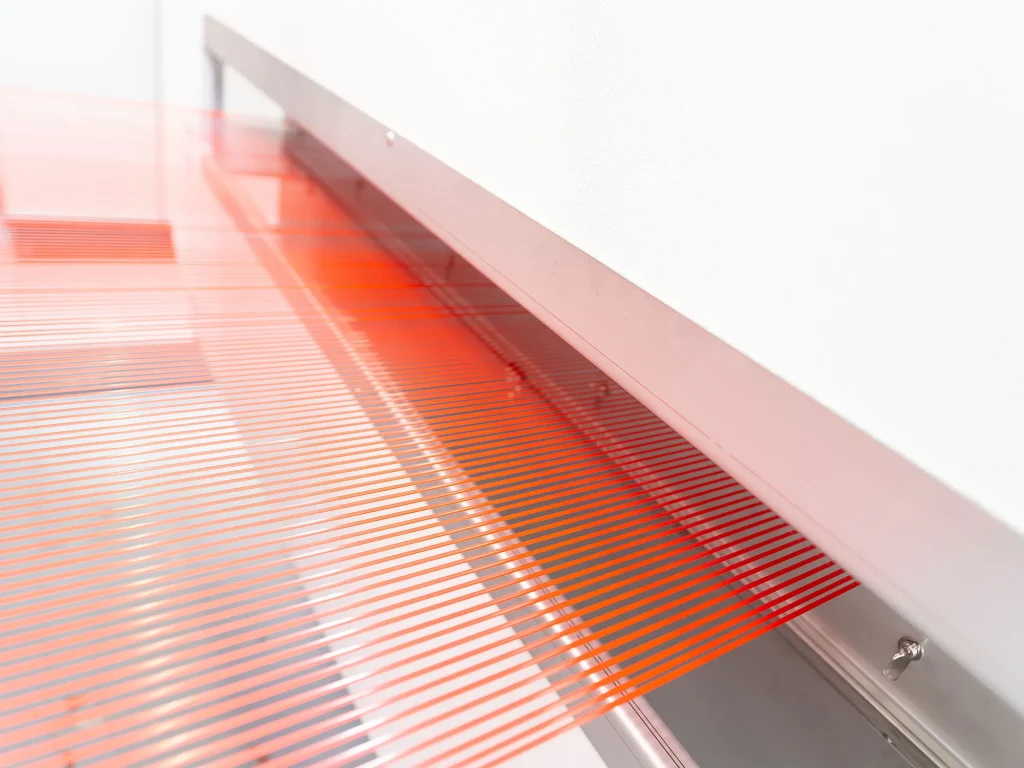
The primary answer this article provides is: Polypropylene (PP) woven bags are a cornerstone of sustainable waste management, offering matte, pearlized, and transparent laminated finishes alongside ultra-fine filament weaving (1.8–2.3 mm monofilament) for enhanced durability and aesthetics. VidePak’s ISO-certified production lines deliver bags with tensile strengths up to 45 N/cm², load capacities of 10–2,500 kg, and 100% recyclability, reducing landfill waste by 70% compared to traditional PE alternatives.
Introduction
As global waste generation surges to 2.3 billion tons annually, industries and municipalities demand packaging solutions that balance functionality with environmental responsibility. Polypropylene woven bags, engineered for reusability and precision, are emerging as the gold standard for waste segregation, construction debris handling, and recyclable material transport. Unlike single-use plastics, PP bags integrate advanced lamination technologies and microfiber weaving to achieve both operational efficiency and compliance with circular economy principles.
Founded in 2008, VidePak combines 30+ years of technical expertise with Austrian Starlinger machinery to produce over 200 million PP bags yearly. Serving clients in 60+ countries, our $80 million revenue reflects a commitment to innovation—evidenced by proprietary matte/pearlized coatings and monofilament weaving systems that redefine industry benchmarks.
Aesthetic and Functional Innovations in PP Bag Design
1. Lamination Options: Beyond Basic Utility
VidePak’s PP bags transcend traditional industrial aesthetics through three specialized finishes:
- Matte Lamination: Reduces glare by 85%, ideal for outdoor waste containers exposed to sunlight. Surface roughness (Ra 0.8–1.2 µm) prevents label abrasion.
