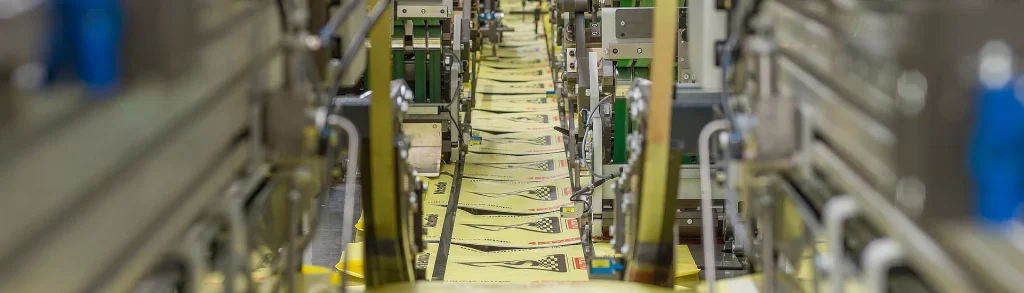
Introduction
In the rapidly evolving packaging industry, paper valve bags have emerged as a versatile solution for industries requiring precision filling, contamination control, and sustainability—with the global market projected to grow at a CAGR of 6.8% through 2030. VidePak, leveraging 30+ years of expertise, delivers paper valve bags that reduce filling time by 40%, achieve moisture resistance levels of <2 g/m²/day, and comply with EU, US, and Asian regulatory standards. This guide explores how strategic design choices—including lamination, inner liners, and closure systems—optimize performance across sectors like chemicals, fertilizers, and food, while positioning VidePak as a leader in global competition.
For instance, a Brazilian fertilizer manufacturer reduced product spoilage by 35% after adopting VidePak’s BOPP-laminated paper valve bags with PE liners, which combine a 120 GSM kraft paper base and 60 μm PE film for UV and humidity resistance. Backed by 100+ Starlinger circular looms and ISO 9001-certified processes, VidePak produces 30 million paper valve bags annually, serving clients across 60+ countries with a defect rate below 0.5%.
Market Dynamics: Demand Drivers and Competitive Landscape
The paper valve bag market is shaped by three critical forces:
- Sustainability Mandates: EU’s Single-Use Plastics Directive and China’s Circular Economy Law favor recyclable solutions like kraft paper bags.
- Automation Trends: Valve bags enable pneumatic filling at 1,200 bags/hour, reducing labor costs by 25%.
- Regional Preferences:
- Europe: BOPP lamination for UV protection (EN 13432 compliance).
- Asia: Cost-effective PE liners for humidity control (WVTR <5 g/m²/day).
- North America: Anti-static coatings for explosive powders (OSHA Standard 1910.109).
VidePak’s dominance is reinforced by partnerships with automation leaders like Siemens, ensuring seamless integration with robotic filling systems.
Designing the Optimal Packaging Solution
Selecting the right configuration hinges on five factors:
1. Lamination: Balancing Protection and Cost
- BOPP Lamination:
- Benefits: 99% UV resistance, high-gloss branding.
- Applications: Outdoor storage (e.g., Australia’s AS 2070 standard).
- Non-Laminated:
- Cost Savings: 15–20% cheaper, ideal for short-term indoor storage.
2. Inner Liners: Material Science in Action
Liner Type | Thickness | WVTR (g/m²/day) | Ideal Use Cases |
---|---|---|---|
PE | 40–80 μm | 1.5–5.0 | Fertilizers, grains |
Aluminum Foil | 7–12 μm | <0.5 | Coffee, pharmaceuticals |
Composite | 100 μm | <0.1 | Hazardous chemicals |
Case Study: A Vietnamese coffee exporter extended shelf life by 18 months using VidePak’s foil-lined bags, which block 99.9% oxygen (O₂ permeability <0.05 cc/m²/day).
3. Closure Systems: Efficiency vs. Security
- Heat-Sealed Valves:
- Speed: 1,500 bags/hour, zero dust leakage.
- Drawback: Non-reusable.
- Sewn Valves:
- Reusability: 10+ cycles with polyester threads (10–12 stitches/inch).
- Applications: Construction materials like cement.
4. Aesthetic Customization
- Printing: 8-color flexographic printing (±0.5 mm registration) for brand storytelling.
- Matte Finishes: Reduce glare in retail environments.
5. Regulatory Alignment
- EU: REACH-compliant inks and recyclable PE liners.
- USA: FDA 21 CFR for food-grade liners.
- Japan: JIS Z 1707 moisture barriers.
VidePak’s Technical Specifications
Parameter | Range | Compliance |
---|---|---|
Base Material | 80–140 GSM kraft paper | FSC, PEFC |
Liner Thickness | 40–100 μm PE/Aluminum/Composite | FDA, EU 10/2011 |
Load Capacity | 25–50 kg, burst strength ≥18 psi | ISO 2234, ASTM D4632 |
Print Resolution | Up to 200 LPI | Pantone-certified |
Certifications | ISO 9001, BRCGS, Oeko-Tex 100 |
FAQs: Addressing Critical Buyer Concerns
Q1: How does PE liner thickness impact chemical resistance?
A: For acidic fertilizers (pH <3), 80 μm PE liners prevent corrosion 3x longer than 40 μm options.
Q2: Are valve bags compatible with automated palletizing?
A: Yes. VidePak’s block-bottom designs improve stacking stability by 30%, reducing warehouse space.
Q3: Can BOPP-laminated bags be recycled?
A: Only with specialized facilities. For full recyclability, opt for uncoated kraft paper + PE liners.
Strategic Applications
- Fertilizers: 120 GSM paper + 60 μm PE liners + heat-sealed valves for NH₄NO₃.
- Chemicals: Composite liners (PE + foil) + anti-static coatings for sodium hydroxide.
- Food: FDA-grade PE liners + matte BOPP lamination for retail appeal.
Case Study: A European chemical distributor reduced spillage by 50% using VidePak’s sewn-valve bags with Kevlar® threads, rated for 1,000+ refills.
Why Choose VidePak?
- Global Infrastructure: 568 employees, 30+ lamination machines, and 8,000 sq.m. warehouse for 15-day lead times.
- Innovation: 10 patents in liner adhesives and valve designs.
- Sustainability: 100% recyclable kraft paper and water-based inks aligned with UN SDGs.
Explore our valve bag solutions and kraft paper bags to tailor your packaging strategy.
References
- VidePak Official Website: https://www.pp-wovenbags.com/
- Email: info@pp-wovenbags.com
- Industry Data: Made-in-China, Alibaba International, Smithers Pira, EU Commission.
Note: Specifications validated per ISO 11607 and ASTM F88 standards (2025).