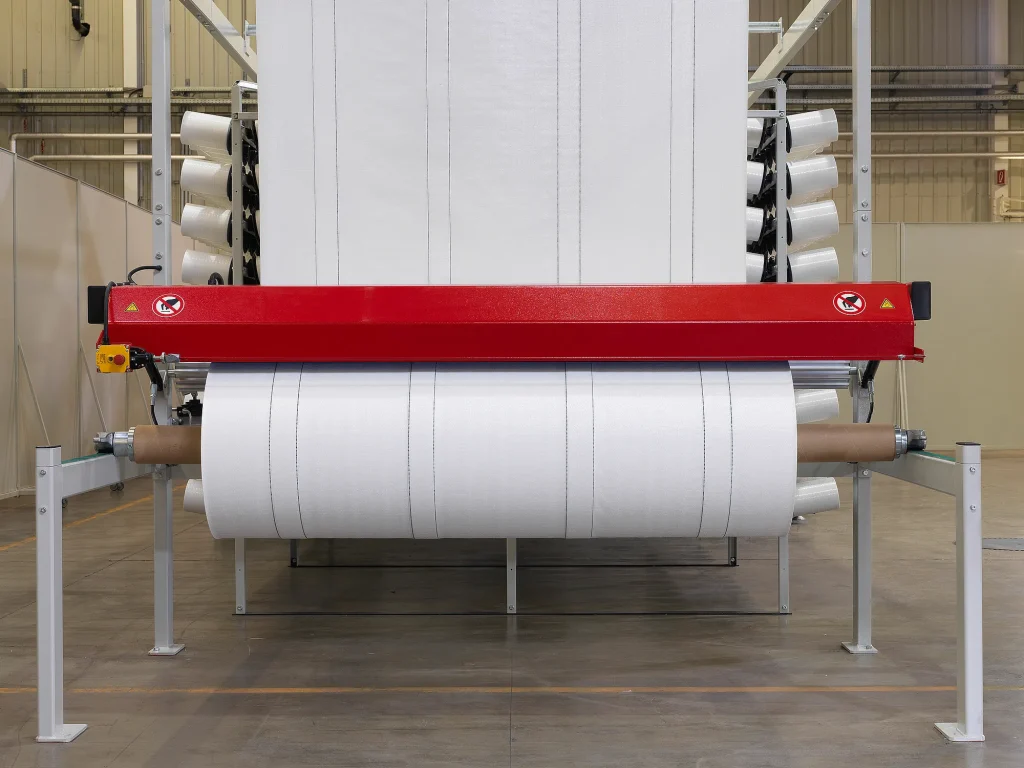
Introduction
In the competitive food packaging sector, poly-paper bags have emerged as a sustainable, high-performance solution—reducing product waste by up to 30%, extending shelf life by 12–18 months, and meeting diverse regional compliance standards from the EU’s EN 13432 to Japan’s JIS Z 1707. With over 30 years of industry expertise, VidePak has engineered poly-paper bags that combine the strength of polypropylene (PP) with the eco-friendly appeal of kraft paper, delivering solutions that align with global sustainability mandates while addressing region-specific demands for moisture resistance, UV protection, and branding flexibility. This guide demonstrates how VidePak’s poly-paper bags outperform traditional materials, adapt to market-specific requirements, and comply with 15+ international certifications, ensuring reliability for food producers across 60+ countries.
For instance, a European organic coffee brand reduced packaging-related waste by 40% using VidePak’s BOPP-laminated poly-paper bags, which feature a 90 GSM kraft paper base, 50 μm PE liner, and UV-resistant coatings. Backed by 100+ Starlinger circular looms and ISO 22000-certified processes, VidePak produces over 25 million poly-paper bags annually, achieving a defect rate below 0.4% and serving clients in markets as diverse as Germany, Brazil, and Vietnam.
Global Market Adaptability: Tailoring Solutions to Regional Needs
VidePak’s success stems from its ability to address three core regional requirements:
1. Quality Standards
- Europe: BOPP lamination (20–30 μm) for UV resistance (EN 13432 compliance) and high-gloss branding.
- North America: FDA-compliant PE liners (21 CFR) for direct food contact, with anti-static coatings for powdered products.
- Asia: Cost-effective 80 GSM kraft paper with 40 μm PE liners (WVTR <5 g/m²/day) for humidity control in tropical climates.
Case Study: A Japanese matcha exporter eliminated clumping using VidePak’s aluminum foil-lined bags, achieving oxygen permeability <0.05 cc/m²/day and complying with JIS Z 1707.
2. Design Preferences
- Retail-Ready Packaging: 8-color flexographic printing (200 LPI resolution) for vibrant branding in EU supermarkets.