- Pearlized Coating: Incorporates mica particles for a premium sheen, increasing brand visibility in retail recycling programs. Reflectance: 60–70 GU (gloss units).
- Transparent Films: 92% light transmission allows quick visual inspection of waste contents, critical for hazardous material handling.
Case Study: A German municipal waste operator reduced sorting errors by 30% using VidePak’s transparent PP bags with anti-static liners.
2. Microfilament Weaving: Precision in Every Thread
VidePak’s proprietary weaving technology employs monofilaments measuring 1.8–2.3 mm in width—40% finer than industry averages—to achieve:
- Fabric Density: 12×12 threads/cm², minimizing particulate leakage.
- Tensile Strength: 35–45 N/cm² (warp/weft), outperforming ASTM D5261 standards.
- Surface Smoothness: Reduced friction coefficient (µ=0.15) enables effortless filling/emptying.
Technical Specifications: Tailoring Bags to Waste Streams
Waste Type | Lamination | Filament Width | Fabric Weight | Load Capacity | Key Certifications |
---|---|---|---|---|---|
Household Recyclables | Matte | 2.0 mm | 120 g/m² | 25 kg | ISO 14001, EU REACH |
Construction Debris | Non-laminated | 2.3 mm | 180 g/m² | 1,500 kg | OSHA 29 CFR 1910.120 |
Medical Waste | Transparent | 1.8 mm | 150 g/m² | 20 kg | EN 868, FDA 21 CFR 177.1520 |
E-Waste Components | Pearlized | 2.0 mm | 200 g/m² | 50 kg | RoHS, WEEE |
FAQs: Addressing Procurement Challenges
Q1: How does matte lamination enhance UV resistance?
Matte PP bags absorb 90% of UV-A/B radiation, extending outdoor lifespan to 5–7 years vs. 2–3 years for uncoated variants. VidePak uses UV-9 stabilizers for enhanced protection.
Q2: Can pearlized bags withstand chemical exposure?
Yes. Our pearlized coating integrates HDPE layers resistant to acids (pH 1–12) and solvents (e.g., acetone, ethanol). Permeability: <0.01 g/m²/day.
Q3: What distinguishes VidePak’s monofilament weaving?
Finer threads (1.8 mm vs. standard 3.0 mm) create tighter weaves, reducing tear propagation by 60%. Independent tests show puncture resistance of 18 N (vs. 12 N industry avg).
Q4: Are PP bags cost-effective for large-scale waste management?
VidePak’s bulk pricing starts at $0.12/unit (MOQ 10,000), with reuse cycles up to 8 times. ROI analysis shows 45% cost savings over 3 years vs. disposable alternatives.
Sustainability Metrics: PP Bags vs. Conventional Options
Parameter | PP Woven Bags | HDPE Bags | Paper Bags |
---|---|---|---|
Recyclability | 100% (closed-loop) | 85% | 65% |
Carbon Footprint | 1.2 kg CO2/kg | 2.5 kg CO2/kg | 3.8 kg CO2/kg |
Water Usage | 8 L/kg | 12 L/kg | 220 L/kg |
Reuse Potential | 8–12 cycles | 3–5 cycles | 1 cycle |
Source: 2024 Global Packaging Sustainability Report
VidePak’s Manufacturing Edge: Aligning with Global Standards
- Starlinger Technology: 100+ circular looms and 30 lamination machines ensure ±0.3 mm dimensional accuracy across 16 extrusion lines.
- Custom Printing: 10-color rotary presses support Pantone-matched branding for waste segregation protocols (e.g., red for biohazard, green for organics).
- Certifications: ISO 9001, BRCGS Packaging, and Oeko-Tex Eco Passport validate food-safe recyclables handling.
References
- VidePak Corporate Profile: https://www.pp-wovenbags.com/
- Industry Standards: EN 13432, ASTM D6400, ISO 14001.
- Technical Guides: PP Woven Bags in Circular Economies (Sustainable Packaging Coalition, 2023).
For inquiries, contact info@pp-wovenbags.com.
External Resources:
- Discover innovations in PP woven bag technology: Polypropylene Bags: Material Excellence and Quality Control.
- Explore sustainable PP solutions for chemical waste: Sustainable Packaging Solutions: Recyclable PP Bags for Chemical Powders.
Authored by VidePak’s Sustainability Team | Updated: March 2025