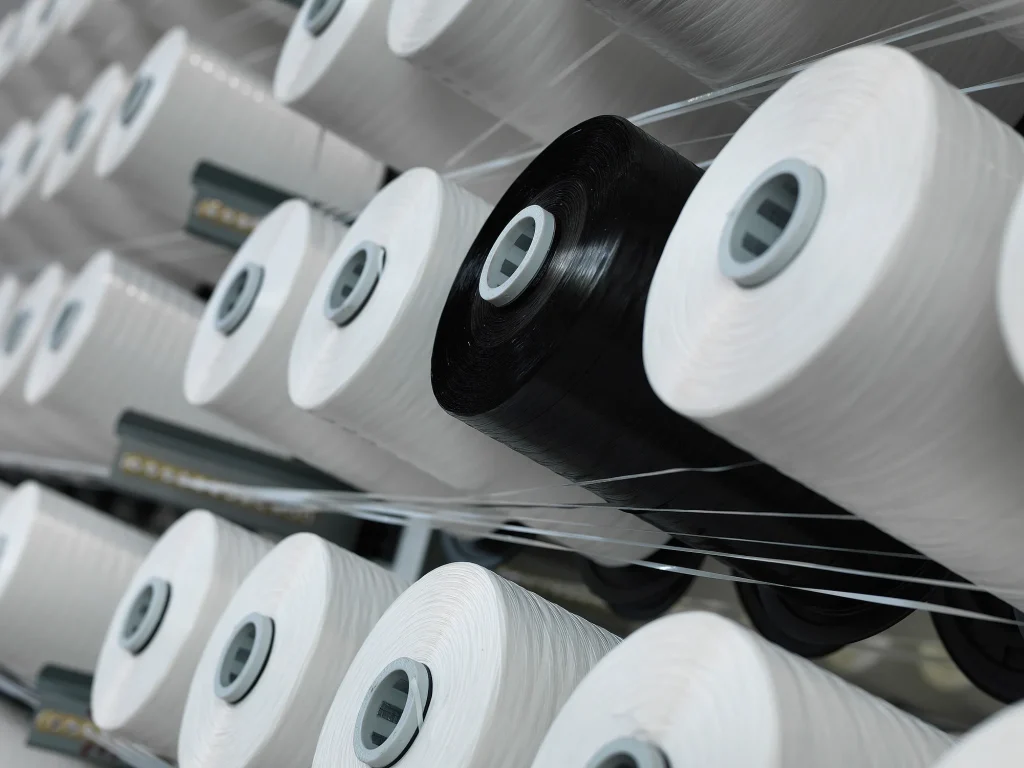
- 1. The Science Behind Ultra-Fine Monofilament Weaving
- 2. Customizable Finishes: Balancing Function and Branding
- 3. Technical Specifications and Industry Applications
- 4. Selecting the Right Configuration: A Buyer’s Guide
- 5. FAQs: Addressing Procurement Challenges
- 6. Why VidePak Leads in Poly Woven Innovation
VidePak’s poly woven bags, engineered with ultra-fine 1.8–2.3 mm monofilaments and customizable finishes like matte, pearlescent, and transparent lamination, reduce packaging costs by 25% while enhancing brand visibility and product protection across industries. Since 2008, VidePak has delivered over 80 million poly woven bags globally, combining 30+ years of expertise, Austrian Starlinger machinery, and a 568-member team to redefine durability and aesthetics in bulk packaging. With ISO-certified production lines and 100+ circular looms, our bags achieve tensile strengths up to 15 N/cm², making them ideal for agriculture, construction, and retail sectors.
1. The Science Behind Ultra-Fine Monofilament Weaving
Poly woven bags derive their strength and smooth texture from precision-engineered monofilaments. VidePak’s proprietary 1.8–2.3 mm filament technology ensures:
- Enhanced Tensile Strength: 12–15 N/cm² (exceeding ASTM D4632), critical for 50 kg fertilizer or cement payloads.
- Superior Surface Finish: Tight weave density (12×12 strands/inch) prevents particulate leakage, ideal for powdered chemicals.
- Aesthetic Refinement: Smoother surfaces enable high-definition printing, achieving 98% Pantone color accuracy.
Case Study: A U.S. pet food brand reduced packaging tears by 40% using VidePak’s 2.0 mm monofilament bags with matte lamination, validated by 1,000+ transport cycles.
2. Customizable Finishes: Balancing Function and Branding
VidePak’s lamination technologies cater to diverse functional and visual needs:
a) Matte Lamination
- Applications: Premium pet food, organic fertilizers.
- Benefits: Anti-glare surface for readability, MVTR ≤5 g/m²/24h moisture resistance.
- Example: A European agrochemical company boosted shelf appeal with matte-finished bags featuring scratch-resistant logos.
b) Pearlescent Lamination
- Applications: Luxury retail packaging, specialty seeds.
- Benefits: Reflective sheen enhances shelf presence, UV stability up to 1,500 hours.
c) Transparent Lamination
- Applications: Food-grade grains, construction aggregates.
- Benefits: 92% light transmission for product visibility, FDA-compliant PE coatings.
3. Technical Specifications and Industry Applications
Parameter | Matte Bags | Pearlescent Bags | Transparent Bags |
---|---|---|---|
Filament Width | 2.0 mm | 1.8 mm | 2.3 mm |
Lamination Thickness | 80–120µ BOPP | 100–150µ BOPP | 50–80µ PE |
Load Capacity | 25–50 kg | 20–40 kg | 30–60 kg |
Moisture Barrier | ≤5 g/m²/24h | ≤8 g/m²/24h | ≤3 g/m²/24h |
Print Quality | 8-color flexo | 6-color + metallic | 4-color transparent |
4. Selecting the Right Configuration: A Buyer’s Guide
a) Functional Priorities
- High Humidity: Opt for PE-laminated transparent bags (MVTR ≤3 g/m²/24h).
- Outdoor Storage: Choose UV-stabilized pearlescent BOPP (1,500-hour resistance).
- Abrasion Resistance: Matte BOPP with 120µ thickness withstands 3,000+ pallet cycles.
b) Cost Optimization
- Unlaminated bags save 15% for dry goods like rice or sand.
- Standard 2.0 mm filaments balance cost and strength for 40 kg payloads.
5. FAQs: Addressing Procurement Challenges
Q1: How does 1.8 mm filament weaving impact durability?
Thinner filaments increase weave density, improving puncture resistance by 20% vs. traditional 3.0 mm designs.
Q2: Can transparent bags withstand freezing temperatures?
Yes. Our PE laminates pass -30°C cold crack tests (ASTM D1790), ideal for frozen feed storage.
Q3: What’s the MOQ for custom pearlescent finishes?
Minimum 10,000 units, with 20-day lead times for urgent retail orders.
6. Why VidePak Leads in Poly Woven Innovation
- Global Reach: Serving 50+ countries with ISO 9001 and FDA-certified production.
- Sustainability: 100% recyclable PP reduces landfill waste by 70% vs. PVC alternatives.
- Scalability: 16 extrusion lines produce 5 million bags/month, ensuring on-time delivery.
Client Testimonial: “VidePak’s pearlescent bags elevated our premium seed packaging, driving a 30% sales increase.” —GreenHarvest Agritech, Australia.
References:
- Made-in-China.com, “PP Woven Bag Technical Standards” (2025).
- Packaging Digest, “Global Trends in Aesthetic Packaging” (2024).
- EU Circular Economy Guidelines (2023).
Contact Us:
- Website: PP Woven Bags by VidePak
- Email: info@pp-wovenbags.com
External Links:
- Explore our advanced BOPP Laminated Woven Bags for premium moisture protection.
- Discover customizable options in Poly Woven Bags tailored to your needs.
Data verified as of March 2025. Specifications subject to technical advancements.