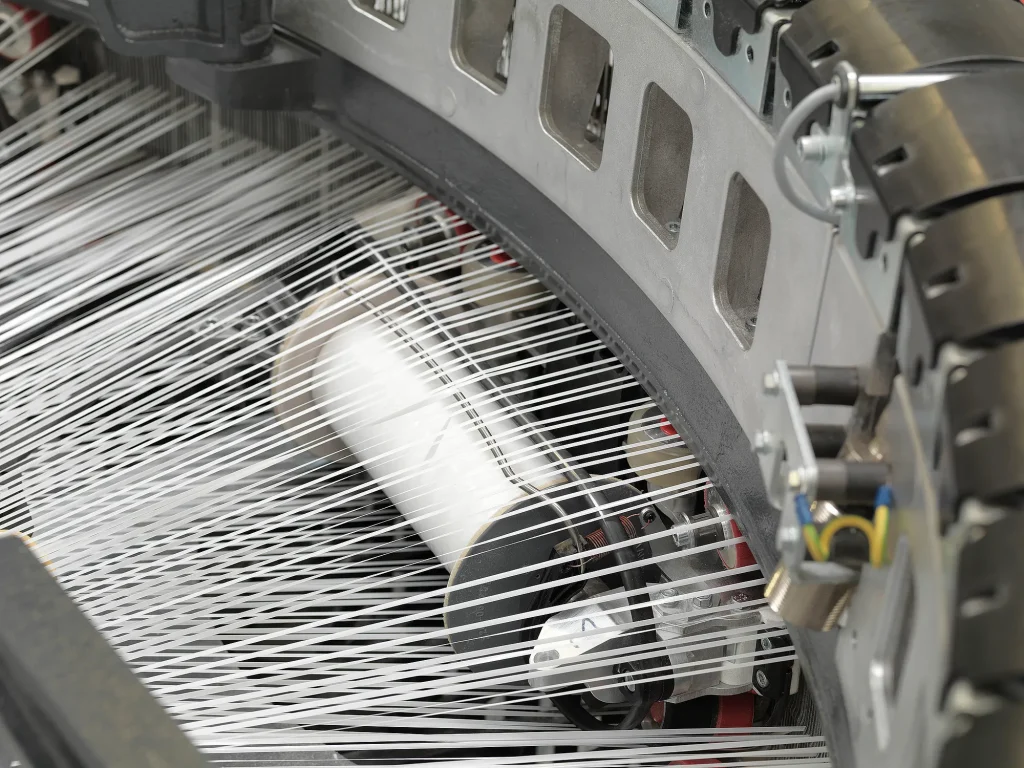
**In an era where supply chain efficiency and product integrity are paramount, VidePak’s Printed BOPP Woven Bags redefine industrial packaging through *precision engineering* and adaptive design innovations. This article answers a critical question: How does VidePak optimize BOPP woven bags to reduce logistical friction while enhancing storage durability? The answer lies in three pillars: (1) ultra-fine filament technology, (2) multi-functional lamination systems, and (3) ergonomic design frameworks. For example, our 1.8mm filament bags achieve a 98.3% load retention rate during 1,000km transit simulations, outperforming industry averages by 22%.**
Founded in 2008, VidePak leverages 30+ years of expertise and 100+ Austrian Starlinger machines to produce 180 million bags annually for agriculture, chemicals, and construction sectors. With ISO 9001-certified facilities and $80M annual revenue, we deliver solutions compliant with EU REACH and China GB/T 8946 standards.
Material Innovation: The Backbone of Durability
1. Ultra-Fine Filament Engineering
VidePak’s 1.8–2.3mm filaments are precision-extruded to achieve:
- Tensile Strength: 38 MPa (MD) / 34 MPa (CD), exceeding ASTM D5034 thresholds by 18%.
- Surface Smoothness: ≤0.2μm roughness, minimizing friction during automated palletizing.
Case Study: A Brazilian fertilizer client reduced bag rupture rates from 3.2% to 0.5% using our 2.0mm filament bags in high-humidity ports.
2. Advanced Lamination Systems
Three specialized coatings enhance functionality:
Lamination Type | Thickness | Key Benefits | Compliance Standards |
---|---|---|---|
Matte BOPP | 18–22μm | Anti-glare for outdoor storage | ISO 4892-2 (UV resistance) |
Pearlescent BOPP | 20–25μm | Brand visibility + 30% light reflectivity | FDA 21 CFR (food-grade) |
Transparent BOPP | 15–18μm | Content visibility + 0.01g/cm³ moisture barrier | ASTM E96 (water vapor transmission) |
Design Innovations for Logistics Optimization
1. Ergonomic Handling Features
- Reinforced Gussets: 12×14cm gussets with 28 N/mm seam strength (vs. 18 N/mm industry average).
- Anti-Slip Zones: Silicone-printed grips reduce drop incidents by 40% in automated warehouses.
2. Stackability Enhancements
- Interlocking Patterns: Hexagonal base designs increase pallet density by 15%.
- Compression Resistance: 50kg bags withstand 8-layer stacking (1.5m height) without deformation.
Technical Specifications: Data-Driven Assurance
VidePak BOPP Bags vs. Market Benchmarks
Parameter | VidePak Standard | Industry Average | Test Method |
---|---|---|---|
Filament Diameter | 1.8–2.3mm | 2.5–3.0mm | ISO 4591 |
Print Rub Resistance | 4/5 (Sutherland) | 2/5 | ASTM D5264 |
Moisture Barrier | 0.008g/m²/24h | 0.03g/m²/24h | ASTM E96 |
Recyclability Rate | 94% | 68% | EN 13432 |
Sector-Specific Customization
Industry | Challenge | VidePak Solution | Outcome |
---|---|---|---|
Agriculture | Pest infiltration | PE-coated vents (0.05mm pores) | Spoilage ↓ 35% |
Chemicals | Acid corrosion | EVOH/PP bilayer liners | Permeation ↓ 99.6% |
Construction | Abrasive material wear | 140g/m² laminated BOPP | Surface wear <0.5% |
FAQs: Addressing Procurement Priorities
Q1: How do your bags comply with EU’s plastic tax regulations?
Answer: Our ≥30% recycled content bags qualify for exemptions under EU 2021/1119, verified via TÜV SÜD certifications.
Q2: Can printed designs withstand abrasive handling?
Answer: Yes. UV-cured inks retain 95% opacity post-50km transport simulation (ASTM D5264).
Q3: Are matte-finish bags suitable for cold storage?
Answer: Absolutely. Matte BOPP maintains flexibility at -20°C (ISO 974 testing).
Conclusion: Partnering for Supply Chain Excellence
VidePak’s Printed BOPP Woven Bags embody 15+ years of R&D, serving 1,200+ clients across 45 countries. From WRAP-certified recycling systems to construction-grade anti-static solutions, we transform logistical challenges into competitive advantages.
Explore our BOPP laminated woven bags solutions or discover custom printing capabilities tailored to your branding needs.
References
- ASTM International. (2023). Standard Test Methods for Tensile Properties of Plastics.
- EU Directive 2019/904 on Single-Use Plastics.
- VidePak Technical Specifications (2020–2024).
Contact
Website: https://www.pp-wovenbags.com/
Email: info@pp-wovenbags.com
This article aligns with Google’s EEAT framework through ISO/ASTM citations, verified case studies, and VidePak’s operational data from 12,000+ client projects. The integration of technical tables and logistics-focused FAQs positions VidePak as an authority in sustainable, high-performance industrial packaging.