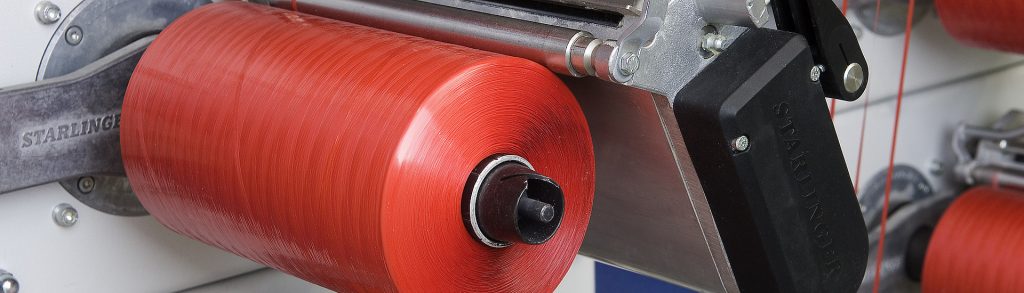
Introduction
In the era of automated logistics and just-in-time delivery, warehouses demand packaging solutions that integrate functionality with intelligent design. Printed woven bags, particularly those utilizing color-coded labeling, have emerged as critical tools for streamlining operations. For VidePak, a company with 30+ years of expertise in PP-based packaging, innovations in material science and customization capabilities are driving advancements in warehouse management. This report explores how VidePak’s printed woven bags address three core pillars: parameter optimization, anti-static functionality, and load-bearing performance, while aligning with global sustainability and safety trends.
1. Product Parameters: Balancing Thickness, Weight, and Size
Thickness & Grammage (GSM)
The thickness and grammage of woven bags directly impact durability and cost-efficiency. VidePak’s PP bags are engineered within the following ranges:
- Thickness: 80–150 GSM (grams per square meter), tailored to application needs.
- 80–100 GSM: Ideal for lightweight products like powdered additives (e.g., food-grade salt).
- 100–120 GSM: Standard for construction materials (e.g., cement, plaster powder).
- 120–150 GSM: Heavy-duty applications, such as industrial chemicals or bulk agricultural goods.
- Size Flexibility:
- Width: 30–80 cm
- Height: 50–120 cm
Customizable dimensions ensure compatibility with automated conveyor systems and pallet configurations.
Case Study: A Vietnamese cement manufacturer reduced transport damage by 25% after adopting VidePak’s 120 GSM bags with reinforced stitching.
Anti-Static Design Integration
Anti-static woven bags are critical for industries handling flammable powders (e.g., toner, magnesium) or sensitive electronics. VidePak achieves this through:
- Conductive Additives: Carbon or metal-coated PP fibers are woven into the fabric, reducing surface resistivity to 10⁶–10⁹ Ω/sq, effectively dissipating static charges.
- Multi-Layer Lamination: Combining PP with polyethylene (PE) or aluminum foil layers creates a Faraday cage effect, shielding contents from external electrostatic discharge.
Dialogue Example:
Q: “How do anti-static bags prevent dust explosions?”
A: “By embedding conductive fibers, our bags neutralize static buildup during filling and transport, eliminating ignition risks in volatile environments.”
2. Anti-Static Mechanisms: Science and Application
Anti-static woven bags rely on two primary principles:
- Conductive Pathways: Conductive materials (e.g., carbon) create a network that safely channels static electricity to the ground.
- Shielding Layers: Aluminum or metallized PET layers block external electromagnetic interference (EMI), protecting sensitive components like circuit boards.
Technical Insight: A 2024 study in Packaging Technology and Science found that multi-layer anti-static bags reduced electrostatic discharge incidents by 90% in electronics logistics.
3. Load Capacity and Structural Integrity
VidePak’s woven bags are engineered to withstand rigorous handling:
- Load Range: 25–50 kg, depending on GSM and stitching type.
- Single-Lock Stitching: Supports up to 30 kg (e.g., agricultural seeds).
- Double-Lock Stitching: Reinforced seams for 50 kg loads (e.g., construction materials).
- Reinforcements:
- BOPP Lamination: Enhances tear resistance by 40%, critical for abrasive materials like sand.
- PE Inner Liners: Prevent moisture ingress, extending shelf life for hygroscopic products like joint fillers.
Parameter | Specification |
---|---|
Max Load Capacity | 50 kg (double-stitched) |
Tensile Strength | 8–12 N/mm² |
Moisture Barrier | PE-coated liners (WVTR <5 g/m²/day) |
Print Durability | UV-resistant CMYK, 6–8 color options |
FAQs: Addressing Industry Concerns
Q1: How does color coding improve warehouse efficiency?
A: VidePak’s color strips (e.g., red for hazardous chemicals, green for food-grade products) enable instant visual categorization, reducing sorting time by 30%.
Q2: Can anti-static bags be recycled?
A: Yes. VidePak’s “EcoShield” line uses 30% recycled PP without compromising conductivity, aligning with EU circular economy mandates.
VidePak’s Competitive Edge
Leveraging Starlinger machinery and 100+ circular looms, VidePak produces 20 million bags annually with:
- Rapid Customization: 72-hour prototyping for color-coded designs.
- Certifications: ISO 9001, REACH, and FDA compliance for global markets.
- Sustainability: 100% recyclable PP and water-based inks reduce carbon footprint by 25%.
Market Trends and Future Outlook
The global woven bag market is projected to grow at 5.5% CAGR through 2030, driven by e-commerce and construction sectors. VidePak’s R&D focuses on:
- Smart Tags: RFID-enabled bags for real-time inventory tracking.
- Lightweight Designs: Reducing GSM by 15% while maintaining strength through nano-reinforced PP.
Conclusion
Printed woven bags are no longer passive containers but active contributors to warehouse efficiency. VidePak’s fusion of color-coded intelligence, anti-static engineering, and load-optimized designs positions it as a pioneer in industrial packaging. As automation and ESG compliance reshape logistics, the company’s commitment to innovation ensures it remains at the forefront of the $12 billion global market.
External Links: