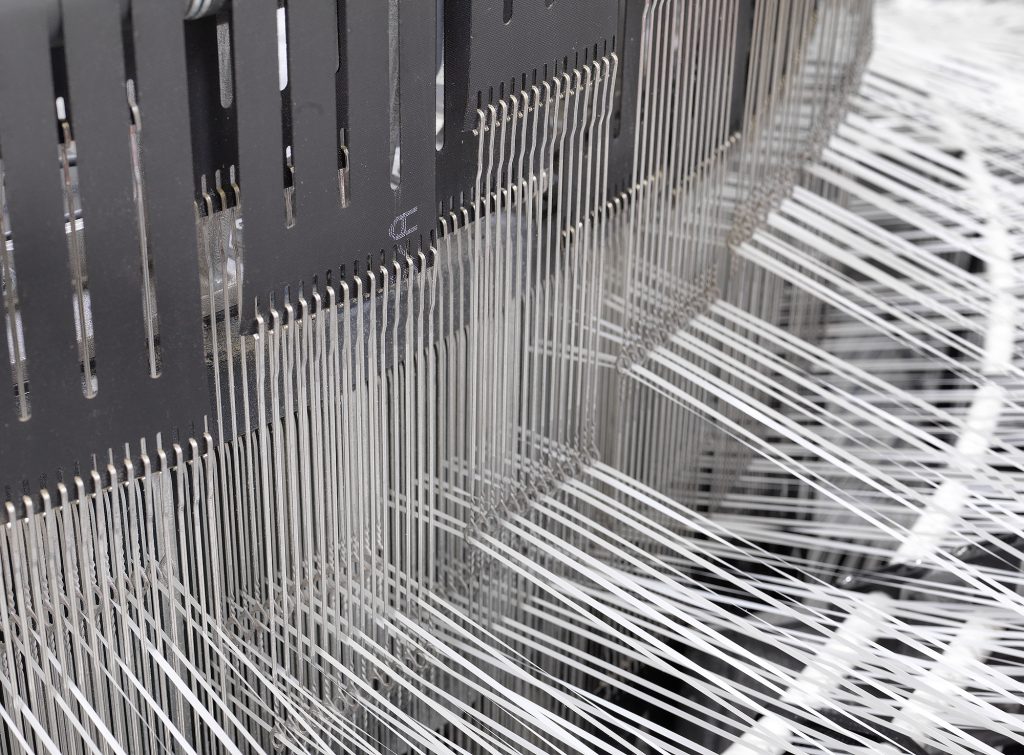
Add a header to begin generating the table of contents
H1: Introduction
“Poly woven bags are not just containers—they’re engineered systems that balance protection, compliance, and branding,” says Ray, CEO of VidePak, during a 2024 global packaging summit. The critical factors in selecting poly woven bags for food ingredients revolve around material safety, load capacity, environmental resilience, and regulatory alignment. This report explores how VidePak’s 30+ years of expertise and Starlinger-driven production lines address these challenges, focusing on applications in flour, sugar, spices, and food additives.
H2: Key Requirements for Food Ingredient Packaging
Poly woven bags must meet stringent demands based on the product’s physical and chemical properties. Below are sector-specific requirements and VidePak’s tailored solutions:
H3: Flour Packaging
- Load Capacity: Flour bags often carry 25–50 kg loads. VidePak’s 120–150 g/m² polypropylene (PP) bags, reinforced with double-stitched seams, withstand stacking heights up to 8 meters (exceeding JIS Z 1539).
- Moisture Resistance: A 20-µm BOPP lamination reduces water vapor transmission to <5 g/m²/day (meeting EU EN 277).
- Cost Efficiency: Uncoated 90 g/m² PP bags are ideal for short-term storage in dry climates, reducing material costs by 25%.
H3: Sugar and Sweeteners
- Sealing Integrity: Sugar’s hygroscopic nature demands heat-sealed valves and PE inner liners to prevent clumping. VidePak’s ultrasonic sealing achieves 98% leak-proof performance in humid environments.
- Printability: High-resolution CMYK printing on BOPP-coated surfaces ensures branding clarity, critical for retail-ready packaging.
