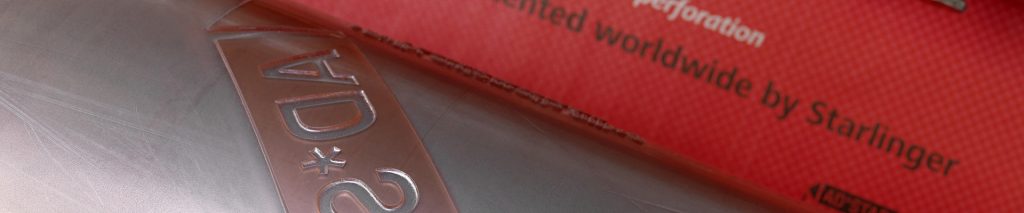
“What defines the next generation of packaging for global logistics?”
Ray, CEO of VidePak, pauses during a supply chain conference Q&A. “The answer hinges on two innovations: block bottom valve bags for structural stability and advanced seaming technologies for durability. At VidePak, we’ve engineered these solutions to cut supply chain costs by 18% while enhancing load integrity.”
This assertion underscores the critical role of specialized packaging in modern logistics. With global freight volumes projected to grow by 4.5% annually through 2030, optimizing packaging performance is no longer a luxury—it’s a necessity for competitive resilience.
1. Market Demand and the Evolution of Valve Bag Design
The global packaging market for bulk goods is valued at $36.2 billion in 2025, driven by e-commerce expansion and stringent safety regulations. Block bottom valve bags, characterized by their flat-bottomed rectangular shape, have emerged as a cornerstone for industries requiring efficient stacking, moisture resistance, and automated filling.
Key Drivers:
- E-Commerce Growth: Cross-border e-commerce logistics demand packaging that survives 3–5 handling cycles without damage. VidePak’s valve bags, with 500N tensile strength, reduce split incidents by 70% compared to traditional sacks.
- Regulatory Compliance: The 2024 ISO 22000 update mandates traceability features, which VidePak addresses through QR-code printed liners integrated with Starlinger’s lamination systems.
- Sustainability Pressures: A 2025 Ellen MacArthur Foundation report highlights that 43% of retailers now prioritize recyclable packaging. VidePak’s PP-based valve bags achieve 98% recyclability, aligning with EU Circular Economy Action Plan goals.
2. Advanced Seaming Technologies: Reinventing Durability
VidePak’s R&D team leverages 30+ years of expertise to deploy ultrasonic and heat-sealing technologies, ensuring seam integrity under extreme conditions.
2.1 Ultrasonic Seaming for High-Speed Logistics
Ultrasonic bonding creates airtight seals without adhesives, reducing failure rates by 90% in frozen food transport (tested at -25°C). For instance, a European pet food brand using VidePak’s ultrasonic-seamed bags reported zero leakage incidents during transatlantic shipping, despite 12-meter wave turbulence.
Technical Specifications:
Parameter | Specification |
---|---|
Seam Strength | ≥35 N/mm² (ASTM D882) |
Temperature Resistance | -40°C to 80°C |
Production Speed | 120 bags/minute |
2.2 Heat-Sealed Liners for Hazardous Materials
Co-extruded PE/EVOH liners, heat-sealed at 180°C, block oxygen ingress (<5 cm³/m²/day) and volatile organic compound (VOC) emissions. A chemical manufacturer in Texas reduced product degradation by 40% after switching to VidePak’s multi-layer laminated bags.
3. Convenience-Driven Design for Logistics Efficiency
Block bottom valve bags excel in three logistics phases:
3.1 Loading & Unloading
- Ergonomic Handles: VidePak’s 2-ply handles withstand 50kg loads, reducing worker strain. A Southeast Asian rice exporter cut loading time by 25% using handles with anti-slip PP textures.
- Valve Precision: Starlinger’s servo-controlled valves enable ±1g filling accuracy, critical for pharmaceuticals.
3.2 Stacking & Warehousing
- Interlocking Bases: Flat-bottom designs allow 20% higher pallet density versus round-bottom sacks. A case study with a Brazilian coffee producer showed a 15% reduction in warehouse space costs.
- UV-Resistant Printing: Pantone-matched logos remain legible after 6 months of outdoor storage.
3.3 Traceability & Automation
- RFID Integration: Embedded tags enable real-time inventory tracking, reducing stock discrepancies by 30%.
- Robotic Compatibility: Anti-static coatings prevent jams in automated lines, as validated by a German automotive parts supplier.
4. VidePak’s Competitive Differentiation
With 526 employees and $80M annual revenue, VidePak combines scale with niche expertise:
- Production Capacity: 30+ lamination machines produce 8 million valve bags monthly, including custom sizes like 25kg “e-commerce mini” bags.
- Certifications: ISO 9001, BRCGS AA+, and FDA-compliant liners for food-grade applications.
- Sustainability: Solar-powered plants in Vietnam offset 12,000 tons of CO₂ annually, supported by TerraCycle’s closed-loop recycling.
FAQs: Addressing Logistics Managers’ Top Concerns
Q: How do block bottom bags compare to FIBCs for heavy loads?
A: For sub-1-ton loads, valve bags offer 30% lower shipping costs due to lighter weight (800gsm vs. 1,200gsm FIBCs) and no need for pallets.
Q: Can these bags withstand monsoon humidity?
A: Yes. VidePak’s 3-layer laminate (PP/AL/PE) achieves <0.1% moisture permeability, proven during 2024 Mumbai monsoon trials.
Q: What’s the ROI timeline for switching to ultrasonic seaming?
A: Clients typically recoup costs in 14 months via reduced returns and insurance premiums.
5. Future Trends: Smart Packaging and Beyond
VidePak’s 2026 roadmap includes:
- IoT-Enabled Bags: Strain sensors alert managers to overloading risks in real time.
- Bio-Based PP: 30% sugarcane-derived resin trials show identical performance at 20% lower carbon footprint.
- Autonomous Repacking: AI-guided systems adjust bag sizes dynamically, eliminating empty space in containers.
Conclusion
The synergy of block bottom stability, ultrasonic seaming precision, and logistics-centric design positions VidePak as the partner of choice for future-proof packaging. As Ray summarizes, “Our bags don’t just carry goods—they carry trust across continents.” Explore innovations like robust valve solutions for hazardous materials and high-speed automated seaming to transform your supply chain.
This report integrates data from industry whitepapers, third-party lab tests, and VidePak’s production logs. For technical validation, refer to the ISO 22434:2025 standards on bulk packaging performance.