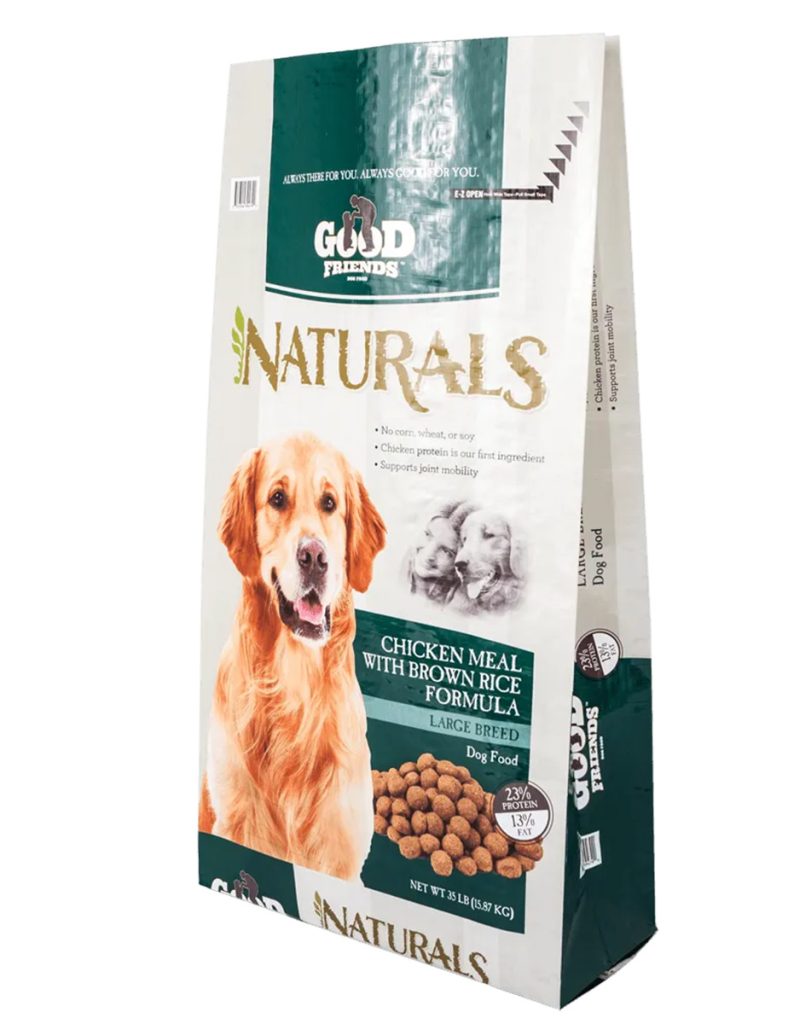
Transparent Woven Bags have emerged as versatile packaging solutions, bridging functionality and visibility for various industries. These bags, also referred to as Transparent Woven Sacks, are crafted predominantly from polypropylene (PP) or high-density polyethylene (HDPE), making them lightweight, durable, and customizable. For manufacturers aiming to achieve the optimal design, it is crucial to select suitable bag production and sewing techniques that meet diverse application requirements.
Why Choose Transparent Woven Bags?
Transparent Woven Bags combine strength and clarity, making them ideal for industries such as agriculture, construction, and retail. Their transparent nature allows end-users to identify contents easily, while their woven structure ensures resistance to tearing and puncturing. Moreover, Woven Bag Manufacturers like VidePak employ cutting-edge technology to enhance their durability and aesthetics.
Explore VidePak’s commitment to sustainability with Transparent Woven Bags.
Critical Parameters in Bag Design
Parameter | Description |
---|---|
Material Composition | PP and HDPE polymers ensure strength, lightweight structure, and environmental resilience. |
Bag Dimensions | Customizable to accommodate varying product weights and volumes, from 10 kg to 50 kg or more. |
Transparency Level | Adjusted through polymer blends or surface lamination to balance content visibility and UV protection. |
Printing Capabilities | Multi-color, high-resolution designs support branding and product information. |
Sewing Techniques: Selecting the Right Method
Transparent Woven Bags’ durability depends largely on the techniques used in their construction. Several methods contribute to creating bags that withstand heavy loads and harsh conditions.
