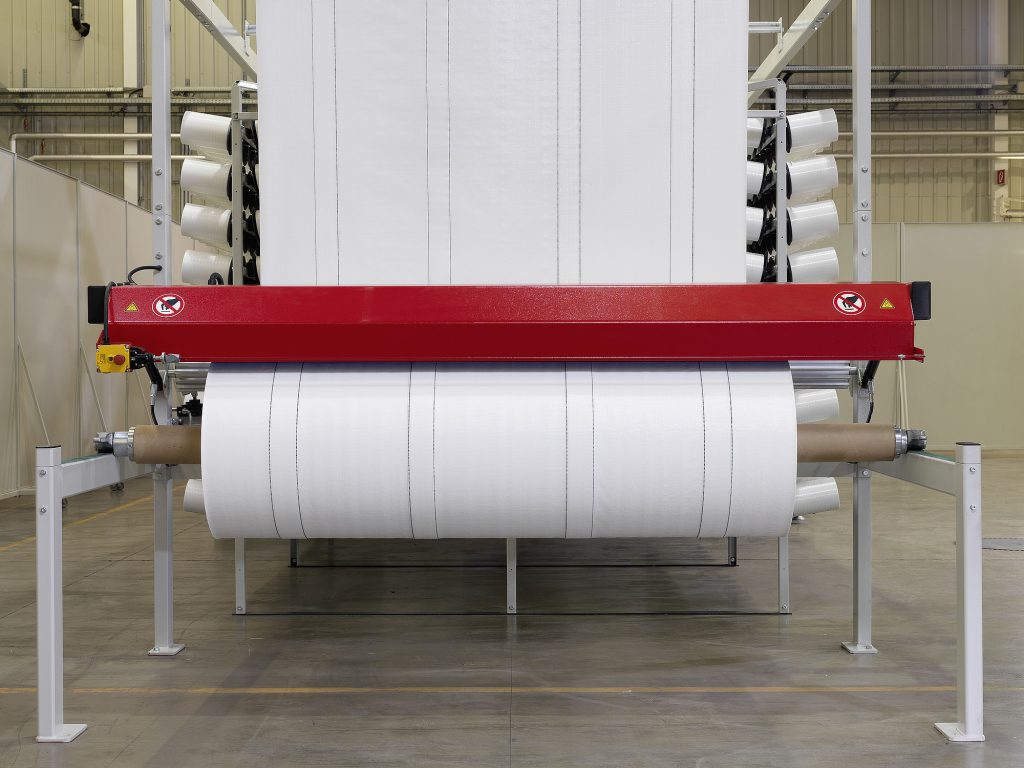
The Key Answer: Poly-BOPP (biaxially oriented polypropylene) bags excel in customizability and functional diversity, with ultrasonic welding and heat sealing emerging as optimal closure methods for high-speed production and airtight sealing. Valve and block-bottom designs dominate industrial applications, offering 30–40% higher efficiency than traditional stitching, while advanced printing techniques enable 98% color accuracy for brand differentiation.
Introduction: The Dual Strengths of Poly-BOPP Bags
Poly-BOPP bags, renowned for their moisture resistance, tensile strength, and printability, are reshaping packaging across agriculture, retail, and logistics. Their hybrid structure—combining woven PP layers with BOPP lamination—ensures durability while accommodating high-definition branding. For instance, Shandong GreenPack reported a 25% increase in client retention after adopting digitally printed BOPP bags for organic fertilizer packaging. This report dissects critical manufacturing choices—from sealing methods to closure designs—that define their performance.
Industry Expert Insight:
“The future of packaging lies in marrying aesthetics with engineering. Poly-BOPP bags are a canvas for innovation, whether through RFID-integrated valve designs or AI-driven printing systems.” — 2025 Global Packaging Trends Report.
