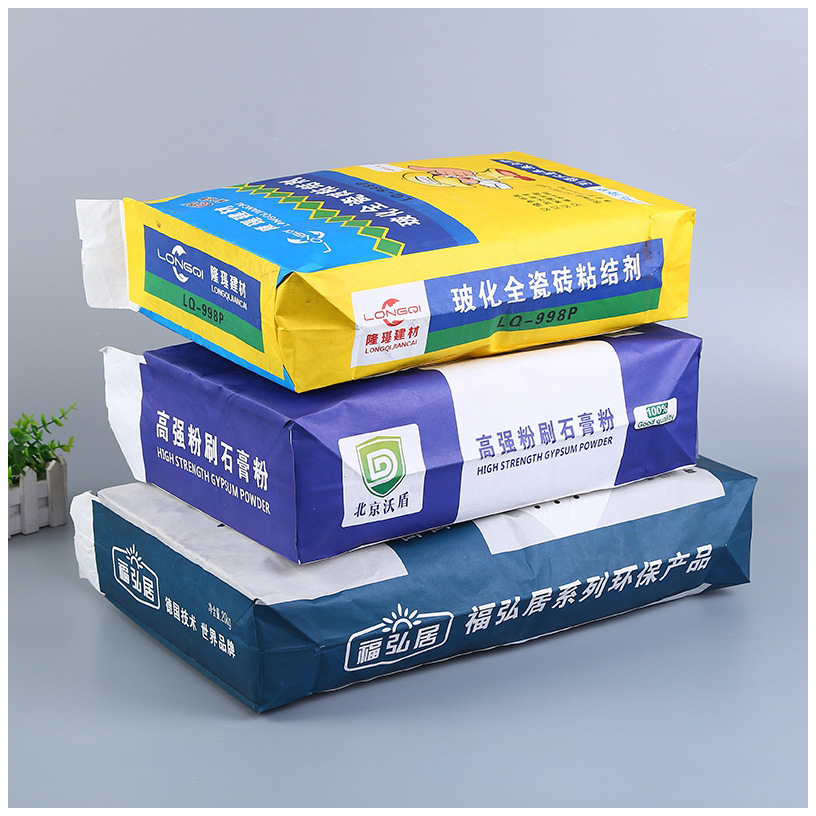
When it comes to packaging solutions, Pasted Valve Bags are a versatile and cost-effective choice. They are commonly used for packaging a variety of materials, including powders, grains, and chemicals, providing excellent protection and ensuring safe storage and transportation. In this article, we will discuss the unique features of Pasted Valve Sacks, the materials used in their production, and the critical quality control measures employed to ensure top-tier performance.
Additionally, we will examine the rigorous quality testing processes that Valve Bags for Packaging undergo, particularly when it comes to the raw materials, such as PP (Polypropylene) and PE (Polyethylene) pellets, used in their manufacture. Understanding these elements is vital to ensuring that every Valve PP Bag delivers the reliability and strength expected from industrial packaging.
1. Characteristics of Pasted Valve Bags
Pasted Valve Bags are designed for a range of packaging applications, offering a secure and efficient way to pack a variety of dry goods. Some of the key features that make Pasted Valve Sacks a popular choice include:
1.1. Structural Design
The defining feature of a Pasted Valve Bag is its valve closure system, which allows for easy filling and sealing. The valve is typically sewn onto the bag’s opening, and when the filling process is complete, it can be sealed by applying paste or adhesive. This valve system is not only convenient but also ensures that the contents remain securely inside, minimizing the risk of spillage.
1.2. Material Versatility
Pasted Valve Bags can be made from various materials, but PP (Polypropylene) is the most common choice due to its durability, lightweight nature, and resistance to moisture. These bags are often used in the packaging of agricultural products like fertilizers, grains, and chemicals, as well as non-food industrial goods.
1.3. Customizable Features
A significant advantage of Pasted Valve Bags is the ability to customize them according to customer needs. The bags can be made in different sizes, with various valve openings to suit different filling machines, and can be printed with custom branding or labels. Additionally, some bags are laminated or reinforced for extra durability.
1.4. Cost-Effectiveness
Compared to other types of industrial bags like Sewn Open Mouth Bags or Block Bottom Bags, Pasted Valve Sacks offer a more economical packaging solution. Their simple, efficient design minimizes labor costs during packaging and handling.
2. Material Quality Testing: Ensuring the Best Performance of Pasted Valve Bags
To produce high-quality Valve Bags for Packaging, the raw materials—primarily PP and PE pellets—must undergo stringent testing. These tests help ensure that the bags maintain their integrity under various conditions and provide the necessary strength to handle the contents securely.
