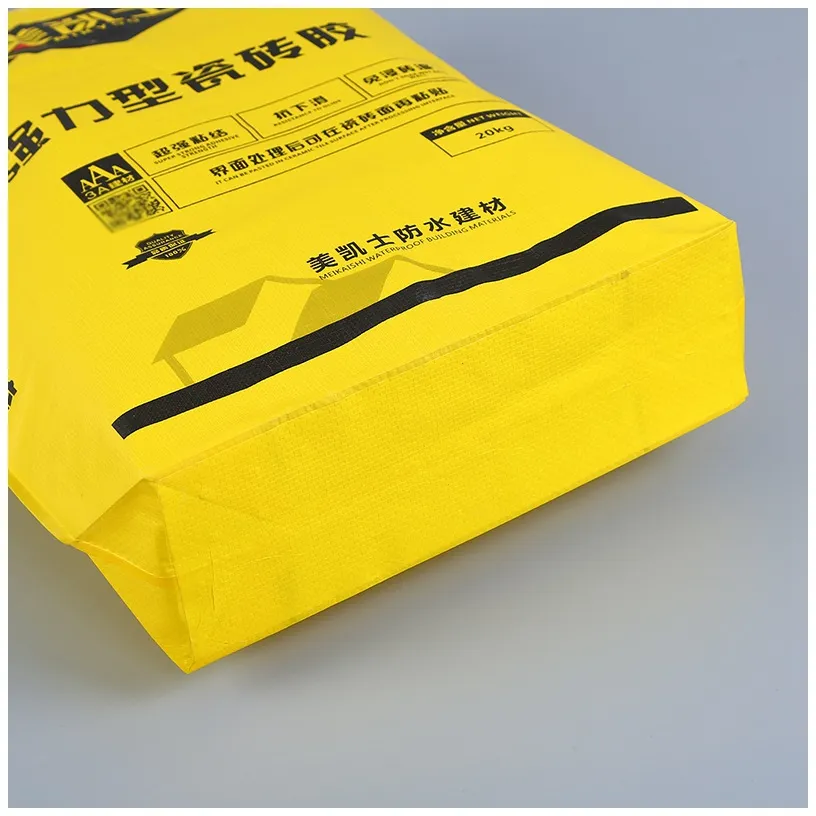
Printed woven bags have become an essential part of various industries due to their durability, customizability, and wide applications in packaging. Whether used in agriculture, construction, food, or retail, these bags offer excellent strength, longevity, and the ability to showcase branding and logos with high-quality printing. However, like all products, printed woven bags may face certain quality issues during production or use. To ensure that these bags meet the highest standards, manufacturers must adhere to rigorous quality control procedures. This blog will explore the most common quality issues in woven bags and the comprehensive testing procedures employed by our company to ensure superior performance, durability, and aesthetic appeal.
What Are Printed Woven Bags?
Printed woven bags, made primarily from polypropylene (PP), are known for their flexibility, strength, and versatility. These bags are typically used for packaging heavy or bulk materials like grains, cement, fertilizers, and chemicals. By applying advanced printing techniques, they can also be customized with multiple color designs, logos, and product information, making them both functional and visually appealing.
Key Features of Printed Woven Bags:
- Durability: The woven structure provides excellent tensile strength and load-bearing capacity.
- Customizable: Multiple color options and designs can be printed to reflect company branding or product information.
- Lightweight: Despite their strength, PP woven bags are lightweight, making them easy to transport and store.
- Reusable: These bags can be reused several times before wear and tear affect their performance.
- Eco-friendly: PP woven bags are recyclable, aligning with the increasing focus on sustainable packaging solutions.
Feature | Description |
---|---|
Durability | High tensile strength for heavy materials |
Customizable | Multiple color printing, logos, designs |
Lightweight | Easy to carry and transport |
Reusable | Can be used multiple times |
Eco-friendly | Made from recyclable materials |
Common Quality Issues in Woven Bags
Like all manufactured products, woven bags can experience quality issues that impact their performance and lifespan. Identifying and addressing these issues through comprehensive testing is crucial to ensure the bags meet industry standards and customer expectations.
1. Thickness Variations
A key issue in woven bags is inconsistent thickness. If the bag’s thickness varies too much, it may result in weak spots that compromise its overall strength. This is particularly important in heavy-duty applications where the bag is required to hold bulk materials like sand or grain. Manufacturers must ensure that the bag’s thickness stays within the specified tolerances to avoid problems like tearing or bursting.
2. Edge Fraying
Woven bags are cut to size during the manufacturing process, and poorly cut edges can lead to fraying. Frayed edges not only affect the bag’s appearance but can also cause functional problems, such as weakening the overall structure of the bag. Ensuring clean, precise cuts without jagged edges is vital for maintaining the integrity of the bag.
3. Color Discrepancy
Printed woven bags are often customized with logos and product information in multiple colors. Color discrepancy is a significant issue, especially for companies that rely on consistent branding. Variations in color can arise due to differences in the quality of inks or the printing process itself. This can lead to a product that does not meet visual quality standards.
4. Weight Deviation
The weight of woven bags is another critical factor. Deviations in weight may indicate problems with the production process or inconsistent material use. Since weight impacts transportation costs and usability, manufacturers need to ensure that each bag meets the specified weight range.
