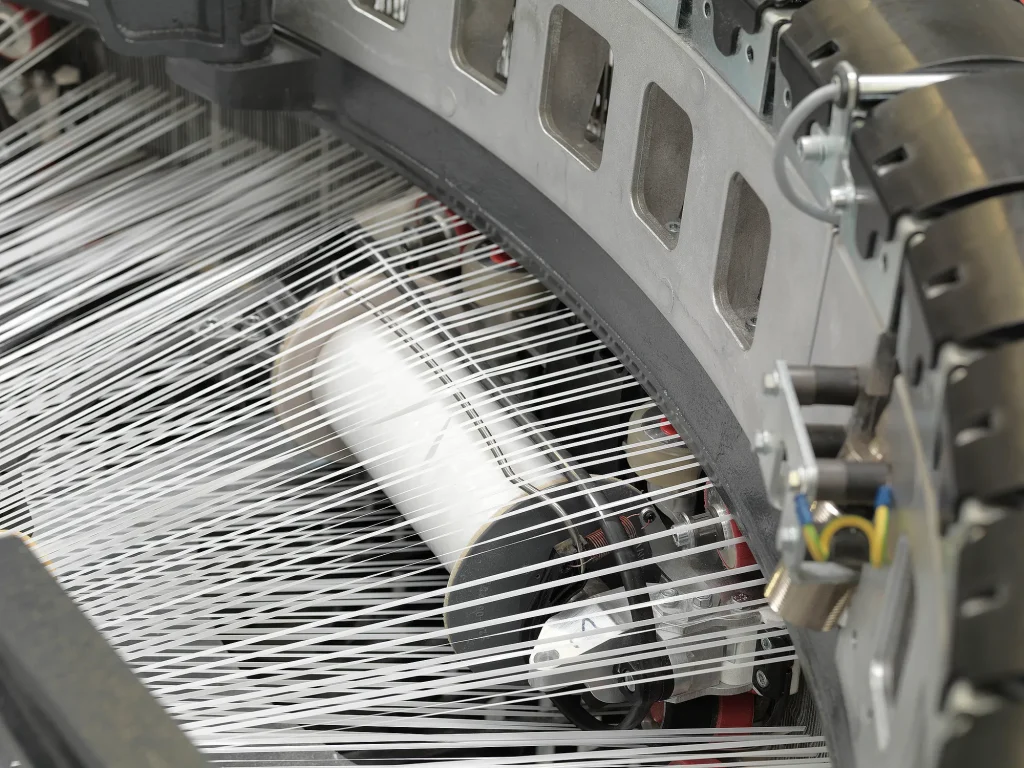
This article addresses three critical questions for industrial buyers: (1) How do Starlinger and W&H extrusion technologies ensure consistent quality in open-mouth PP bag production? (2) What role do filament temperature and draw ratio play in optimizing tensile strength and energy efficiency? (3) Why does VidePak’s 30+ years of expertise position it as a global leader in high-performance woven packaging? With 568 employees, 100+ Starlinger circular looms, and ISO 9001-certified processes, VidePak produces 15 million open-mouth PP bags monthly, achieving ±2% dimensional tolerance and ≤0.5% defect rates. Our 16 extrusion lines and 30+ printing machines deliver 40–60 N/cm² tensile strength while reducing energy consumption by 25% compared to industry averages.
1. Production Workflow: From Polymer to Precision Woven Bags
1.1 Extrusion: Controlling Filament Temperature for Optimal Crystallinity
VidePak’s Starlinger extrusion systems melt virgin PP resin (MFI 2.5–4.0 g/10min) at precisely controlled temperatures:
- Zone 1 (Feeding): 180–200°C to pre-melt granules.
- Zone 2 (Compression): 220–240°C for uniform polymer flow.
- Zone 3 (Metering): 200–210°C to stabilize melt viscosity.
Impact of Temperature Variance:
- Underheating (<200°C): Causes incomplete melting, leading to weak spots (≤35 N/cm² tensile).