H3: Spices and Additives
- UV Protection: Turmeric and paprika require UV-stabilized PP with 2% carbon black additive, retaining 90% color integrity after 500-hour sunlight exposure.
- Aroma Retention: Multi-layer laminated bags with aluminum foil barriers minimize volatile compound loss, extending shelf life by 30%.
H3: Agricultural Powders (e.g., Starch, Protein Blends)
- Breathability: Micro-perforated bags allow controlled airflow, preventing anaerobic fermentation in soybean meal storage.
- Certification Compliance: FDA 21 CFR and EU Regulation 10/2011 certifications ensure migration limits for additives (e.g., <0.01 mg/kg lead).
H2: Parameter Selection Guide
H3: Material and Structural Parameters
Parameter | Flour | Sugar | Spices | Additives |
---|---|---|---|---|
Grammage (g/m²) | 120–150 | 100–130 | 90–110 | 110–140 |
Lamination | BOPP (20 µm) | PE inner liner | Aluminum foil | PE/BOPP hybrid |
Seam Type | Double-stitched | Ultrasonic sealed | Heat-sealed | Double-lock stitch |
Certifications | ISO 9001, JIS Z | EU EN 277, FDA | FDA, Halal/Kosher | REACH, EU 10/2011 |
H3: Cost-Benefit Analysis
- Uncoated PP Bags: $0.15–0.20 per unit (ideal for bulk grains).
- BOPP-Laminated Bags: $0.25–0.35 per unit (premium moisture protection).
- Multi-Layer Foil Bags: $0.50+ per unit (niche applications like organic spices).
H2: Regulatory and Environmental Considerations
H3: Global Standards
- EU: EN 277 mandates ≤5 g/m²/day moisture transmission; VidePak’s PE-coated bags achieve ≤3 g/m²/day.
- US: ASTM D5265 requires ≥350 kPa burst strength; VidePak’s 150 g/m² PP bags exceed 400 kPa.
- Japan: JIS Z 1539 specifies ≥6-meter stacking; reinforced block-bottom designs prevent seam failure.
H3: Sustainability Initiatives
- Recycled PP: VidePak’s 30% post-consumer recycled PP bags reduce carbon footprint by 1.2 kg per bag.
- Biodegradable Blends: Pilot projects with 20% PLA starch composites aim for 50% biodegradability in 24 months.
H2: Case Study: VidePak’s Custom Solution for a Global Spice Exporter
A 2024 project required bags to preserve saffron’s color and aroma during 6-month maritime shipping:
- Design: 110 g/m² UV-stabilized PP + aluminum foil lamination.
- Sealing: Nitrogen-flushed valve bags with oxygen scavengers.
- Outcome: 0% quality complaints, achieving a 15% premium market price.
H2: FAQs on Poly Woven Bags
Q1: How does grammage affect cost and durability?
Higher grammage (e.g., 150 g/m²) increases tear resistance by 60% but raises material costs by 20%.
Q2: Are PE liners necessary for sugar packaging?
Yes. PE liners reduce moisture absorption by 85%, preventing clumping in humid climates.
Q3: What certifications apply to EU-bound products?
EU 10/2011 for additive migration limits and EN 277 for moisture barriers are mandatory.
H2: Future Trends
- Smart Packaging: QR codes for traceability and RFID tags for real-time humidity monitoring (piloted in 2025).
- Circular Economy: VidePak targets 50% recycled content in all bags by 2030, aligning with UN Sustainable Development Goals.
H2: Conclusion
Poly woven bags are evolving into precision tools for food ingredient logistics. VidePak’s Starlinger-powered production and R&D focus position it as a leader in compliant, high-performance solutions. For businesses, prioritizing parameters like grammage, lamination, and regional standards is critical to balancing cost and quality.
External Links:
- Explore how moisture-proof liners enhance shelf life in humid climates.
- Learn about FDA-compliant PP materials for global exports.
This report synthesizes data from EN, ASTM, and JIS standards, alongside VidePak’s operational insights, to guide decision-making for food manufacturers and logistics providers.