2.1. Appearance Inspection
The first step in quality control is visually inspecting the PP and PE pellets for any impurities or defects. Pellets that are discolored, have uneven shapes, or are contaminated may lead to weak or defective bags. Ensuring that only clean, consistent pellets are used is the foundation of high-quality production.
2.2. Melt Flow Index (MFI)
The Melt Flow Index (MFI) is a critical measure of a material’s viscosity when heated. This test determines the flow characteristics of the polymer when it is processed. For Pasted Valve Bags, the MFI needs to be within an optimal range to ensure that the material can be extruded and formed into a bag without compromising its strength or flexibility. A lower MFI indicates a higher molecular weight and greater material strength, while a higher MFI suggests a quicker processing rate but may reduce strength.
2.3. Density Testing
Density testing is used to assess the compactness and structure of the material. Higher-density materials tend to offer better strength and durability, which is crucial for Valve PP Bags that need to withstand the weight and pressure of their contents. This test helps confirm that the material used for bag production is up to industry standards.
2.4. Tensile Strength and Elongation at Break
To ensure that Pasted Valve Bags perform reliably under stress, tensile strength and elongation at break tests are conducted. Tensile strength measures the maximum load the material can handle before breaking, while elongation at break tests how far the material can stretch before failure. These properties are particularly important in industrial applications where the bags are likely to be subjected to heavy weights and rough handling.
Property | Specification | Test Result (Typical) |
---|---|---|
Tensile Strength | Minimum 15 MPa | 18 MPa |
Elongation at Break | Minimum 10% | 12% |
Density | 0.91–0.92 g/cm³ | 0.91 g/cm³ |
Melt Flow Index (MFI) | 2–5 g/10 min | 3 g/10 min |
2.5. Thermal Properties
Given the varied environmental conditions in which Pasted Valve Sacks are used, testing the material’s thermal properties is crucial. These properties indicate how well the material can withstand high and low temperatures without degrading or losing structural integrity. Polypropylene, the primary material used in Valve Bags for Packaging, typically has a melting point of around 160°C, which ensures it can handle the temperatures associated with industrial processes.
2.6. Chemical Resistance
Since many Pasted Valve Bags are used to contain chemicals, it is essential to test the material’s chemical resistance. The PP material must be able to withstand exposure to oils, acids, and other potentially corrosive substances without breaking down. Manufacturers perform accelerated aging tests and immersion tests to verify that the material retains its integrity in different environments.
2.7. UV Resistance
For bags exposed to outdoor elements, UV resistance is an important quality parameter. UV degradation can cause materials to become brittle and crack over time. By testing the material’s UV resistance, manufacturers can ensure that Pasted Valve Bags will provide long-lasting protection, even when exposed to sunlight for extended periods.
3. Frequently Asked Questions (FAQs)
3.1. What are Pasted Valve Bags used for?
Pasted Valve Bags are commonly used in the packaging of agricultural products (such as fertilizers and grains), chemicals, and other industrial goods. Their valve system makes them suitable for efficient and secure filling.
3.2. How does the valve system work in Pasted Valve Sacks?
The valve system in Pasted Valve Sacks is typically made from a sewn or pasted opening that can be closed once the bag is filled. This valve allows for quick and efficient filling, minimizing the chances of spillage.
3.3. Can Pasted Valve Bags be customized?
Yes, Pasted Valve Bags can be customized in terms of size, valve opening, and printed branding. Lamination or reinforcement can also be applied for additional durability.
3.4. What is the difference between Pasted Valve Bags and Sewn Open Mouth Bags?
While both are used for similar packaging applications, Sewn Open Mouth Bags require manual sewing to seal the top, while Pasted Valve Bags use a valve system for more efficient, automated filling and sealing.
3.5. How are Pasted Valve Bags tested for quality?
Pasted Valve Bags undergo several tests, including appearance inspection, melt flow index (MFI) testing, density analysis, tensile strength, and elongation tests, thermal and chemical resistance testing, and UV resistance tests to ensure durability and performance.
In conclusion, Pasted Valve Bags represent an excellent packaging solution for a wide range of industries. With their valve closure system, customizable features, and cost-effective production, they offer both efficiency and security. The stringent material testing processes ensure that Pasted Valve Bags provide the necessary strength, durability, and resistance to meet the demands of industrial and agricultural applications. To learn more about how Valve Bags for Packaging can optimize your packaging process, explore VidePak’s approach to enhancing logistics with Pasted Valve Bags and the versatility of Valve Bags for Packaging.