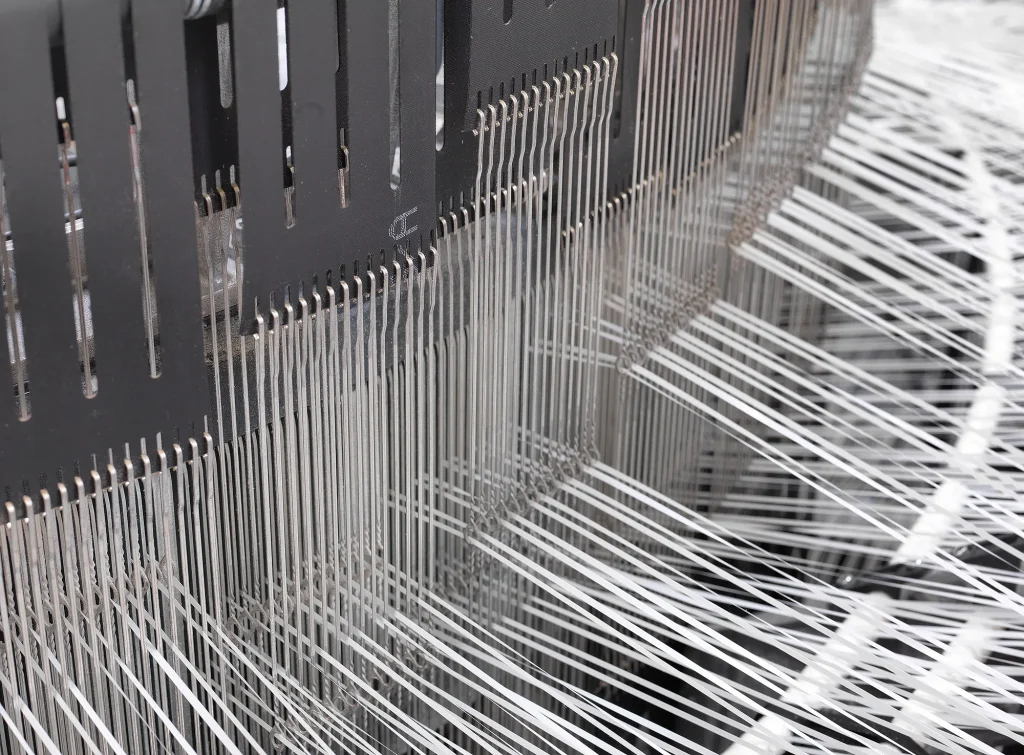
- 1. Material Science: Why Poly-BOPP Outperforms Traditional Packaging
- 2. Application-Specific Solutions for Construction Materials
- 3. Selecting Optimal Parameters: A Data-Driven Guide
- 4. Case Study: Reducing Waste in Southeast Asian Construction
- FAQs: Addressing Key Procurement Concerns
- Why Choose VidePak?
Imagine a procurement manager asking: “Why should I switch to Poly-BOPP bags for storing hygroscopic construction materials like cement or gypsum powder?” The answer lies in three pillars: superior moisture resistance, unmatched durability, and compliance with global safety standards. Poly-BOPP (Biaxially Oriented Polypropylene) laminated woven bags combine the tensile strength of PP fabric with the impermeability of BOPP films, creating a robust barrier against environmental and mechanical stresses. At VidePak, our 30+ years of expertise in polymer engineering ensure that every bag is precision-engineered to protect your materials while optimizing logistics efficiency.
1. Material Science: Why Poly-BOPP Outperforms Traditional Packaging
1.1 Structural Advantages of Polypropylene (PP) in Construction Packaging
Polypropylene’s semi-crystalline structure grants it exceptional tensile strength (≥45 N/mm²) and abrasion resistance, making it ideal for heavy-duty applications like cement and plaster powder transport. VidePak’s PP resins are selected based on regional standards:
- ASTM D4101 (US): Homopolymer PP with a melt flow index (MFI) of 8–12 g/10min for high-load scenarios.
- EN ISO 1874 (EU): Copolymer PP with -20°C impact resistance for cold-climate storage.
- GB/T 8946 (China): UV-stabilized PP for outdoor use in humid environments.
