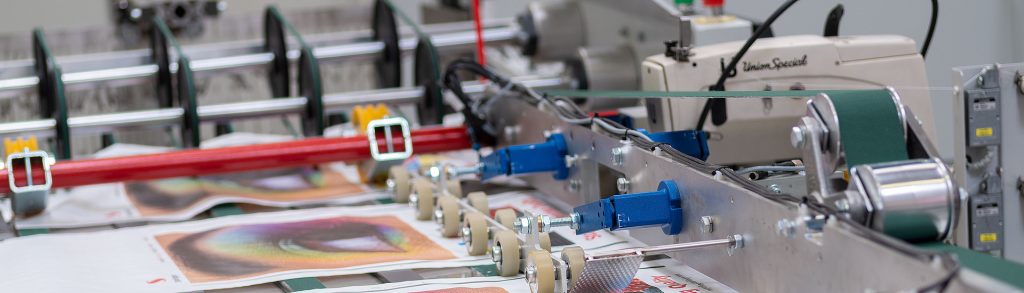
Introduction
The global PP woven bags market is projected to grow at a CAGR of 5.2% through 2030, driven by advancements in printing technologies and their critical role in packaging fertilizers, chemicals, and industrial materials. A key challenge lies in balancing durability, regulatory compliance, and functional design—especially for hygroscopic and corrosive products like fertilizers. This report explores how PP bags address these demands through customizable printing, material innovations, and compliance-driven parameter selection, while aligning with international standards such as ASTM (US), EN (EU), and GB/T (China).
Fertilizer Packaging: Challenges and PP Bag Solutions
Fertilizers—particularly nitrogen-based and compound varieties—require packaging that combats moisture absorption, heat buildup, and chemical reactivity. PP woven bags, with layered structures and specialized coatings, offer tailored solutions:
- Moisture Resistance
- Problem: Ammonium nitrate absorbs moisture, leading to caking and reduced efficacy.
- Solution: BOPP-laminated bags reduce water vapor transmission by 60% compared to uncoated PP.
- Case Study: Shandong Leihua’s 50kg urea bags integrate 25μm PE inner liners, achieving <1% moisture ingress even at 85% humidity.
- Heat Dissipation
- Problem: Exothermic reactions in compound fertilizers risk combustion.
- Solution: Breathable PP fabrics with 30–50 mbar air permeability (ISO 5636-5) allow controlled gas exchange.
- Corrosion Resistance
- Additives: UV stabilizers (e.g., UV-326) and antioxidants (e.g., Irganox 1010) extend bag lifespan by 40% in acidic environments.
Global Standards and Parameter Selection
Q: How do regional standards dictate PP bag specifications?
A: Compliance governs thickness, seam strength, and barrier properties. Below is a comparative analysis:
Standard | Key Requirements | PP Bag Parameters |
---|---|---|
ASTM D5276 (US) | Drop-test resistance ≥1.5m, UV stability | Thickness: 90–100 g/m²; PE-coated seams |
EN 13590 (EU) | REACH-compliant additives, azo-free dyes | Inner liner: 20μm PE; Oeko-Tex® certified |
GB/T 8946 (CN) | Tensile strength ≥5.0 kN/m | Double-stitched seams; anti-UV lamination |
JIS Z 1539 (JP) | High-clarity printing, recyclability | Water-based inks; 80–90 g/m² thickness |
Example: Vedhaa Polypack uses copolymer PP with 25% calcium carbonate filler to meet EN 13590’s tear resistance standards while reducing costs by 15%.
Customization Based on Content
Dialogue: Addressing Client Queries
Q: When should laminated vs. non-laminated bags be used?
A: Laminated bags (e.g., BOPP/PE layers) suit hygroscopic fertilizers like urea, offering <0.5% moisture absorption. Non-laminated, breathable bags are ideal for slow-release granules requiring airflow.
Q: Are inner liners necessary for powdered fertilizers?
A: Yes. Xinfeng’s 50kg DAP bags use 25μm PE liners with ultrasonic seals, reducing spillage by 90%.
Technical Innovations in Printing and Materials
- Anti-Corrosion Coatings
- Technology: Fluoropolymer-coated PP bags resist acidic fertilizers (pH 2–3), retaining 95% tensile strength after 6 months of exposure.
- Smart Printing
- Case Study: Taian Xinfeng’s 6-color gravure printing ensures QR codes remain scannable after 12 months outdoors, enhancing traceability.
- Sustainability
- Trend: Brands like Phenisky Industrial use 30% recycled PP, cutting carbon footprints by 25% while complying with EN 13432 compostability standards.
Performance Metrics and FAQs
Table 1: Critical PP Bag Parameters for Fertilizers
Parameter | Test Standard | Typical Value |
---|---|---|
Thickness | ASTM D3776 | 90–120 g/m² |
Tensile Strength | ISO 13934-1 | ≥5.5 kN/m |
Seam Strength | ASTM D6199 | ≥4.0 kN/m |
Moisture Barrier | ASTM E96 | ≤1.0 g/m²/day |
FAQs
- Q: What thickness is ideal for 50kg fertilizers?
- A: 100–120 g/m² with PE lamination ensures durability and moisture resistance.
- Q: Can valve bags handle powdered fertilizers?
- A: Yes, but double-valve designs (e.g., Vedhaa’s VP-7) minimize dust during filling.
Future Trends
The rise of automated Form-Fill-Seal (FFS) systems and biodegradable additives (e.g., TDPA™) is revolutionizing PP bag production. For instance, Starlinger’s AD*STAR® technology enables 2,000 bags/hour output with zero material waste[citation:N/A].
External Resources:
- Discover how moisture-proof woven bags enhance agrochemical packaging.
- Explore recyclable PP bags for ESG-aligned solutions.
By merging technical rigor with regulatory compliance, PP woven bags continue to dominate global fertilizer packaging, offering scalable and sustainable solutions for diverse industrial needs.