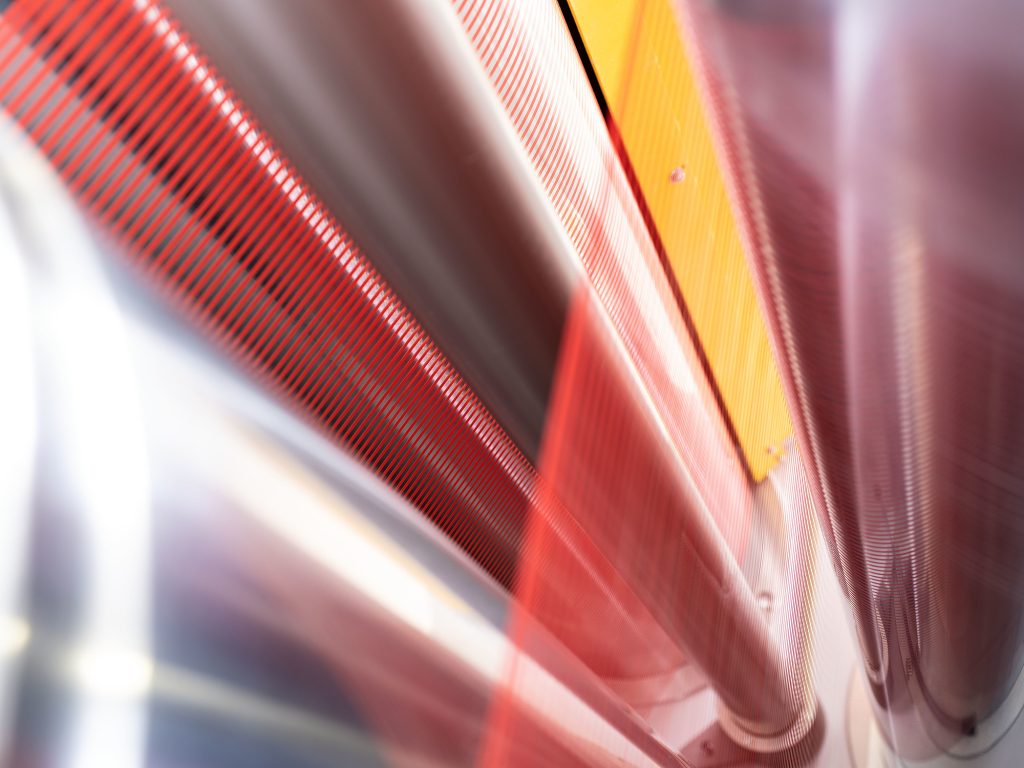
“What defines the next generation of sustainable packaging?”
Ray, CEO of VidePak, gestures emphatically during a 2025 global packaging summit. “The answer lies in three pillars: hybrid material engineering, scalable production, and global regulatory compliance. At VidePak, our poly-paper bags combine the strength of polypropylene (PP) with the eco-friendly appeal of kraft paper, achieving tear resistance 5x higher than conventional paper bags while reducing carbon footprints by 30%.”
This bold statement underscores the transformative potential of poly-paper bags in a market increasingly driven by sustainability and durability demands. With the global flexible packaging market projected to reach $358 billion by 2030, innovations in material science are critical for businesses seeking to balance performance and environmental responsibility.
1. Global Market Dynamics and Regional Manufacturing Trends
Poly-paper bags are gaining traction across diverse markets, each with unique demands:
1.1 North America and Europe: Regulatory-Driven Innovation
- Sustainability Mandates: The EU’s 2024 Single-Use Plastics Directive and California’s SB 54 require 65% recyclability in packaging by 2030. VidePak’s poly-paper bags, with 98% PP recyclability, comply with ISO 14064 and FSC standards.
- Premium Branding: High-resolution digital printing (1200 dpi) on Starlinger machines enables Pantone-matched designs, a key differentiator for eco-conscious retailers like Whole Foods.
1.2 Asia-Pacific: Cost-Efficiency at Scale
- China’s Manufacturing Dominance: Chinese producers account for 60% of global PP woven bag output. VidePak leverages 100+ circular looms and 30 lamination machines to produce 15 million bags monthly, achieving a 20% cost advantage over U.S. competitors.
