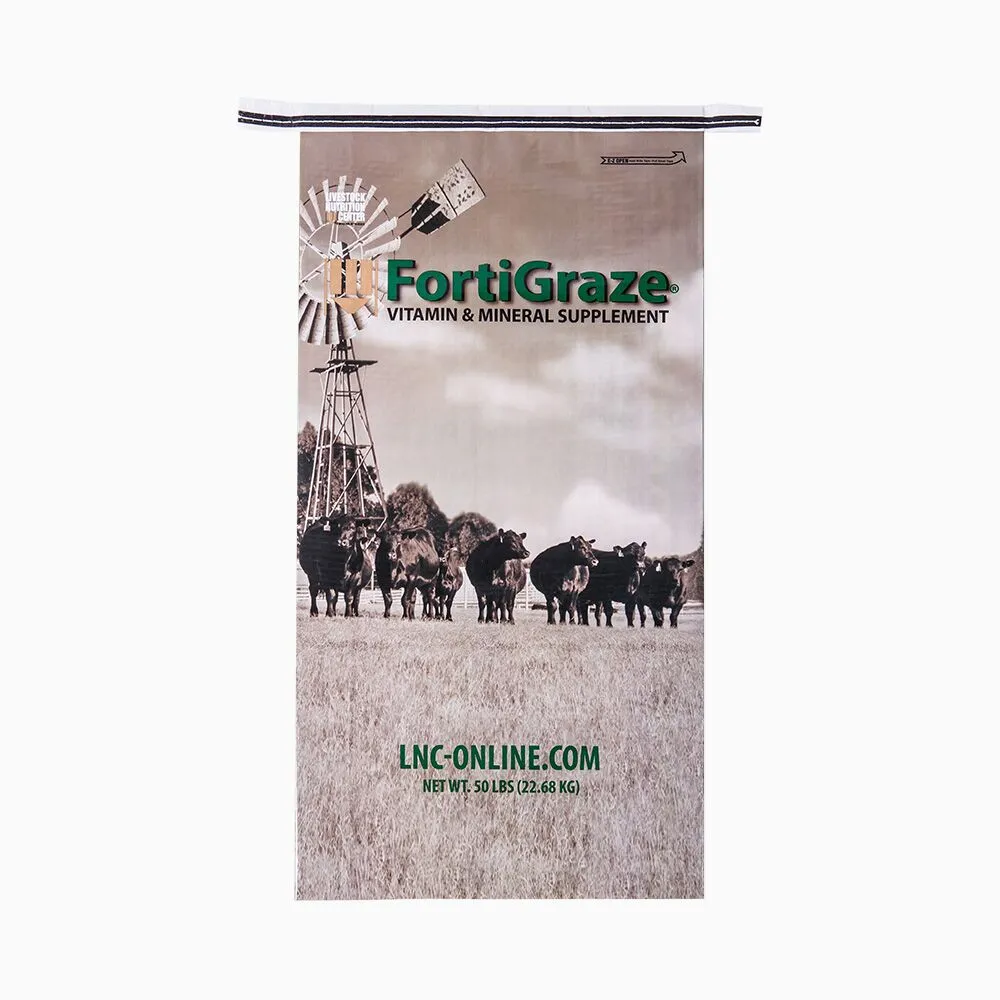
Main Answer: Printed BOPP Woven Bags—including Printed BOPP Woven sacks, BOPP Woven Bags, and Printed Woven Bags—excel as a robust, visually compelling packaging solution. By uniting woven polypropylene (PP) strength with Biaxially Oriented Polypropylene (BOPP) lamination, these bags deliver high-definition graphics, excellent tear resistance, and customizable features that outperform traditional packaging materials across agriculture, construction, pet food, and more. Crucially, the extrusion, drawing, and weaving processes determine a bag’s mechanical durability and flexibility, ensuring the final product meets wide-ranging market needs.
A 2026 forecast by the World Packaging Organisation highlights growing demand for advanced PP-based woven bags at an annual rate of around 6%. This increase stems from evolving packaging regulations, consumer emphasis on brand visuals, and the cost-effectiveness of reusable, sturdy bags. Below, we explore how extrusion, drawing, and weaving each enhance the resilience of Printed Woven Bags, and why Printed BOPP Woven sacks remain a top choice for businesses seeking elevated product protection and shelf impact.