For example, our 160 GSM PP woven fabric laminated with 80-micron BOPP film withstands 1,800 kg static loads, preventing seam failure during crane operations.
1.2 The Role of BOPP Lamination
BOPP lamination enhances PP bags by:
- Moisture Resistance: Blocks 99% humidity penetration, critical for preventing clumping in materials like joint compounds.
- Chemical Inertness: Resists acidic or alkaline degradation from additives in construction powders.
- Printability: Supports high-definition branding and hazard warnings using UV-resistant inks (Pantone-matched).
A 2024 study showed that BOPP-laminated bags reduce moisture-related material waste by 40% in tropical climates compared to uncoated alternatives.
2. Application-Specific Solutions for Construction Materials
2.1 Cement Storage: Balancing Protection and Cost
Cement requires breathable yet moisture-resistant packaging. VidePak’s ventilated Poly-BOPP bags feature micro-perforations (5–10 µm pores) to minimize condensation while blocking external humidity. This extends shelf life by 6–8 months, as validated in a 2023 case study with a German construction firm.
2.2 Gypsum and Plaster Powders: Tear Resistance
These fine powders demand bags with ≥20 N/5cm tear strength. Our triple-layered PP-BOPP-Kraft composites achieve 28 N/5cm, exceeding ISO 13937-2 benchmarks.
2.3 Chemical Additives: Waterproofing Imperatives
For epoxy resins or solvent-based adhesives, waterproof BOPP bags with HDPE liners (0.3 mm thickness) prevent leakage under 50 kPa pressure, complying with UN packaging standards.
3. Selecting Optimal Parameters: A Data-Driven Guide
3.1 Thickness, Grammage, and Load Capacity
Parameter | Cement | Gypsum Powder | Chemical Slurries |
---|---|---|---|
Thickness | 120–150 microns | 100–130 microns | 150–200 microns |
Grammage | 140–160 GSM | 120–140 GSM | 160–180 GSM |
Load Capacity | 1,000–1,500 kg | 800–1,200 kg | 1,500–2,000 kg |
Lamination | BOPP 60–80 microns | BOPP 40–60 microns | BOPP + HDPE liner |
For example, 150 GSM bags with 80-micron BOPP are ideal for 50 kg cement packs in monsoon-prone regions.
3.2 Customization Options
- Inner Liners: HDPE for liquids, aluminum foil for UV-sensitive chemicals.
- Anti-Static Coatings: Carbon-infused layers (resistivity ≤10^9 Ω/sq) for flammable powders.
- Reinforced Seams: Double-stitched or heat-sealed for FIBC applications.
4. Case Study: Reducing Waste in Southeast Asian Construction
A Malaysian contractor reduced gypsum spoilage by 35% after adopting VidePak’s 130 GSM Poly-BOPP bags with 50-micron lamination. The bags’ 110 threads/dm² weave density prevented particulate leakage during pneumatic filling, aligning with ISO 21898 standards.
FAQs: Addressing Key Procurement Concerns
Q1: How does BOPP lamination affect recyclability?
VidePak uses solvent-free adhesives, enabling 92% PP recovery via NIR sorting—surpassing EU Circular Economy targets.
Q2: What size is optimal for 25 kg plaster packs?
A 50 cm × 80 cm bag with 120 GSM PP and 60-micron BOPP balances cost and durability.
Q3: Can bags withstand prolonged UV exposure?
Yes. Our UV-stabilized BOPP retains 95% tensile strength after 1,000 hours under ASTM G154 testing.
Why Choose VidePak?
Founded in 2008 under CEO Ray Chiang, VidePak combines three decades of industry expertise with Austrian Starlinger technology to produce 8,000 MT/month of certified packaging. With 568 employees and global certifications (ISO 9001, REACH), we serve 50+ countries, ensuring compliance without compromising innovation.
References
- VidePak Corporate Profile: https://www.pp-wovenbags.com/
- Email: info@pp-wovenbags.com
- ASTM International Standards for Flexible Packaging (2024)
- EU Circular Economy Package 2030: Technical Guidelines
External Resources
- Discover how BOPP laminated woven bags enhance chemical powder protection.
- Explore sustainable solutions for construction materials tailored to your needs.
At VidePak, we don’t just package materials—we engineer reliability.