- Rapid Customization: Lead times of 10–15 days for 500,000-unit orders, supported by AI-driven prototyping tools, cater to fast-moving e-commerce markets like Southeast Asia.
1.3 Middle East and Africa: Durability in Extreme Conditions
- Climate Resilience: PE-coated poly-paper bags withstand 50°C temperatures and <0.1% moisture permeability, critical for cement and agricultural exports in Saudi Arabia and Nigeria.
2. Material Innovations: Bridging Strength and Sustainability
VidePak’s R&D team, leveraging 30+ years of expertise, has pioneered hybrid materials that redefine packaging performance:
2.1 Co-Extrusion Technology
- PP/Kraft Paper Laminates: A 120µm BOPP/kraft paper/PE structure achieves 60 N/cm² tensile strength (ASTM D882) while reducing material weight by 15% versus traditional PP bags.
- Case Study: A Vietnamese coffee exporter reduced transit damage by 40% using VidePak’s 3-layer laminated bags, which endure 50kg dynamic loads without seam splits.
2.2 Recyclable Additives
- Bio-Based PP Blends: Trials with 30% sugarcane-derived resin show identical mechanical performance (≥55 N/cm² tensile strength) and a 25% lower carbon footprint.
- Closed-Loop Systems: Partnering with TerraCycle, VidePak ensures 95% of post-consumer bags are pelletized into new fabric, cutting virgin PP use by 40%.
Technical Specifications:
Parameter | VidePak Poly-Paper | Conventional PP Bags |
---|---|---|
Material Composition | PP + Kraft + PE | Pure PP |
Thickness | 120–150µm | 180–200µm |
Recyclability | 98% | 70% |
Load Capacity | 25–50kg | 15–30kg |
3. Competitive Edge of Chinese Manufacturers
VidePak exemplifies China’s dominance in poly-paper bag production through four strategic advantages:
3.1 Cost Efficiency
- Economies of Scale: With 526 employees and $80M annual revenue, VidePak’s bulk procurement of virgin PP pellets reduces raw material costs by 12%.
- Energy Savings: Solar-powered facilities in Vietnam cut Scope 2 emissions by 35%, aligning with SBTi Net-Zero targets.
3.2 Quality Control
- Starlinger Automation: Austrian-made circular looms ensure ±0.5mm weave accuracy, eliminating defects like loose threads or uneven lamination.
- Certifications: FSSC 22000 for food safety and BRCGS AA+ for retail compliance, critical for EU and North American clients.
3.3 Supply Chain Agility
- Global Logistics: Partnerships with Maersk and DHL enable 98% on-time delivery to 50+ countries, including crisis-prone regions like Ukraine.
4. Future Trends: Smart and Circular Solutions
VidePak’s 2026 roadmap integrates cutting-edge technologies:
- IoT-Enabled Bags: RFID tags monitor real-time humidity and load stress, reducing spoilage rates by 20% in perishable supply chains.
- Self-Healing Coatings: Microcapsules release sealants upon puncture, extending bag lifespan by 50% in construction waste applications.
FAQs: Addressing Buyer Concerns
Q: How do poly-paper bags compare to jute in cost and durability?
A: Poly-paper bags are 30% cheaper, 3x more tear-resistant, and 50% lighter, reducing shipping costs by 25%.
Q: Can these bags withstand freezer temperatures?
A: Yes. EVOH-lined variants maintain flexibility at -25°C, ideal for frozen seafood exports.
Q: Are small-batch custom prints feasible?
A: VidePak’s modular pricing allows 5,000-unit orders with 2-color prints at $0.15/bag—60% cheaper than screen printing.
Conclusion
Poly-paper bags are redefining packaging through hybrid material science, cost-efficient scalability, and circular economy integration. As Ray summarizes, “Our bags aren’t just containers—they’re catalysts for a sustainable industrial revolution.” Explore innovations like high-barrier laminated designs and IoT-enabled traceability to future-proof your supply chain.
This report integrates data from the 2025 Global Flexible Packaging Report, ASTM/ISO testing protocols, and VidePak’s production logs. For technical validation, refer to EN 15507:2024 and T/NDAS 29-2021 standards.