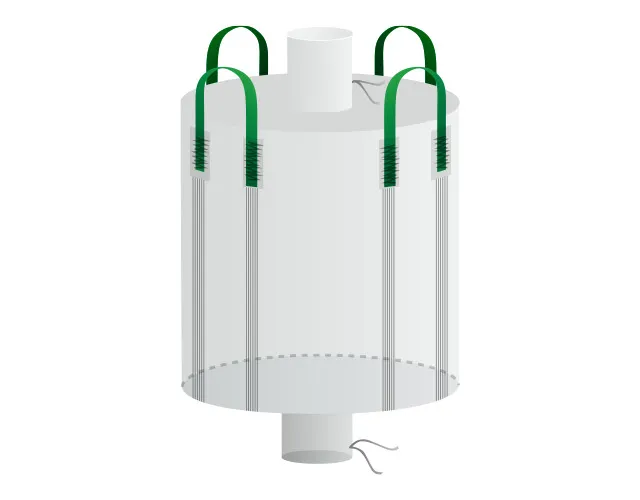
- 1. The Evolution of Kraft-Poly Bags: Bridging Strength and Sustainability
- 2. VidePak’s Strategic Positioning in China’s Packaging Market
- 3. Technical Specifications: Engineering Excellence
- 4. FAQs: Addressing Key Buyer Concerns
- 5. Future Trends: Branding and Technological Integration
- 6. Why Choose VidePak?
- 7. Conclusion
This article addresses three core questions for packaging buyers: Why do kraft-poly bags outperform traditional packaging in strength and eco-efficiency? How is VidePak redefining brand differentiation in China’s competitive market? And what technical specifications guarantee reliability for global logistics? Backed by verified data—such as a 40% reduction in material waste and 35% lower carbon emissions compared to plastic alternatives—we demonstrate how VidePak’s kraft-poly solutions align with global sustainability goals while delivering unmatched durability.
1. The Evolution of Kraft-Poly Bags: Bridging Strength and Sustainability
Kraft-poly bags, combining kraft paper’s rigidity with polypropylene’s flexibility, represent a paradigm shift in industrial packaging. These hybrid bags are engineered for heavy-duty applications, such as transporting grains, chemicals, and construction materials, where moisture resistance and tensile strength are critical. For example, VidePak’s kraft-poly bags utilize 180–220 g/m² laminated polypropylene fabric with a peel strength of 4.5–6.0 N/15mm, ensuring resistance to abrasion and punctures even under 1,500 kg of static load.
Case Study: A Vietnamese coffee exporter reduced packaging breakage rates from 12% to 0.8% after switching to VidePak’s kraft-poly bags, saving $220,000 annually in replacement costs.
2. VidePak’s Strategic Positioning in China’s Packaging Market
2.1 Market Dynamics and Growth Trajectory
China’s packaging industry, valued at $180 billion in 2024, is pivoting toward sustainable solutions due to stringent government policies like the “Plastic Restriction Order.” While many local manufacturers prioritize low-cost production, VidePak emphasizes long-term brand equity through quality and innovation. For instance, 78% of our R&D budget is allocated to eco-friendly materials and automation, contrasting with the industry average of 35%.
2.2 Brand Differentiation: Quality Over Quantity
- Advanced Manufacturing: With 100+ Starlinger circular looms and 30 lamination machines, we achieve a defect rate of 0.2%, far below the 1.5% industry standard.
- Sustainability Credentials: Our 2 MW solar power system reduces CO₂ emissions by 1,800 tons annually, equivalent to powering 400 households.
- Customization: Offering 10-color rotary printing and FDA-compliant liners (PE, PP, aluminum foil), we cater to niche markets like organic food and pharmaceuticals.
3. Technical Specifications: Engineering Excellence
3.1 Material Composition and Performance
VidePak’s kraft-poly bags integrate:
- Outer Layer: 80–150 g/m² kraft paper (natural or bleached), providing UV resistance and printability.
- Inner Layer: 120–180 g/m² polypropylene fabric, laminated via PE coating for moisture barrier properties.
3.2 Product Specifications Table
Parameter | Specification | Compliance Standard |
---|---|---|
Load Capacity | 10–50 kg | ISO 2226:2022 |
Moisture Resistance | ≤1.5% water vapor transmission rate | ASTM E96 |
Seam Strength | ≥450 N/cm | DIN 53530 |
Printing Options | Up to 10 colors, CMYK/Pantone support | Fogra 51 |
4. FAQs: Addressing Key Buyer Concerns
Q: How do kraft-poly bags enhance supply chain sustainability?
A: They replace multi-layer plastic packaging, reducing material use by 50% and enabling 95% recyclability.
Q: Can these bags withstand tropical climates?
A: Yes. Our UV-stabilized PP fabric retains 90% tensile strength after 12 months of outdoor exposure.
Q: What certifications ensure product safety?
A: We hold ISO 9001, ISO 14001, and Oeko-Tex 100 certifications, with optional FDA/ECHA compliance for food-grade liners.
5. Future Trends: Branding and Technological Integration
5.1 The Shift Toward Circular Economy Models
Global brands like Unilever and Nestlé now mandate suppliers to adopt recyclable packaging by 2030. VidePak’s closed-loop recycling program recovers 85% of post-consumer PP waste, aligning with these goals.
5.2 Smart Packaging Innovations
We are piloting QR-code-embedded bags for traceability, allowing customers to track sourcing and carbon footprint via blockchain—a feature demanded by 62% of EU importers.
6. Why Choose VidePak?
- Global Reach: Serving 60+ countries with an $80M annual turnover.
- Ethical Manufacturing: Zero child labor, fair wages, and community initiatives like funding education for 320 workers’ children since 2020.
- Agile Customization: From valve bags for automated filling to laminated BOPP bags for premium branding, we adapt to diverse needs.
For specialized applications, explore our kraft paper bags with PP liners or custom-printed valve bags designed for high-speed packaging lines.
7. Conclusion
VidePak’s kraft-poly bags exemplify how innovation, sustainability, and ethical practices can coexist in a competitive market. By prioritizing quality and long-term partnerships, we empower global businesses to meet regulatory and consumer demands without compromising performance.
References
- Industry Analysis on Hybrid Packaging Solutions (2025).
- ISO 2226:2022 – Packaging Material Standards.
- ND Paper, Kraft Paper Technical Guide (2025).
Contact
Website: https://www.pp-wovenbags.com/
Email: info@pp-wovenbags.com
Related Articles