- Overheating (>250°C): Degrades PP chains, reducing elongation at break by 30%.
Case Study: A fertilizer client required bags with 50 N/cm² tensile strength. By maintaining 225°C in Zone 2, VidePak achieved 53 N/cm² with ±1.5% batch consistency.
1.2 Filament Drawing: Balancing Draw Ratio and Energy Efficiency
Starlinger’s AD*Star® technology adjusts draw ratios (5:1 to 7:1) in real-time via servo motors:
Draw Ratio | Filament Thickness | Tensile Strength | Energy Use |
---|---|---|---|
5:1 | 80–100 denier | 40–45 N/cm² | 0.8 kWh/kg |
6:1 | 60–80 denier | 50–55 N/cm² | 1.0 kWh/kg |
7:1 | 40–60 denier | 60–65 N/cm² | 1.2 kWh/kg |
Example: For pet food packaging requiring 55 N/cm² strength, a 6.5:1 ratio optimized energy use while meeting specifications.
2. Weaving and Quality Control: How Technology Ensures Consistency
2.1 Circular Loom Precision with Starlinger ATLAS 2.0
VidePak’s 100+ Starlinger looms integrate IoT-enabled ATLAS 2.0 systems to monitor:
- Weaving Speed: 120–150 rpm, adjusted for tape width (2.5–5.0 mm).
- Warp/Weft Alignment: Laser sensors ensure ≤0.3 mm deviation.
- Fabric Density: 10×10 to 14×14 threads/inch, controlled via real-time tension feedback.
Quality Impact:
- High Density (14×14): 15% higher abrasion resistance (ASTM D5264).
- Low Density (10×10): 20% faster production speed.
2.2 W&H Lamination: Sealing Performance and Barrier Integrity
For laminated open-mouth bags, W&H Novotec 500 systems apply BOPP films (20–30 µm) at:
- Temperature: 175–185°C for PP-to-PP bonding.
- Pressure: 3.0–4.0 N/mm² to eliminate air pockets.
- Adhesion Strength: ≥3.5 N/15mm (tested per ASTM F904).
Case Study: A chemical manufacturer required moisture barriers <0.1 g/m²/day. VidePak’s 25 µm BOPP lamination achieved 0.08 g/m²/day WVTR.
3. Sustainability and Cost Efficiency: The VidePak Advantage
3.1 Energy-Saving Technologies
- Heat Recovery: Starlinger’s EcoPower system recycles 40% of extrusion heat.
- Solar Integration: 2MW rooftop panels reduce grid dependency by 35%.
3.2 Waste Reduction
- PP Recycling: 98% of production scrap reused via inline granulators.
- Ink Optimization: Digital dosing systems cut ink waste by 22%.
4. FAQs: Addressing Industrial Buyers’ Concerns
Q1: How does filament temperature affect bag durability?
Optimal melting (220–240°C) ensures polymer crystallinity ≥65%, directly correlating to tensile strength.
Q2: Can open-mouth bags handle 50kg dynamic loads?
Yes. Our 14×14 weave design with 6:1 draw ratio achieves 60 N/cm² tensile strength (ISO 13934-1).
Q3: What’s the lead time for custom-printed orders?
18–22 days for 20,000+ units, utilizing 30+ W&H printing machines.
5. Why Choose VidePak?
- Global Reach: Serving 60+ countries with $80M annual revenue.
- Certifications: BRCGS, ISO 9001, and ISO 14001.
- Innovation: RFID-enabled bags for supply chain tracking (pilot phase).
Explore our open-mouth PP bag solutions or learn about advanced extrusion technologies.
References
- ASTM International. (2025). Standard Test Methods for Tensile Properties of Plastics.
- Starlinger & Co. (2024). Technical Manual for ADStar® Systems*.
- Made-in-China. (2025). PP Woven Bag Production Specifications.
- VidePak. (2024). Sustainability and Quality Assurance Report.
Contact VidePak
Website: https://www.pp-wovenbags.com/
Email: info@pp-wovenbags.com