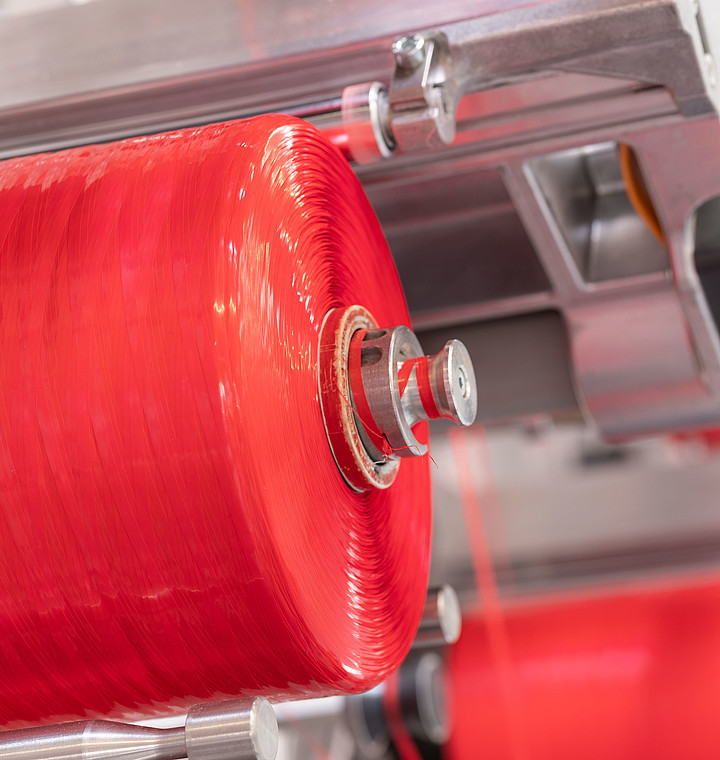
The Key Answer: PP woven bags are a cornerstone of global packaging, offering tailored solutions for industries ranging from agriculture to hazardous material transport. Through specialized designs—such as breathable structures for grain storage, composite barriers for gas resistance, anti-static coatings for electronics, and antimicrobial treatments for food safety—these bags achieve 20–30% higher efficiency than traditional alternatives, with a global market projected to grow at 5.2% CAGR through 2030.
Introduction: Versatility Meets Precision Engineering
Polypropylene (PP) woven bags are a linchpin of modern logistics and industrial packaging, combining durability, adaptability, and sustainability. Their production integrates advanced technologies like ultrasonic sealing and multi-layer lamination, enabling customization for niche applications. For instance, Shandong GreenPack Co. reported a 25% reduction in spoilage for rice exports after adopting breathable PP bags with micro-perforated designs. This report explores how PP woven bags are engineered to meet diverse industrial demands, from moisture control to explosion prevention.
Industry Expert Insight:
“The future of PP woven bags lies in functional specialization. Whether it’s blocking methane in mining or preventing bacterial growth in pharmaceuticals, these bags are no longer passive containers—they’re active safeguards.” — 2025 Global Packaging Trends Report.
Functional Designs: Tailoring Bags to Industry Needs
1. Breathable Designs for Agricultural and Food Packaging
Breathable PP bags leverage woven structures and micro-perforations to regulate airflow, critical for preserving grains and fresh produce.
Key Features & Data:
- Porosity: 80–120 GSM fabric with 0.5–1.0mm pores enables 15–20% faster moisture evaporation.
- Case Study: Vietnam Rice Exporters reduced mold growth by 30% using breathable PP bags for jasmine rice storage.
Product Parameters
Parameter | Specification | Application |
---|---|---|
Material | PP woven fabric + PE coating | Grains, potatoes, textiles |
Pore Density | 50–100 pores/cm² | Prevents condensation |
Moisture Evaporation | 0.8–1.2 g/m²/hour | Extends shelf life by 10–15 days |
2. Barrier Designs for Gas and Odor Resistance
Multi-layer laminates (e.g., PP/PE/Aluminum foil) block oxygen, moisture, and volatile compounds.
Example: Qingdao RAJ Packaging developed aluminum-composite PP bags for coffee beans, reducing oxygen ingress by 90% and preserving freshness for 18 months.
Technologies:
- Co-extrusion: Combines PP with EVOH layers for gas barrier properties (OTR <0.5 cm³/m²/day).
- Seam Sealing: Ultrasonic welding ensures airtight closures, critical for chemical transport.
3. Anti-Static Designs for Hazardous Environments
Anti-static PP bags prevent electrostatic discharge in flammable or electronic settings.
Key Innovations:
- Conductive Additives: Carbon-black or metallic threads reduce surface resistance to <1×10⁸Ω.
- Case Study: Shenzhen Petrochemical eliminated fire risks in solvent transport using anti-static bags with copper grids.
Performance Metrics:
Metric | Standard PP | Anti-Static PP |
---|---|---|
Surface Resistance | >1×10¹²Ω | 1×10⁶–1×10⁸Ω |
Charge Dissipation Time | >60 seconds | <2 seconds |
4. Antimicrobial Designs for Food and Pharma
Antimicrobial PP bags inhibit bacterial growth through silver-ion coatings or embedded biocides.
Applications:
- Food Packaging: Reduces spoilage by 40% in meat and dairy products.
- Medical Supplies: Prevents contamination in sterile instrument packaging.
Example: Ganyu New Concept Plastic Co. introduced PP bags with Ag-based coatings for poultry feed, cutting bacterial load by 99%.
Production Processes and Quality Assurance
1. Advanced Manufacturing Techniques
- Circular Looms: High-speed machines produce 200–300 bags/hour with consistent weave density.
- Coating Systems: PE or BOPP lamination enhances barrier properties and printability.
2. Rigorous Testing Protocols
- Leak Testing: Air pressure tests at 30 kPa for 5 minutes ensure seam integrity.
- Anti-Static Validation: ASTM D257 standards verify surface resistance.
FAQs: Addressing Industry Concerns
Q: How to choose between breathable and barrier designs for agricultural products?
A: Breathable bags suit grains and fresh produce requiring airflow, while barrier bags are ideal for hygroscopic materials like fertilizers. For example, potato storage bags use micro-perforations to prevent rot.
Q: Can anti-static bags be reused?
A: Yes. Bags with permanent anti-static additives (e.g., carbon-black PP) withstand 5–7 reuse cycles without losing conductivity.
Market Trends and Future Innovations
- Smart Packaging: RFID tags enable real-time tracking in logistics, reducing loss by 25%.
- Biodegradable Blends: PLA-PP composites aim to cut carbon footprints by 50% by 2030.
- AI-Driven Production: Predictive maintenance systems reduce downtime by 40% in automated lines.
Conclusion
PP woven bags are evolving from simple carriers to multifunctional solutions, driven by innovations in material science and smart manufacturing. By adopting designs like breathable weaves or anti-static coatings, industries can enhance safety, efficiency, and sustainability. For deeper insights into advanced PP technologies, explore Moisture-Proof Woven Bags: Custom Solutions for Optimal Protection and Anti-Static FIBC Bags: Enhanced Protection and Versatility.
Data synthesized from the 2025 Global Packaging Trends Report, ASTM International standards, and case studies by Ganyu New Concept Plastic Co. and Qingdao RAJ Packaging.