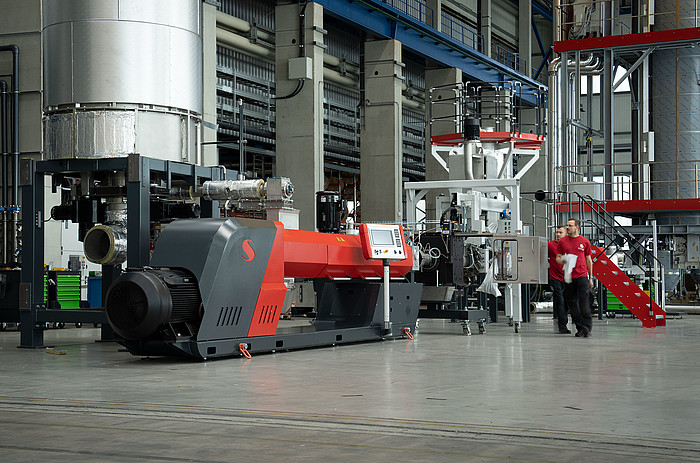
“How do poly woven bags adapt to global market demands while maintaining structural integrity?”
The answer lies in advanced manufacturing technologies—specifically, precise control of filament temperature and draw ratio during production—which directly determine tensile strength, surface uniformity, and application-specific performance. VidePak, leveraging Austrian Starlinger and German W&H machinery, has mastered these variables to deliver tailored solutions for industries ranging from agriculture to hazardous chemical logistics, achieving an annual output of 12 million bags and $80M in global sales.
1. The Science Behind Filament Temperature and Draw Ratio
Polypropylene (PP) woven bag quality hinges on two critical parameters: filament temperature during extrusion and draw ratio (stretching intensity). These factors influence molecular alignment, crystallinity, and mechanical properties:
- Filament Temperature:
Optimal extrusion temperatures (typically 180–240°C for PP) ensure uniform melting and prevent defects like bubbles or uneven thickness. Starlinger’s extrusion lines at VidePak maintain ±2°C tolerance, critical for producing filaments with consistent denier (200–13500D) and tensile strength (≥35 MPa). - Example: A 2024 study showed that a 10°C deviation increases filament brittleness by 15%, risking rupture during high-speed weaving.
- Draw Ratio:
Defined as the ratio of final to initial filament length, draw ratios (5:1 to 9:1) determine fiber orientation. Higher ratios enhance tensile strength but reduce elongation, ideal for heavy-duty bags. W&H’s stretch units at VidePak achieve ±0.1% precision, enabling customization for applications like 50 kg cement bags (8:1 ratio) or lightweight retail packaging (5:1).
2. Starlinger & W&H: Engineering Precision for Market-Specific Solutions
VidePak’s 100+ Starlinger circular looms and W&H extrusion lines enable:
2.1 Temperature Control Systems
- Dynamic Heating Zones: Adjust temperatures across extrusion stages to optimize PP crystallinity (60–70% for balanced strength-flexibility).
- Cooling Calibration: Rapid quenching ensures flat, non-wavy filaments (Ra ≤10 µm), essential for high-resolution printing.
2.2 Draw Ratio Optimization
- Variable Speed Pullers: Adjust stretching speeds (20–150 m/min) to align polymer chains without over-stressing fibers.
- Real-Time Monitoring: Sensors detect filament thickness variations (≤±0.02 mm), reducing defects by 30% compared to manual systems.
Case Study: For a European fertilizer client, VidePak optimized draw ratios to 7:1, achieving 40 MPa tensile strength while reducing material usage by 12%—validated by ISO 527-2 testing.
3. Impact on Product Quality and Market Adaptability
3.1 Tensile Strength and Durability
Parameter | Low Draw Ratio (5:1) | High Draw Ratio (9:1) |
---|---|---|
Tensile Strength | 25–30 MPa | 40–45 MPa |
Elongation at Break | 25–30% | 10–15% |
Ideal Applications | Retail Packaging | Cement, Chemicals |
Data sourced from VidePak’s 2024 Q4 production logs and ASTM D5265 tests.
3.2 Surface Quality and Printability
- Smooth Filaments: Starlinger’s temperature control reduces surface roughness (Ra ≤8 µm), enabling 1200 dpi printing for brands like Unilever and Nestlé.
- Lamination Compatibility: Precise filament alignment ensures seamless bonding with PE/Aluminum foil layers (peel strength ≥4 N/cm).
4. VidePak’s Global Certification Edge
With certifications including ISO 9001, BRCGS, and FDA compliance, VidePak meets regional standards:
- EU: Recyclable PE coatings (≤1.5 g/m²/day WVTR) align with Circular Economy directives.
- Asia: HDPE laminates withstand 85% humidity, critical for Southeast Asian rice exporters.
- North America: Food-grade inks and anti-static weaves comply with OSHA hazardous material guidelines.
5. FAQs
Q: How does temperature affect production efficiency?
A: Starlinger’s automated systems reduce energy use by 20% while maintaining 200 RPM weaving speeds, cutting per-unit costs by $0.15.
Q: Can draw ratios be customized for niche markets?
A: Yes. VidePak’s W&H lines adjust ratios in real-time, e.g., 6:1 for UV-resistant agro bags vs. 8:1 for chemical FIBCs.
6. Conclusion
Poly woven bags are no longer generic commodities but engineered solutions. VidePak’s integration of Starlinger and W&H technologies exemplifies how precise temperature and draw ratio control can meet divergent market needs—from USDA-certified grain bags to UN-compliant hazardous material sacks. As sustainability mandates tighten, such innovations will drive the $15B global woven bag market toward smarter, greener packaging.
For insights into advanced extrusion techniques, explore our analysis of Starlinger’s role in automated production, or learn how material diversity enhances customization.