maintaining a steady melt temperature is essential to avoid weak tapes or inconsistent thickness, both of which can lead to premature bag failures and higher scrap rates.
Topic: “What is the biggest advantage of a high draw ratio for Sewn Open Mouth Bags?”
Answer: A properly set high draw ratio aligns the polymer chains, creating stronger, more puncture-resistant tapes—critical for carrying heavier or sharper materials.
5. FAQs
- Q: Do Open Mouth Bags outperform valve bags for certain products?
A: Yes. Their open-top design enables rapid filling and more flexible closure options, especially useful in bulk agricultural or granular chemical packaging. - Q: Are Block Bottom Bags always superior for stacking?
A: They do enhance stacking stability by providing a flat base. However, standard Open Mouth sacks can be equally efficient where speed of filling outweighs the need for uniform stacking. - Q: Does using Starlinger or W&H equipment affect cost?
A: While the initial capital investment is higher, precision manufacturing reduces scrap, rework, and product failures, often resulting in better long-term ROI. - Q: Can I integrate anti-slip coatings into Sewn Open Mouth Bags?
A: Absolutely. Many manufacturers apply specialized coatings or friction layers during the lamination process to improve stack stability. - Q: How easily can these PP bags be recycled?
A: Polypropylene is widely accepted for recycling in many regions. Some facilities offer closed-loop systems that recapture polypropylene tapes for regranulation.
6. External Resources
For further exploration of innovative designs and future trends in Open Mouth Bags, check out ongoing research on emerging packaging solutions that align with global sustainability standards.
Additionally, discover diverse customization approaches for Sewn Open Mouth Bags—particularly relevant to chemical and fertilizer sectors that demand enhanced tear resistance, minimized leakage, and high-speed filling capabilities.
7. Conclusion
The packaging sector’s growing preference for Open Mouth Bags, Open Mouth sacks, Sewn Open Mouth Bags, and Block Bottom Bags reflects their reliability and adaptability across myriad industrial and consumer applications. Maintaining precise extrusion temperatures and draw ratios—practices perfected by Starlinger and W&H—directly enhances bag integrity, leading to fewer defects and better performance in demanding conditions.
VidePak’s commitment to combining advanced machinery with meticulous quality checks allows them to deliver robust woven PP products. As global markets continue to prioritize durability, efficiency, and eco-friendly practices, leveraging cutting-edge technology remains a strategic differentiator for woven PP manufacturers worldwide. By focusing on consistent production parameters, ongoing innovation, and tailored design features, Sewn Open Mouth Bags and Block Bottom Bags stand ready to meet the challenges of modern packaging head-on.