5. Tensile Strength and Elongation Failure
Tensile strength refers to the maximum stress that the bag can withstand before breaking. Inconsistent tensile strength and elongation rates (the ability of the material to stretch before breaking) can lead to premature failure of the bag under load. This issue is particularly relevant for bags designed to carry heavy products like cement or chemicals.
6. Impact Resistance
Woven bags must be able to withstand physical impact during transportation and storage. If a bag has low impact resistance, it could puncture or tear when dropped or subjected to pressure. Ensuring that the bags are impact-resistant is crucial for maintaining product integrity and safety.
7. UV Resistance
For bags exposed to sunlight, such as in outdoor storage conditions, resistance to ultraviolet (UV) rays is critical. Without UV stabilization, woven bags can degrade quickly, leading to brittleness and loss of strength. This is especially important for bags used in agriculture and construction industries, where products may be stored outdoors.
8. Environmental Impact
As the world moves toward more sustainable practices, the environmental performance of woven bags is becoming increasingly important. Ensuring that the materials used are recyclable, and that production processes are environmentally friendly, is crucial for minimizing waste and reducing the ecological footprint.
Comprehensive Testing Procedures
To address these common quality issues, our company implements a range of thorough testing procedures. These tests help ensure that every printed woven bag meets the required standards in terms of strength, durability, appearance, and environmental impact.
1. Thickness Tolerance Testing
We measure the thickness of each bag to ensure it stays within the allowable tolerance range. This ensures that the bag has a uniform structure and is free of weak spots.
2. Edge Cut Quality Testing
Cutting quality is evaluated to ensure that edges are smooth and free from fraying. This test ensures that the woven structure remains intact and that the bag’s overall strength is not compromised.
3. Color Matching Testing
For printed woven bags, we use advanced color-matching technologies to ensure that the printed colors are consistent with the customer’s specifications. This ensures that all custom logos and designs are printed accurately, enhancing the overall visual appeal.
4. Weight Testing
Every batch of woven bags is weighed to confirm that the bags meet the specified weight. This helps maintain consistency across all products and ensures that customers receive bags that are fit for their intended purpose.
5. Tensile Strength and Elongation Testing
We use tensile testing machines to measure both the tensile strength and elongation of the raw materials and finished bags. This ensures that the bags can withstand the stress of their intended use without tearing or breaking.
6. Impact Resistance Testing
Our impact resistance testing involves dropping the bags from different heights or applying sudden forces to simulate real-world conditions. This helps ensure that the bags can withstand the rough handling they may encounter during transportation.
7. UV Resistance Testing
To ensure the bags can withstand prolonged exposure to sunlight, we subject them to UV testing under controlled conditions. This test measures how well the bags resist degradation caused by ultraviolet rays.
8. Environmental and Sustainability Testing
We use eco-friendly materials and processes in our production lines and conduct environmental impact assessments to ensure that the bags can be recycled and reused, minimizing their environmental footprint.
Testing Procedure | Quality Issue Addressed |
---|---|
Thickness Tolerance Testing | Inconsistent thickness, weak spots |
Edge Cut Quality Testing | Frayed edges, compromised structure |
Color Matching Testing | Color discrepancies, poor print quality |
Weight Testing | Deviations in weight |
Tensile Strength & Elongation Testing | Weak tensile strength, poor elongation |
Impact Resistance Testing | Low impact resistance, puncture risks |
UV Resistance Testing | Degradation due to sunlight exposure |
Environmental Testing | Eco-friendliness, recyclability |
Customization Options for Printed Woven Bags
Printed woven bags are highly customizable, and this flexibility extends beyond just printed logos or designs. Various elements of the bag, such as size, material, weight, and color, can be tailored to meet specific customer needs. Below are some common customization options:
- Multiple Color Printing: Custom woven bags can be printed in various colors using techniques like flexographic or rotogravure printing. This allows for sharp, vibrant logos and designs, enhancing the visual appeal of the product.
- Custom Sizes and Dimensions: Bags can be tailored to the exact size and dimensions required by the customer. Whether it’s for bulk packaging or smaller retail use, our bags can be adapted to fit any requirement.
- Material Customization: Depending on the application, the material of the woven bags can be customized for additional strength or environmental performance. For example, adding UV-resistant additives or using eco-friendly, biodegradable materials.
- Gusset and Handle Options: Woven bags can be further customized with gussets (for greater storage volume) or handles (for ease of carrying). These features enhance both the functionality and usability of the bag.
Conclusion
Printed woven bags are an essential component in various industries due to their versatility, durability, and the ability to display custom logos and designs. However, like any product, they face certain quality issues during production, such as thickness variations, edge fraying, color discrepancies, and tensile strength problems. By employing comprehensive testing procedures, including thickness tolerance, tensile strength, and UV resistance testing, our company ensures that every printed woven bag meets the highest standards of quality and performance.
Through constant quality control, innovation, and customization, printed woven bags remain a reliable and sustainable packaging solution for industries worldwide. Whether you need printed woven sacks for agricultural products, chemicals, or food items, our rigorous quality assurance and testing processes ensure that you receive high-quality, durable, and eco-friendly packaging every time.
By understanding these common issues and the importance of comprehensive testing, businesses can make informed decisions when choosing the right printed woven bags for their specific needs.