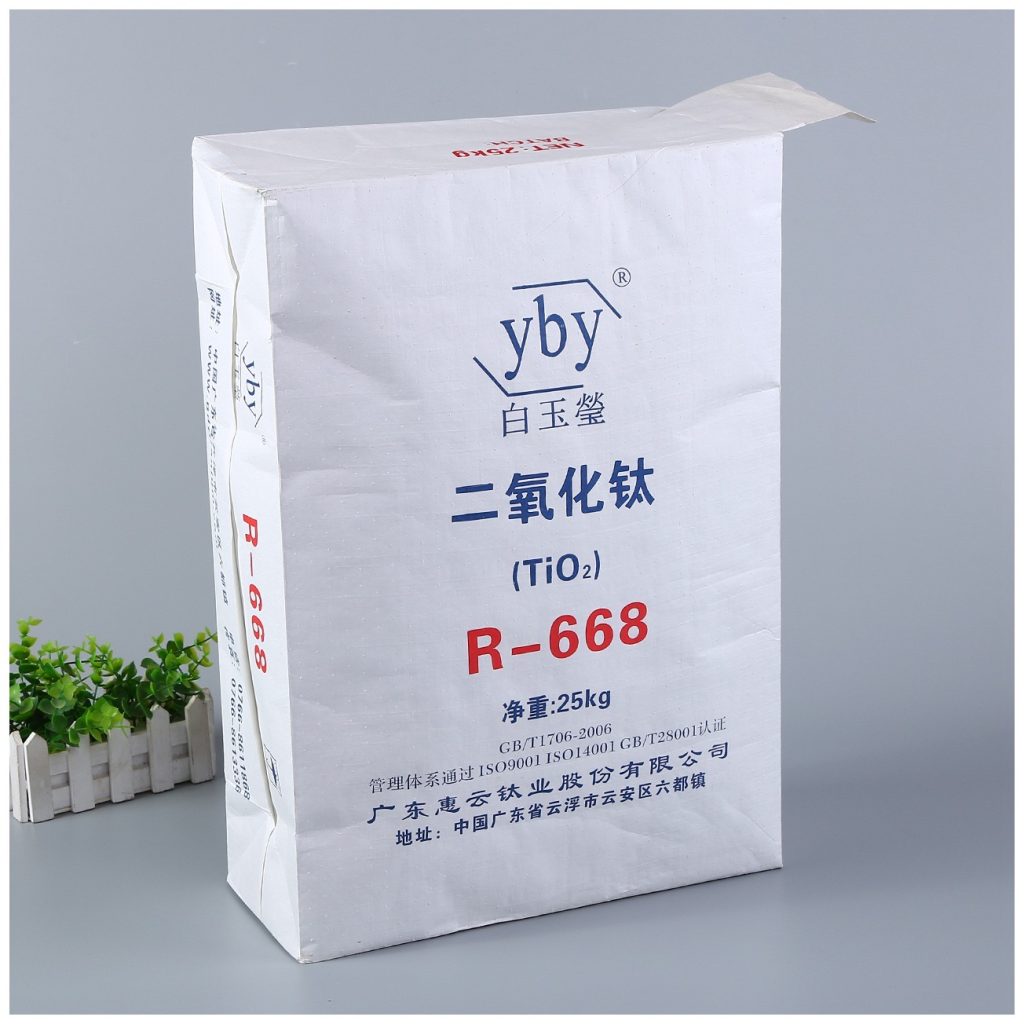
In the world of packaging, Printed Woven Bags are gaining significant popularity across a variety of industries, from agriculture to manufacturing. These bags, made from woven polypropylene (PP) fabric, are robust, customizable, and offer superior protection. With advanced printing technology, Printed Woven Sacks can be tailored with multi-color logos, designs, and product information, offering not only functionality but also brand visibility. As demand for customization grows, the quality of material selection and the equipment used in production become increasingly important.
At VidePak, we leverage advanced technology from Austria’s Starlinger and Germany’s W&H, two leaders in the manufacturing of woven bag equipment, to ensure that our Custom Woven Bags meet the highest standards in quality, durability, and aesthetic appeal. With innovations such as fine and coarse filaments, these technologies play a critical role in determining the performance characteristics of the bags, including their strength, appearance, and overall reliability. In this article, we explore the differences in filament selection, the impact of our high-tech equipment on manufacturing, and how these factors contribute to the final product.
Understanding the Choice of Fine and Coarse Filaments in Woven Bags
The choice between fine and coarse filaments is crucial when manufacturing Printed PP Woven Bags, as it directly influences the bag’s strength, weight, and printing quality. Fine filaments are thinner and more tightly woven, giving the bag a finer texture and providing superior printability. They are particularly well-suited for Printed Woven Bags where high-resolution logos and intricate designs are required. On the other hand, coarse filaments are thicker and offer enhanced strength and durability, making them ideal for industrial applications where the bag will carry heavy loads or endure rough handling.
