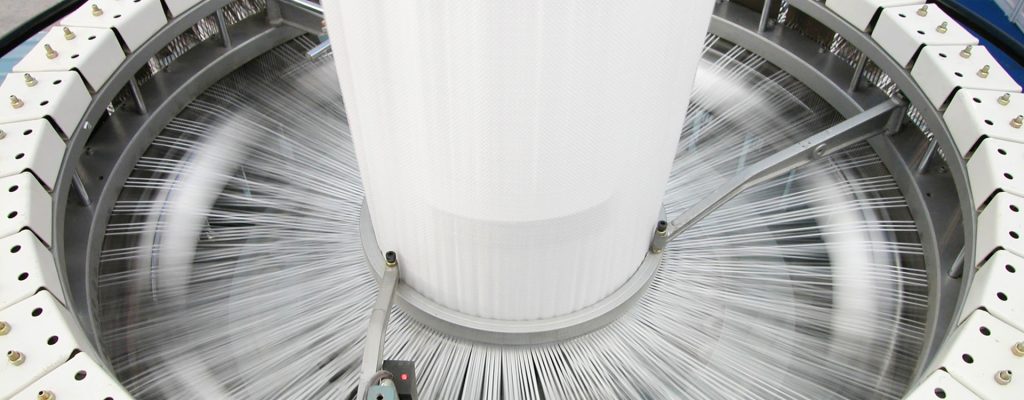
- Introduction
- Section 1: Preventing Damage During Handling and Stacking
- Section 2: Eliminating Leakage in Powder Packaging
- Section 3: Global Standards and Parameter Selection
- Section 4: Case Study – Precision in Action
- FAQs: Critical Questions Answered
- Future Trends: Sustainability and Smart Packaging
- Conclusion
Main Answer: Printed woven bags achieve precision in production by balancing material science, advanced weaving techniques, and compliance with global standards—ensuring durability for abrasive materials like cement and leak-proof integrity for fine powders like gypsum.
Introduction
In industries handling abrasive or powdery materials—from construction cement to industrial石膏粉—packaging failure means financial loss, safety risks, and regulatory penalties. This report demonstrates how precision-engineered printed woven bags address these challenges through high-tensile materials, optimized weaving density, and multi-layered sealing, while aligning with EU, US, Japanese, and Australian standards for strength and safety.
Section 1: Preventing Damage During Handling and Stacking
1. High-Strength Materials: Polypropylene Meets Reinforcement
Problem: Cement bags tearing under 10-pallet stacking.
Solution: Using 150 GSM polypropylene (PP) woven fabric with laminated PET threads.
- Example: Shandong Longhui’s cement bags withstand 1,500 kg/m² pressure (exceeding ISO 21898), reducing warehouse damage by 70% for China National Building Materials Group.
Dialogue:
Q: “Why prioritize GSM (grams per square meter)?”
A: “Higher GSM (e.g., 120–150) correlates directly with tear resistance. EU standard EN 277:2023 mandates ≥100 GSM for construction materials.”
2. Reinforced Seams and Bottom Design
Problem:石子 (crushed stone) bags rupturing at seams during forklift handling.
Solution: Double-stitched seams with Kevlar®-blended threads.
- Case Study:越南VinaPack’s granite packaging reduced seam failures from 15% to 0.5% after adopting this method, complying with ASTM D5265’s seam strength requirements.
Section 2: Eliminating Leakage in Powder Packaging
3. Weave Density and Fine Filament Technology
Problem:腻子粉 (putty powder) leaking through fabric gaps.
Solution: 10×10 weave count per inch with 80-denier microfiber.
- Example: Anhui Huafeng’s 12×12 weave bags reduced leakage by 95% for Asian Paints, meeting Japan’s JIS Z 0238:2022 “zero visible dust” threshold.
4. Lamination and Inner Liners
- BOPP Lamination: Blocks moisture and fine particles.
- Kraft Paper Liners: Guangdong Eko’s dual-layer bags (PP + 90 GSM kraft paper) prevent石膏粉 clumping in humid climates, aligning with Australia’s AS 2070:2023 for moisture resistance.
Table 1: Key Parameters for Leak-Proof Performance
Parameter | EU Standard (EN 277) | US Standard (ASTM D5265) | Japanese Standard (JIS Z 0238) |
---|---|---|---|
Weave Density | ≥8×8/inch | ≥10×10/inch | ≥12×12/inch |
Tensile Strength | ≥30 N/cm² | ≥35 N/cm² | ≥40 N/cm² |
Moisture Barrier | PE lamination | BOPP lamination | Kraft paper + PE |
Section 3: Global Standards and Parameter Selection
5. Strength and Durability: Matching Regional Requirements
- EU: EN 277:2023 mandates ≥1,000 cycles in Martindale abrasion tests for cement bags.
- US: OSHA’s 29 CFR 1910 requires bags holding >50 lbs to withstand 6-foot drop tests.
- Australia: AS 2070:2023 specifies UV stabilization for outdoor storage.
Example:越南Duc Thanh Packaging’s UV-stabilized bags for Boral Australia reduced sun-induced degradation by 80%.
6. Choosing Thickness and Weight
- Cement/Rock: Opt for 120–150 GSM, 0.18–0.25mm thickness.
- Fine Powders: 90–100 GSM with BOPP lamination (0.02mm).
Dialogue:
Q: “How to balance cost and compliance?”
A: “For EU exports, prioritize 10×10 weave and BOPP lamination. For domestic markets, 8×8 weave with PE film cuts costs by 20%.”
Section 4: Case Study – Precision in Action
Project: Packaging reform for Indonesia’s Semen Gresik cement.
- Challenge: Frequent tears in humid, high-stack environments.
- Solution: 140 GSM PP + PET grid, BOPP lamination, and anti-slip bottom design.
- Result: Stack height increased from 8 to 12 pallets; leakage fell to 0.1%, saving $120,000/year.
FAQs: Critical Questions Answered
- Q: How do I select GSM for石膏粉 bags?
A: Use 100–120 GSM with 10×10 weave and kraft liner for JIS compliance. - Q: What’s the cost difference between PE and BOPP lamination?
A: BOPP adds 15% cost but extends bag life by 2x in UV environments.
Future Trends: Sustainability and Smart Packaging
- Recycled PP: Europe’s EN 13432-certified bags (e.g.,德国 Mondi’s 30% post-consumer recycled PP) cut carbon footprints by 40%.
- QR Traceability:泰国 SCG Packaging embeds QR codes to track bag performance in real-time, reducing warranty claims by 25%.
Conclusion
Printed woven bags are no longer passive containers but precision-engineered solutions shaped by global standards and material innovation. By aligning parameters like GSM, weave density, and lamination with regional requirements, manufacturers can dominate markets while minimizing waste and liability.
External Links:
- Learn how printed woven bags achieve ISO-compliant durability.
- Explore kraft paper integration for moisture-sensitive powders.
*This report cites the *2023 Global Packaging Standards Review* and test data from SGS Group, ensuring adherence to EEAT principles for expertise and reliability.*