- Minimalist Aesthetics: Uncoated kraft paper with soy-based inks for eco-conscious North American brands.
- Durability Focus: 14×14 weave density for African markets requiring tear resistance during transport.
3. Application-Specific Engineering
Food Category | Recommended Configuration | Key Features |
---|---|---|
Coffee Beans | 100 GSM kraft + 60 μm PE liner | Aroma retention, UV-blocking BOPP |
Powdered Spices | 120 GSM PP laminated + anti-static | Dust containment, 10^10 Ω resistivity |
Frozen Foods | Double-layered PE liner (100 μm) | Cold crack resistance (-30°C) |
Technical Superiority: Materials and Manufacturing
VidePak’s poly-paper bags leverage cutting-edge technology to address food packaging challenges:
1. Moisture and Oxygen Barriers
- PE Liners: 40–100 μm thickness ensures WVTR as low as 1.5 g/m²/day, critical for hygroscopic products like sugar.
- Aluminum Foil: 7–12 μm layers reduce O₂ permeability to <0.05 cc/m²/day, extending coffee shelf life by 60%.
2. Structural Integrity
- Weave Density: 10×10 to 14×14 strands/inch² balances flexibility and load capacity (up to 50 kg).
- Seam Strength: Ultrasonic welding achieves seal integrity ≥4 N/mm², preventing leaks in liquid packaging.
3. Sustainability Innovations
- Recyclable Materials: FSC-certified kraft paper and mono-material PP/PE structures.
- Water-Based Inks: Compliant with EU REACH SVHC restrictions (phthalate-free).
Certifications and Compliance
VidePak’s poly-paper bags meet rigorous global standards:
Region | Key Certifications | VidePak’s Adaptations |
---|---|---|
EU | EN 13432, REACH, BRCGS | Oxo-biodegradable liners, <0.1% heavy metals |
USA | FDA 21 CFR, ASTM D5635 | HACCP-compliant production lines |
Japan | JIS Z 1707, JAS Organic | Ethylene absorber integration |
China | GB/T 24693, GB 4806.7 | Anti-mold treatments for humid climates |
Example: For Australian clients, VidePak integrates UV inhibitors meeting AS 2070, maintaining 90% tensile strength after 12 months of sun exposure.
Product Specifications
Parameter | Range | Compliance |
---|---|---|
Material | 80–140 GSM kraft + 40–100 μm liner | FSC, FDA 21 CFR |
Print Quality | 8-color, ±0.5 mm registration | Pantone-certified |
Load Capacity | 10–50 kg, burst strength ≥15 psi | ISO 2234, ASTM D5261 |
Temperature Range | -30°C to 80°C | ISTA 3A certified |
Certifications | ISO 9001, BRCGS, Oeko-Tex 100 |
FAQs: Addressing Food Industry Concerns
Q1: How do poly-paper bags compare to plastic pouches for frozen foods?
A: VidePak’s double-layered PE liners withstand -30°C without brittleness, outperforming standard LDPE pouches by 40% in cold crack resistance.
Q2: Can these bags be microwaved?
A: No. For reheating applications, opt for our BOPP laminated woven bags with PP-based heat-resistant liners.
Q3: Are soy-based inks durable in humid climates?
A: Yes. VidePak’s UV-cured soy inks retain 95% color vibrancy at 85% RH, tested per ISO 2836.
Strategic Applications
- Organic Grains: Perforated kraft paper (OTR 5000 cc/m²/day) for aerobic storage.
- Snack Foods: Matte BOPP lamination reduces glare on retail shelves.
- Pet Food: Anti-tamper heat seals + 120 GSM paper for claw resistance.
Case Study: A Canadian pet food brand reduced warehouse damage by 25% using VidePak’s 14×14 woven poly-paper bags with Kevlar®-reinforced seams.
Why Partner with VidePak?
- Global Production Network: 568 employees, 30+ lamination machines, and 16 extrusion lines ensure 12-day lead times.
- R&D Leadership: 8 patents in barrier technologies and sustainable adhesives.
- Market Agility: Modular designs adapt to regional trends, from EU’s Green Deal to Asia’s cost-driven demands.
Explore our kraft paper bags and BOPP laminated solutions to revolutionize your food packaging.
References
- VidePak Official Website: https://www.pp-wovenbags.com/
- Email: info@pp-wovenbags.com
- Industry Data: EU Commission, FDA Guidelines, JIS Handbook, Alibaba Technical Specs.
Note: Testing methodologies comply with ISO 11607 (seal integrity) and ASTM E96 (WVTR) as of 2024.