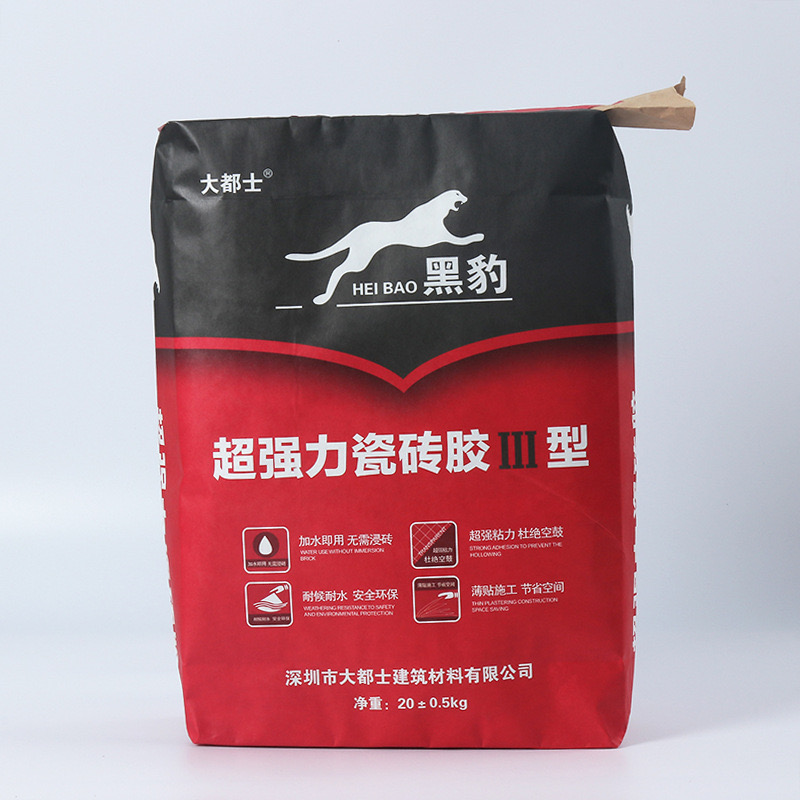
- Key Characteristics of Pasted Valve Bags
- Applications in High-Moisture Environments
- Seven-Layer Co-Extruded Films: Key Benefits for Valve Bags
- Comparison of Bag Types: Valve PP Bags vs. Sewn Open Mouth Bags vs. Block Bottom Bags
- Key Features of Sewn Open Mouth Bags and Block Bottom Bags
- Applications of Multi-Layer Film Technology
- Conclusion
In the packaging industry, Pasted Valve Bags are recognized for their convenience, durability, and advanced design. These bags, often used in sectors requiring airtight storage, come equipped with unique valve openings that make filling fast, easy, and automated. Combining strength and versatility, they are particularly suitable for handling heavy-duty materials. In industries where protection against moisture and other environmental factors is essential, seven-layer co-extruded films add another layer of resilience and functionality to these bags. This article delves into the distinctive qualities and applications of Pasted Valve Bags, highlighting the specialized seven-layer co-extrusion technology that enhances their water resistance and visual appeal.
Key Characteristics of Pasted Valve Bags
Pasted Valve Bags, also known as Pasted Valve Sacks or Valve PP Bags, are engineered to accommodate various materials, including cement, chemicals, and agricultural products. Their defining feature is the valve opening, which enables easy, controlled filling and a secure seal upon closing. Here’s a closer look at their key characteristics:
- Convenient Valve Mechanism
The integrated valve allows for efficient filling without needing an external closure mechanism. Once filled, the valve is designed to self-seal under pressure, preventing leakage and contamination. - Durability and Load-Bearing Capacity
Made from woven polypropylene (PP) and reinforced with multiple layers, Pasted Valve Bags are built to handle the rigorous demands of transportation and storage. They can support weights of up to 50 kg, making them ideal for heavy products like cement and sand. - Block Bottom Design
The block bottom shape provides stability during stacking and storage, ensuring maximum space efficiency. This design also improves the bag’s aesthetic appeal, offering a neat and organized look. - Moisture and Contaminant Resistance
By incorporating advanced barrier films, these bags protect contents from moisture, ensuring the preservation of the product’s quality over time. Industries handling moisture-sensitive products find Pasted Valve Bags ideal for maintaining product integrity. - Compatibility with Automation
Pasted Valve Bags can seamlessly integrate with automated filling systems, reducing labor costs and minimizing filling time. This automation compatibility is particularly beneficial for high-volume packaging lines.
The following table summarizes some common parameters for standard Pasted Valve Bags, highlighting their customizability and load-bearing capacity:
Parameter | Specification | Details |
---|---|---|
Bag Material | Woven Polypropylene | Durable, tear-resistant |
Film Coating | BOPP or PE | Adds moisture and UV protection |
Valve Type | Self-sealing Valve | Easy, automated filling |
Typical Sizes | 25kg to 50kg capacity | Customizable sizes available |
Printing | Up to 10 colors | Customizable for branding |
Environmental Resistance | Waterproof, UV resistant | Suitable for outdoor storage |
For more on the benefits and applications of Pasted Valve Bags, VidePak offers extensive resources.