Critical Manufacturing Choices: Sealing and Closure Technologies
1. Sealing Methods: Ultrasonic Welding vs. Heat Sealing vs. Stitching
- Ultrasonic Welding:
- Speed: Achieves 50–70 seals/minute, 40% faster than heat sealing.
- Strength: Creates airtight bonds with 200–250 N/25mm tensile strength, ideal for valve bags in chemical transport.
- Eco-Friendliness: Eliminates adhesives, reducing VOC emissions by 90%. Case Study: Guangdong Huaxing Packaging reduced leakage incidents by 60% after switching to ultrasonic welding for PE-coated BOPP valve bags in construction waste management.
- Heat Sealing:
- Cost-Efficiency: Requires 30% lower initial investment than ultrasonic systems.
- Versatility: Adjustable parameters (temperature: 120–180°C, pressure: 0.2–0.5 MPa) suit diverse BOPP thicknesses.
- Limitations: Struggles with moisture-sensitive films, risking delamination at >85% humidity.
- Stitching:
- Durability: Polyester threads with 8–12 stitches/inch resist abrasion in heavy-duty applications (e.g., 50kg grain bags).
- Drawbacks: 15–20% slower than welding and prone to microbial growth in humid climates.
2. Closure Designs: Functionality and Applications
Closure Type | Key Features | Best For |
---|---|---|
Valve | Airtight PE spout, 1,200 bags/hr | Powders, granules (e.g., cement, flour) |
Block-Bottom | Flat base, 20% higher stackability | Retail packaging, premium products |
Heat-Sealed | Waterproof, <0.01g/24h OTR | Pharmaceuticals, perishable goods |
Stitched | Reusable, 5–8 cycles | Agricultural bulk transport |
Example: Vietnam Rice Exporters reduced spoilage by 22% using heat-sealed BOPP bags with 0.03mm PE liners for moisture-sensitive jasmine rice.
Custom Printing: Techniques and Innovations
1. High-Definition Flexography
- Resolution: 150–200 LPI (lines per inch), achieving Pantone color matching with <2% deviation.
- Cost: $0.03–$0.05/bag for 10,000-unit orders.
2. Digital UV Printing
- Advantages: Supports complex gradients and QR codes for traceability.
- Speed: 1,200 bags/hour with LED curing, 50% faster than solvent-based inks.
Case Study: Nestlé’s limited-edition coffee bags using digital UV prints saw a 30% sales boost due to enhanced shelf appeal.
FAQs: Addressing Client Concerns
Q: How to choose between valve and stitched closures for bulk chemicals?
A: Valve bags with ultrasonic seals prevent leaks and dust, while stitched designs suit coarse materials like mining ore. For hazardous chemicals, opt for laminated BOPP with PE-coated valves.
Q: Can Poly-BOPP bags withstand freezer temperatures?
A: Yes. Heat-sealed bags with −40°C ratings maintain integrity, ideal for frozen seafood. Ensure a 0.08mm BOPP layer and nylon stitching threads.
Future Trends: Smart Packaging Integration
- QR Code Traceability: Zhejiang GreenFarm reduced supply chain errors by 90% using QR-linked BOPP bags for organic produce.
- RFID-Enabled Valve Bags: Pilot projects in EU logistics show 25% faster inventory checks with embedded tags.
- Biodegradable BOPP Blends: Trials with 30% PLA (polylactic acid) aim to cut carbon footprints by 50% by 2027.
Conclusion
Poly-BOPP bags are not just containers—they are strategic tools for brand differentiation and operational efficiency. By selecting advanced sealing methods like ultrasonic welding and embracing smart closure designs, businesses can align with ESG goals while boosting profitability. For deeper insights into valve bag engineering, explore BOPP Valve Bags: Material Innovation in Packaging and Form-Fill-Seal Woven Bags: The Future of Automation.
Data synthesized from the 2025 Global Packaging Trends Report, case studies, and technical specifications from Shandong GreenPack and Guangdong Huaxing Packaging.