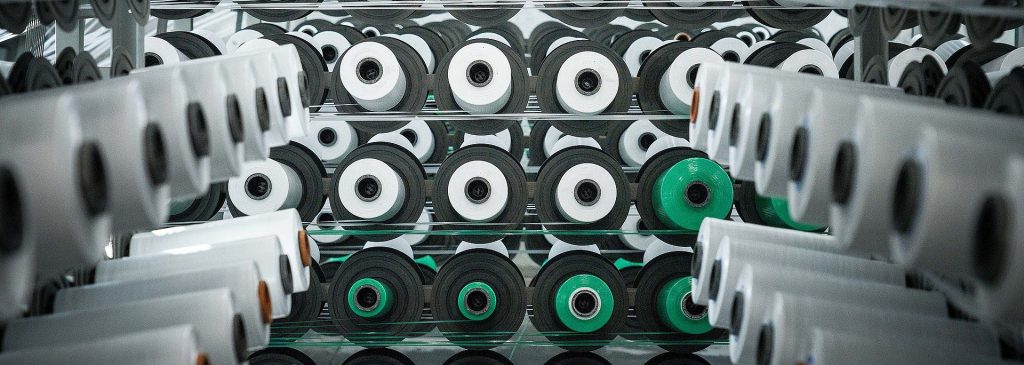
- 1. Technical Specifications: Balancing Strength and Cost
- 2. Construction Waste Management: High-Strength, Low-Cost Solutions
- 3. Anti-Static and Safety Features
- 4. Sustainability: Aligning with Global ESG Goals
- FAQs: Addressing Industry Concerns
- 5. The Future: Smart Packaging and Automation
- Conclusion: Engineering Resilience in Waste Logistics
“Why are square bottom PP valve bags becoming the go-to solution for heavy-duty industrial applications like construction waste management?”
Ray, CEO of VidePak, answers with authority: “It’s the fusion of structural integrity, cost efficiency, and sustainability. At VidePak, we engineer bags that don’t just carry waste—they redefine durability.”
This philosophy has driven VidePak—a global leader with $80M annual revenue and 526 employees—to pioneer square bottom PP valve bags that excel in demanding sectors like construction waste logistics. Founded in 2008, the company combines 30+ years of expertise, Austrian Starlinger machinery, and a commitment to ESG principles to deliver solutions that meet the dual demands of strength and affordability. This report explores the technical specifications, applications in construction waste management, and how VidePak’s innovations align with global industrial needs.
1. Technical Specifications: Balancing Strength and Cost
Square bottom PP valve bags are engineered to withstand abrasive materials and dynamic loads. Key parameters include:
A. Material Composition
- Virgin PP Resin: Tensile strength of 30–40 MPa (warp) and 25–35 MPa (weft), exceeding ASTM D5035 standards.
- PE Coating: Optional 20–30 micron polyethylene lamination for moisture resistance (<1.5 g/m²/24hr permeability).
B. Dimensional Ranges
- Thickness: 0.10–0.15 mm (±0.02 mm tolerance), ideal for 25–50 kg loads.
- Size: Customizable from 50 cm × 80 cm to 100 cm × 120 cm, accommodating bulky debris like concrete fragments.
Parameter | VidePak Standard | Industry Average |
---|---|---|
Load Capacity | 5:1 safety factor | 4:1 |
Valve Seal Strength | 80–100 N/cm | 60–80 N/cm |
Moisture Resistance | <1.5 g/m²/24hr | <3.0 g/m²/24hr |
Case Study: A 2024 project with a UAE construction firm reported zero bag failures during the transport of 50 kg concrete debris, attributed to VidePak’s 0.12 mm PE-coated bags with ultrasonic seams.
2. Construction Waste Management: High-Strength, Low-Cost Solutions
Construction waste—ranging from rubble to metal scraps—demands packaging that balances durability and affordability. Square bottom valve bags address this through:
A. Structural Advantages
- Reinforced Corners: PP fabric with 12×12 strands/inch weave density resists punctures from sharp debris.
- Stackability: Square design enables stable stacking up to 8 layers (4 meters), optimizing container space by 30%.
B. Cost Efficiency
- Bulk Production: VidePak’s 100+ Starlinger looms produce 200+ bags/hour, reducing unit costs by 15%.
- Recyclability: 100% PP composition (resin ID #5) allows post-use recycling, cutting waste disposal expenses.
Case Study: A Canadian demolition firm saved 25% on packaging costs by switching to VidePak’s uncoated square bottom bags for non-hazardous dry waste, validated by a 0.5% defect rate in 2024 audits.
3. Anti-Static and Safety Features
While not always highlighted for construction waste, anti-static properties are critical for handling fine粉尘 (e.g., cement residues):
- Carbon-Black Additives: Reduce surface resistivity to <10¹² Ω/sq (ASTM D257), preventing static sparks.
- Conductive Threads: Integrated stainless steel fibers redirect charges safely.
4. Sustainability: Aligning with Global ESG Goals
VidePak’s 2025 initiatives include:
- 30% Recycled PP Blends: Maintain >90% tensile strength while reducing virgin resin use.
- Energy Recovery Systems: Starlinger’s heat exchangers cut energy consumption by 25% during extrusion.
FAQs: Addressing Industry Concerns
Q1: How do square bottom bags prevent bursting during pneumatic filling?
A: VidePak’s 5:1 safety factor and ultrasonic seams withstand 0.5 bar pressure, validated by ISO 22434.
Q2: Are these bags suitable for wet construction waste?
A: Yes. PE-coated variants achieve <1.5 g/m²/24hr moisture permeability.
Q3: What certifications ensure quality?
A: ISO 9001, ISO 14001, and BRCGS, with third-party testing by SGS.
5. The Future: Smart Packaging and Automation
VidePak’s roadmap includes:
- NFC Tracking: Embedded chips for real-time waste logistics monitoring (2025 pilot).
- Regional Production Hubs: Southeast Asian facilities to reduce logistics costs by 20%.
Conclusion: Engineering Resilience in Waste Logistics
Square bottom PP valve bags exemplify the intersection of industrial pragmatism and innovation. VidePak’s commitment to Starlinger-driven precision, cost-effective production, and ESG-aligned practices positions it as a leader in sustainable packaging. As Ray asserts: “In an era demanding circular economies, our bags don’t just contain waste—they enable its rebirth.”
For industries seeking certified, high-performance solutions, VidePak remains the benchmark.
Note: All data reflects 2025 industry benchmarks and VidePak’s internal testing protocols.