Applications in High-Moisture Environments
For applications requiring enhanced water and moisture resistance, seven-layer co-extrusion technology adds a critical advantage to Valve Bags for Packaging. These applications include environments where the contents must be shielded from high humidity or potential liquid exposure. The multi-layered design of these bags provides several advantages:
- Layered Barrier Protection
Seven-layer co-extrusion creates a film that blocks moisture and vapor, keeping contents dry and free from contamination. This design ensures optimal protection, even in the most demanding conditions. - Improved Aesthetics and Print Quality
The multiple layers allow for high-quality printing, creating visually appealing, branded bags. Customers appreciate the flexibility to customize designs without sacrificing durability. - Enhanced Structural Integrity
The layers reinforce the bag’s structure, providing better resistance to tears and punctures. This is essential for handling abrasive or coarse materials, like sand or gravel, which can compromise thinner bags.
Industries that benefit from these enhanced Pasted Valve Sacks include construction, chemical manufacturing, and agriculture, where moisture protection is crucial. Pasted Valve Sacks are also popular in sectors requiring secure, long-term storage of powdery materials.
Seven-Layer Co-Extruded Films: Key Benefits for Valve Bags
Incorporating seven-layer co-extruded films into Valve Bags for Packaging offers superior moisture protection, dust control, and appearance. This innovative technology ensures that products are safeguarded against external factors, including humidity, dirt, and chemical contaminants, making them especially suited for high-moisture applications.
Advantages of Seven-Layer Co-Extrusion in Valve Bags
- Enhanced Barrier Performance: The multi-layered structure blocks moisture, oxygen, and UV radiation, effectively protecting sensitive materials from degradation.
- Seamless Lamination: Seven-layer films are seamlessly laminated to the woven fabric, providing a sleek surface that’s easy to print on and resistant to environmental wear.
- Long-Term Durability: The layered design is resistant to deformation, making the bags less prone to breaking down under repeated handling or prolonged storage.
Given the significance of moisture control and preservation, the design of these bags contributes to a longer shelf life, particularly for materials that are sensitive to moisture, such as fertilizers and cement. Valve Bags for Packaging made with seven-layer films serve as a reliable choice for demanding storage requirements.
Comparison of Bag Types: Valve PP Bags vs. Sewn Open Mouth Bags vs. Block Bottom Bags
In the industry, different bag designs address various packaging needs. Below is a comparison of Valve PP Bags, Sewn Open Mouth Bags, and Block Bottom Bags, highlighting each type’s unique advantages.
Feature | Valve PP Bags | Sewn Open Mouth Bags | Block Bottom Bags |
---|---|---|---|
Filling Mechanism | Self-sealing valve | Open mouth, sewn closure | Folded bottom with valve |
Stacking Efficiency | High, due to block shape | Moderate, open design | High, block bottom structure |
Moisture Resistance | High, with barrier films | Moderate, depends on material | High, suitable for powders |
Best Use Cases | Cement, fertilizers | Grains, bulk goods | Chemicals, powdery materials |
Customization Options | Printing, size, film | Printing, gusset options | Printing, multi-layer films |
Key Features of Sewn Open Mouth Bags and Block Bottom Bags
Apart from Valve PP Bags, other bag types also cater to specific packaging needs. Sewn Open Mouth Bags, for instance, are a popular choice for bulk grains and granular materials. They are easy to fill and are available in various designs, with or without gussets. Meanwhile, Block Bottom Bags combine durability and storage efficiency, as their shape enables compact stacking and prevents product spillage.
Applications of Multi-Layer Film Technology
The multi-layer film technology used in Valve Bags is also applied to various types of industrial bags, enhancing their durability and usability in harsh environments. Below are some applications of this technology:
- Construction Material Packaging: Seven-layer co-extrusion adds an impermeable layer that protects against water and dust, ideal for cement and sand packaging.
- Chemical Industry: For transporting chemicals, these bags offer a barrier against moisture, safeguarding chemical integrity.
- Agricultural Sector: Protects seeds, fertilizers, and animal feed from environmental factors, preserving their quality and efficacy.
Conclusion
Pasted Valve Bags stand out for their durability, efficiency, and versatility in packaging applications. Their advanced valve design, coupled with seven-layer co-extrusion technology, provides a solution that meets high standards for moisture protection and load-bearing capacity. Whether for industrial, agricultural, or construction use, these bags offer unmatched performance. Through VidePak’s commitment to quality and innovation, customers can rely on solutions that deliver not only functional benefits but also the aesthetic appeal needed for effective branding and market differentiation.