1. Introduction to Printed BOPP Woven Bags
1.1 Lamination and High-Impact Graphics
Printed BOPP Woven Bags combine:
- Woven PP Fabric: A dense web of polypropylene tapes provides load-bearing support.
- BOPP Film Lamination: Offers photorealistic printing surfaces for logos, imagery, and branding details.
Example: A Southeast Asian rice distributor replaced generic plastic sacks with BOPP-laminated woven bags showcasing rice field images. The result: a notable rise in brand recognition and repeat purchases.
1.2 Key Advantages for Multiple Industries
- Superior Strength: Woven polypropylene withstands aggressive handling, heavy loads, and repetitive stacking.
- Vivid Printing: BOPP film accommodates detailed, fade-resistant designs appealing to brand-conscious consumers.
- Cost Efficiency: Over product lifecycles, reduced breakage and fewer product returns justify the slightly higher upfront bag cost.
2. Extrusion, Drawing, and Weaving: How Each Affects Durability and Flexibility
Three critical processes—extrusion, drawing, and weaving—drive performance in Printed BOPP Woven sacks and Printed Woven Bags:
2.1 Extrusion
Polypropylene resin melts and flows through a die to form tapes or filaments.
- Resin Purity: Minimizes tape defects, ensuring uniform thickness and reliable strength.
- Temperature Precision: Stabilizes the polymer, preventing cracks or weak points in the extruded tapes.
Example: A fertilizer firm in Brazil noted that maintaining consistent extrusion temperature profiles halved tape breakage, leading to stronger final fabrics and fewer defective bags.
2.2 Drawing (Stretching)
Drawn tapes achieve superior tensile strength and resistance to splitting:
- Molecular Orientation: Stretching aligns polymer chains, increasing tear resistance.
- Denier Adjustments: Tapes can be thicker (for heavier loads) or thinner (for lighter, more flexible bags) based on draw ratios.
Example: A pet food manufacturer required high-capacity BOPP Woven Bags for 20 kg dog feed. Specifying a higher draw ratio produced tapes able to withstand forklift and pallet handling demands.
2.3 Weaving
Woven tapes interlace in warp (long direction) and weft (cross direction), influencing:
- Fabric Density: Tighter weaves (10×10, 12×12) handle finer products like flour or powders.
- Breathability vs. Barrier: Looser weaves aid ventilation, while denser patterns reduce dust leaks.
Example: A chemical powder exporter opted for a tighter (12×12) weave, effectively preventing dust seepage and damage during overseas shipping.
3. Conversation Snippet
Topic: Boosting Bag Strength Through Drawing
Question: “We need BOPP Woven Bags that can handle 40 kg loads without tearing. Is that feasible?”
Answer: “Yes. By raising the draw ratio in tape stretching and opting for dense weaving, your Printed BOPP Woven Bags gain both higher tear resistance and robust load capacity—while preserving the bag’s print and functionality.”
4. Product Parameters Table
Parameter | Typical Range | Effect on Bag Performance |
---|---|---|
PP Resin Quality | Virgin / Recycled | Influences consistency & mechanical strength |
Extrusion Temp | ~180–220°C | Controls tape stability and polymer integrity |
Draw Ratio | 4:1 to 8:1 | Boosts tensile strength with higher orientation |
Weave Density | 8×8, 10×10, 12×12 | Affects breathability & load distribution |
BOPP Film Thickness | 15–30 microns | Dictates print detail & moisture barrier |
Print Method | Flexographic / Gravure | Determines color accuracy & coverage |
Load Capacity | 5–50 kg (commonly) | Based on weaving density & tape thickness |
5. FAQs
- Q: What distinguishes Printed BOPP Woven Bags from standard woven sacks?
A: BOPP lamination adds a premium print surface and extra moisture protection, elevating brand presentation and durability. - Q: Are these bags suitable for moisture-sensitive products?
A: Yes. BOPP film shields contents from external humidity, though optional micropores help reduce condensation for items needing some ventilation. - Q: How can we guarantee color vibrancy over time?
A: Quality inks and lamination ensure fade resistance, particularly when bags aren’t stored under direct UV light for extended durations. - Q: Do heavier tapes compromise bag flexibility?