Bottom Sealing Options
- Stitched Bottom Sealing
- Overview: Traditional method using sewing machines with reinforced threads.
- Advantages: Highly durable and suitable for heavy loads.
- Challenges: Requires precise thread tension to prevent unraveling.
- Applications: Bulk grain, fertilizer, and cement packaging.
- Heat-Sealed Bottom
- Overview: Utilizes heat to bond layers of woven fabric.
- Advantages: Provides a seamless, leak-proof finish ideal for fine powders.
- Challenges: Requires advanced equipment and precise temperature control.
- Applications: Industrial powders and chemical packaging.
- Ultrasonic Welding
- Overview: Combines fabric layers using high-frequency vibrations.
- Advantages: Fast, precise, and eco-friendly, as it eliminates the need for adhesives.
- Challenges: Higher initial investment in machinery.
- Applications: Food-grade packaging and moisture-sensitive products.
Stitching Thread Material and Density
Thread Type | Properties | Best For |
---|---|---|
Polyester Threads | High tensile strength, resistant to moisture and UV. | Heavy-duty outdoor bags. |
Polypropylene Threads | Lightweight and cost-effective. | General-purpose HDPE Bags. |
Cotton Threads | Eco-friendly but less durable. | Niche biodegradable bags. |
The stitching density, expressed as stitches per inch, significantly influences the bag’s durability:
- 6–8 stitches/inch: Standard for lightweight materials.
- 8–10 stitches/inch: Recommended for medium-duty applications.
- 10–12 stitches/inch: Ideal for heavy-duty and high-load scenarios.
Variations in Bag Mouth Design
Transparent Woven Sacks cater to diverse usage requirements through customizable bag openings. The design of the bag mouth directly impacts filling and sealing efficiency.
Open-Mouth Design
- Features: Simple, wide opening for manual or automated filling.
- Advantages: Cost-effective and easy to use.
- Applications: Packaging grains, seeds, or construction materials.
Valve-Type Mouth
- Features: Includes a valve for self-sealing upon filling.
- Advantages: Minimizes spillage and facilitates automated filling processes.
- Applications: Cement and powdered chemicals.
Heat-Sealed Mouth
- Features: Combines woven fabric with a heat-sealed closure.
- Advantages: Leak-proof and tamper-resistant.
- Applications: Industrial powders and food products.
Stitched Closure
- Features: Sewn shut after filling.
- Advantages: High strength and reusability.
- Applications: Bulk packaging for agricultural products.
Comparing Techniques for Efficiency and Cost
Technique | Durability | Sealing Quality | Cost Efficiency | Use Cases |
---|---|---|---|---|
Stitched Bottom | High | Moderate | Cost-effective | Heavy-duty agricultural bags. |
Heat-Sealed Bottom | Moderate | High | Moderate | Fine powders and moisture-sensitive. |
Ultrasonic Welding | High | Very High | High | Premium industrial and food-grade. |
HDPE Bags: An Ideal Material Choice
HDPE Woven Bags, known for their exceptional strength-to-weight ratio, are preferred by Woven Bag Manufacturers for their durability and resistance to chemicals, UV rays, and moisture. HDPE’s versatility supports various sealing and stitching techniques while maintaining environmental compliance.
Discover the advantages of HDPE Woven Bags in innovative packaging.
Conclusion
Transparent Woven Bags and HDPE Woven Bags provide robust and flexible solutions for modern packaging needs. Selecting the appropriate production and sealing techniques ensures these bags meet specific industry demands while upholding quality and efficiency. From stitched closures to ultrasonic sealing, these manufacturing methods empower industries to achieve packaging excellence.