In many cases, manufacturers use a blend of both types of filaments to optimize the final product’s performance. Fine filaments provide an excellent surface for high-quality printing, while coarse filaments contribute to the bag’s structural integrity and ability to carry heavy loads.
Below is a table outlining the key differences between fine and coarse filaments used in Custom Woven Bags:
Filament Type | Strength | Weight | Print Quality | Common Applications |
---|---|---|---|---|
Fine Filament | Moderate to High | Light | High, fine details | Retail packaging, promotional bags |
Coarse Filament | High | Heavy | Moderate, less detailed | Industrial, heavy-duty bags |
Equipment and Technology: The Starlinger and W&H Advantage
The performance and consistency of Printed Woven Sacks depend significantly on the technology used during production. At VidePak, we employ the latest equipment from Starlinger and W&H, which are well-regarded for their ability to produce high-quality woven bags with precision and efficiency.
Starlinger Equipment
Starlinger’s state-of-the-art machinery is designed for the production of Custom Woven Bags, ensuring both the quality of the woven fabric and the accuracy of the printing process. Starlinger’s circular looms and extrusion lines are known for their high throughput, ensuring large quantities of Printed PP Woven Bags are produced quickly without sacrificing quality. Their equipment enables us to integrate fine filament technology for enhanced print quality, while coarse filaments ensure durability for heavy-duty applications.
With Starlinger’s technology, we can produce multi-layered woven bags that offer superior strength and moisture resistance, vital for industries such as agriculture, construction, and logistics. Moreover, their advanced extrusion lines ensure that the material is consistently high-quality, allowing us to maintain strict standards in every batch of Printed Woven Sacks.
W&H Technology
W&H equipment plays an essential role in the lamination and printing processes of our Custom Woven Bags. Their high-precision printing machines offer multi-color printing capabilities, allowing for vibrant, clear, and durable designs. This is particularly valuable when producing Multiple Color Bags that require intricate logos and branding details.
Incorporating fine filaments into the bags not only improves their appearance but also enhances their ability to hold fine prints and designs. W&H’s technology allows us to seamlessly laminate the bags, improving their resistance to environmental elements, while maintaining the clarity of the printed graphics. Whether the design involves a single color or multiple colors, W&H’s cutting-edge machinery ensures that every bag is produced to meet the highest aesthetic and functional standards.
Customization and Flexibility in Printed Woven Bags
One of the key advantages of Printed Woven Bags is the level of customization they offer. At VidePak, we understand that every business has different packaging needs, whether it’s a unique logo, specific color scheme, or size requirements. Our expertise, combined with the versatility of Starlinger and W&H equipment, allows us to create Custom Woven Bags that meet the precise demands of our clients.
We offer a wide range of customization options, including:
- Multi-color printing: Ideal for companies that want to showcase their branding with high-quality, detailed prints.
- Custom sizes: Bags can be produced in different dimensions to accommodate various products, from small retail items to large industrial goods.
- Various filament types: Depending on the needs of the client, we can choose between fine or coarse filaments to create the desired strength and appearance.
- Special coatings: We offer lamination and additional coatings for enhanced moisture resistance or extra durability in harsh environments.
The ability to tailor each bag to the exact needs of our clients is what makes Printed Woven Bags such a popular choice for many industries.
The Importance of Material and Manufacturing Expertise
At VidePak, the combination of the best materials and cutting-edge equipment is the cornerstone of our success in producing high-quality Printed Woven Sacks. The careful selection of raw materials, including high-quality PP pellets, ensures that our bags meet the highest standards for both strength and appearance.
Our production process incorporates advanced quality control checks at every stage, from raw material selection to the final product. This ensures that every Custom Woven Bag is durable, reliable, and up to industry standards. The precision of our equipment, paired with our technical expertise, guarantees that the final product performs well under the conditions it was designed for, whether in retail, agriculture, or heavy-duty applications.
Conclusion
The rise in demand for Printed Woven Bags reflects their versatility, durability, and ability to be customized for various applications. Whether you’re looking for bags that showcase your brand with intricate designs or need bags that can handle heavy-duty loads, Custom Woven Bags are the ideal solution.
The choice of filament, whether fine or coarse, has a significant impact on the bag’s performance, and at VidePak, we use the best equipment from Starlinger and W&H to ensure that every bag is made to the highest standards. Our equipment allows us to produce Multiple Color Bags with exceptional print quality, while our expertise in material selection guarantees the durability and strength needed for even the most demanding applications.
By partnering with VidePak, businesses can rest assured that they will receive Printed PP Woven Bags that not only meet their functional needs but also contribute to their branding and market presence.
For more information on our customized solutions, check out our Printed Woven Bags and Custom Woven Bags pages.