A: Not necessarily. Proper stretching and weaving preserve pliability while bolstering strength. Selecting the right denier ratio is key. - Q: Can Printed Woven Bags be recycled?
A: Polypropylene (#5) is recyclable, though thick lamination may necessitate specialized delamination for optimal recycling processes.
6. Two External Links
Uncover advanced print and performance advantages of Printed BOPP Woven Bags:
Printed BOPP Woven Bags
Learn how BOPP Woven Bags transform packaging in construction and beyond:
BOPP Woven Bags
7. Practical Use Cases and Benefits
7.1 Agriculture and Food
For grains, seeds, feed, and fertilizers:
- Photo-Realistic Branding: BOPP surfaces highlight farm images or logos.
- High Tensile Strength: Resists forklift prongs, repetitive dropping, or stacking pressure.
Example: A maize exporter in Argentina switched to photorealistic Printed Woven Bags with improved seam reinforcement, reducing product wastage and boosting brand visibility in retail.
7.2 Construction Materials
Harsh conditions and heavy loads define cement, sand, or chemical powders:
- Dense Weave: Minimizes powder leakage.
- Water Repellent: BOPP lamination counters moisture, crucial for on-site durability.
Example: A construction supply firm in the Middle East drastically cut returns by adopting lamination that resisted humidity and ensured easier stacking.
7.3 Pet Food and Animal Feed
High-load packaging with detailed brand messaging:
- Dynamic Print: Bright, engaging imagery of pets or feed results in strong shelf impact.
- Resilient Weave: Endures frequent transport in large distribution channels.
Example: A US-based pet food label reported a 15% revenue hike after rebranding with large-format, color-accurate BOPP-laminated sacks that better withstood warehouse handling.
7.4 Industrial Chemicals
Flammable powders or corrosive materials call for advanced protective measures:
- Chemical-Resistant Films: BOPP coatings handle mild spillage or chemical fumes.
- Anti-Static Additives: Reduce spark risks for dust-laden environments.
Example: A European fertilizer maker integrated anti-static BOPP-laminated woven sacks to store nitrates safely, cutting potential warehouse fire hazards.
8. Future Trends and Outlook
8.1 Sustainability Initiatives
With heightened focus on eco-friendly methods, producers explore:
- Recycled PP Tapes: Lower virgin plastic usage.
- Biodegradable Additives: Experimenting with partial compostability.
- Improved Delamination: Easing film separation for more efficient recycling.
Example: A Northern European feed producer introduced partially recycled, BOPP-laminated sacks, maintaining tear resistance while upgrading green credentials.
8.2 Intelligent Packaging
From RFID tags to interactive labels, Printed Woven Bags adapt to digital inventory systems:
- Traceability: Facilitates supply chain oversight for high-value goods.
- Consumer Engagement: QR codes link customers to product videos or origin stories.
Example: A coffee roaster in Latin America affixed QR-coded stickers to each bag, enabling retailers to track bean freshness and convey farm-to-cup transparency.
8.3 Print Innovations
Tech advances in flexographic, gravure, and digital printing methods promise:
- Enhanced Resolution: Crisp brand visuals that draw consumer attention.
- Unique Coatings: Spot varnish or metallic inks for premium packaging lines.
Example: A specialty fertilizer brand in Asia used metallic highlights on Printed Woven Bags, exuding a high-end aesthetic that distinguished them from competitors.
9. Conclusion
Printed BOPP Woven Bags, Printed BOPP Woven sacks, BOPP Woven Bags, and Printed Woven Bags epitomize modern packaging evolution—blending eye-catching lamination with the heavy-duty reliability of woven polypropylene. Central to their success are the extrusion, drawing, and weaving processes, which optimize tape consistency, enhance tensile strength, and tailor breathability or barrier properties. The result is packaging that not only excels in display-ready branding but also reduces breakage, preserves contents, and withstands complex shipping demands.
As sustainability pressures intensify and global supply chains crave higher-efficiency solutions, Printed Woven Bags stand poised for continued growth. Whether it’s agricultural produce, pet food, or industrial commodities, the unique fusion of BOPP lamination and woven PP construction delivers a proven balance of aesthetics, functionality, and cost-effectiveness—making Printed BOPP Woven Bags a top-tier choice for brands seeking impact and durability in an increasingly competitive marketplace.