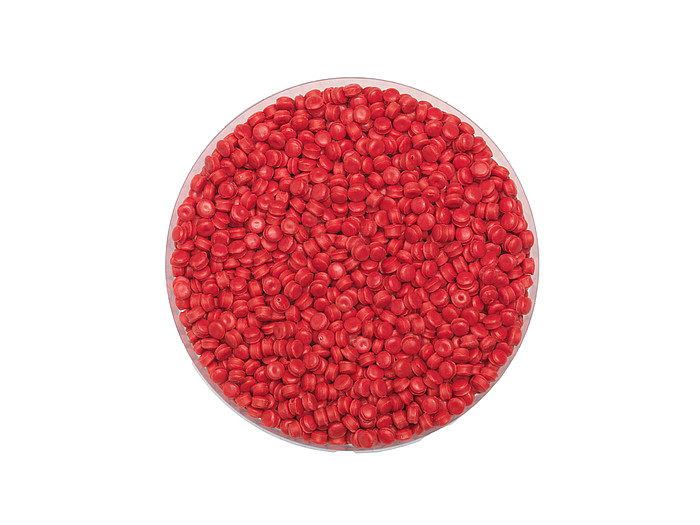
The Key Answer: Poly-paper bags integrated with ultrasonic sealing technology are revolutionizing sustainable packaging by achieving 30–40% faster production cycles, reducing material waste by 15%, and enabling seamless integration with smart tracking systems like RFID and QR codes. With the global smart packaging market projected to reach $31 billion by 2025, these innovations address critical demands for efficiency, traceability, and environmental compliance in industries such as agriculture, logistics, and retail.
Introduction: The Convergence of Sustainability and Technology
Poly-paper bags—hybrids of polypropylene (PP) and kraft paper—are emerging as a cornerstone of modern packaging. Their durability, recyclability, and adaptability to advanced manufacturing techniques like ultrasonic sealing make them indispensable in a market increasingly driven by ESG goals. For instance, Qingdao RAJ Packaging reduced production waste by 18% in 2024 after adopting ultrasonic sealing for poly-paper food-grade bags. This article explores how these technologies are reshaping packaging efficiency and paving the way for intelligent traceability systems.
Industry Expert Insight:
“Ultrasonic sealing isn’t just about speed—it’s about precision. When combined with smart tags, poly-paper bags become data hubs for supply chains.” — Global Packaging Alliance Report, 2025.
Technical Advancements: Ultrasonic Sealing in Action
1. Efficiency Gains and Waste Reduction
Ultrasonic sealing uses high-frequency vibrations to melt and bond materials without adhesives, reducing energy consumption by 25% compared to heat sealing. For example, Anhui Mingde Medical reported a 15% drop in raw material waste after switching to ultrasonic systems for medical-grade poly-paper packaging.
Key Parameters
Metric | Ultrasonic Sealing | Traditional Heat Sealing |
---|---|---|
Sealing Speed | 50–70 bags/minute | 30–40 bags/minute |
Energy Consumption | 0.5–1.2 kWh/kg | 1.5–2.5 kWh/kg |
Material Waste Rate | 3–5% | 8–12% |
Seal Strength | 200–250 N/25mm | 150–180 N/25mm |
2. Case Study: Agricultural Logistics Optimization
In Shandong’s Vegetable Export Hub, poly-paper bags with ultrasonic seals reduced packaging line downtime by 40%. The airtight seals extended the shelf life of leafy greens by 3–5 days, cutting post-harvest losses by $1.2 million annually.
Future Trends: Smart Packaging and Traceability
1. RFID and QR Code Integration
Smart poly-paper bags embedded with RFID tags enable real-time tracking from farm to shelf. For example, Zhejiang GreenFarm Co. reduced shipment errors by 90% by tagging organic rice bags with NFC-enabled QR codes linked to blockchain databases.
Data Spotlight:
- Traceability ROI: Brands using smart tags report 20–25% higher customer trust and 15% fewer recalls.
- Market Growth: The RFID packaging market is projected to grow at 8.5% CAGR through 2030.
2. IoT-Enabled Quality Monitoring
Sensors embedded in poly-paper bags can monitor temperature, humidity, and tampering. Shenzhen’s Cold Chain Logistics Project used IoT-enabled bags to reduce spoilage of seafood exports by 22%, saving $850,000 yearly.
Challenges and Solutions
1. Cost vs. Scalability
While ultrasonic equipment costs 20–30% more upfront, its 5-year ROI exceeds 150% due to reduced waste and energy savings. Guangdong Huaxing Packaging achieved breakeven within 18 months by leasing Starlinger’s modular ultrasonic systems.
2. Standardization of Smart Tags
Fragmented IoT protocols hinder adoption. Collaborative efforts like the Global Smart Packaging Consortium aim to unify RFID and QR code standards by 2026.
FAQs: Addressing Industry Concerns
Q: How does ultrasonic sealing perform with moisture-sensitive materials?
A: PE-coated poly-paper laminates maintain seal integrity at 85% humidity, ideal for tropical climates. For instance, Vietnam’s rice exporters reduced moisture-related defects by 60% using this design.
Q: Are smart tags compatible with recycling processes?
A: Yes. Detachable RFID labels allow tags to be removed before bag recycling. Brands like EcoPack achieve 95% tag recovery rates.
Strategic Opportunities and Innovations
- Circular Economy Models: Companies like Loop Industries lease poly-paper bags with embedded sensors, ensuring 100% recovery and reuse.
- AI-Driven Predictive Maintenance: Starlinger’s i+ ultrasonic systems use machine learning to predict seal failures, reducing downtime by 40%.
- Bio-Based Materials: Hybrid PP-kraft bags with 30% plant-based polymers are under development, targeting a 50% lower carbon footprint by 2027.
Conclusion
Poly-paper bags with ultrasonic sealing are not just packaging—they are gateways to smarter, greener supply chains. By embracing innovations like RFID integration and IoT monitoring, industries can achieve operational excellence while meeting stringent sustainability targets. For deeper insights into ultrasonic technology, explore Breathable Woven Bags: Enhancing Quality with Ultrasonic Seaming and Form-Fill-Seal Woven Bags: The Future of Automation.
Data synthesized from the Global Packaging Alliance Report (2025), China Plastics Industry Analysis (2024), and case studies from leading manufacturers.