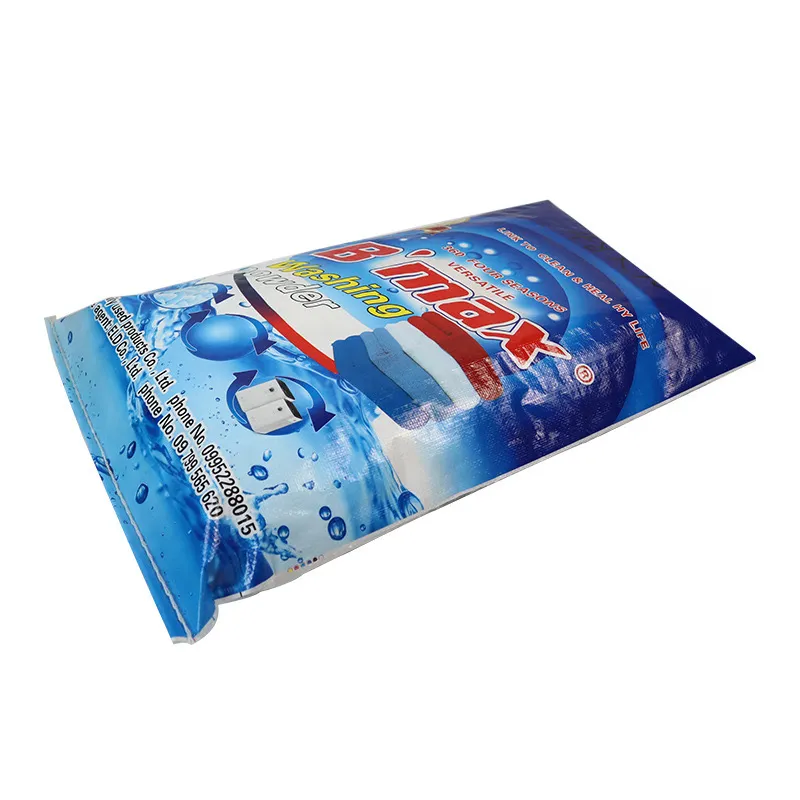
In the ever-evolving world of packaging, Printed BOPP Woven Bags stand out for their durability, versatility, and aesthetic appeal. They are commonly utilized across various industries, ranging from agriculture to construction, owing to their high strength and ability to showcase vibrant designs. However, the quality of these bags is paramount to ensure they meet industry standards and customer expectations. This blog post delves into the intricate process of quality control at VidePak, particularly focusing on the procurement and warehousing of raw materials used to manufacture Printed BOPP Woven Sacks.
Understanding BOPP Woven Bags
BOPP (Biaxially Oriented Polypropylene) Woven Bags are made from polypropylene yarn, which is woven together to form a robust and flexible material. These bags are printed using advanced techniques, allowing for high-quality graphics that enhance branding and product visibility. The production of Printed Woven Bags involves several critical stages, where quality control is integrated into every aspect to guarantee the final product’s performance.
Raw Material Procurement
Quality control begins with the procurement of raw materials. At VidePak, we prioritize the sourcing of new polyethylene (PE) and polypropylene (PP) plastic granules. These materials are essential for ensuring that the end products maintain their structural integrity and visual appeal.
Criteria for Raw Material Selection
The selection of raw materials involves meticulous criteria to ensure only the best materials are used. Here are some key factors:
- Purity and Quality: We procure virgin PE and PP granules, ensuring they are free from contaminants that could compromise the bag’s strength and appearance.
- Supplier Evaluation: Our suppliers undergo a rigorous evaluation process, ensuring they meet our quality standards and can consistently deliver high-quality materials.
- Batch Testing: Each batch of raw materials is subjected to quality tests before acceptance, including assessments of mechanical properties such as tensile strength, elongation, and melt flow rate.
Quality Control During Procurement
Quality control measures during the procurement phase are designed to minimize risks associated with raw material defects.
Parameter | Description | Testing Method |
---|---|---|
Tensile Strength | Measure of the maximum stress a material can withstand while being stretched or pulled | Universal Testing Machine |
Elongation | The degree to which a material can be stretched before breaking | Tensile Testing |
Melt Flow Rate | Indicates the flow characteristics of the resin during processing | Melt Flow Index Tester |
Each batch is tested for these parameters, ensuring that they meet our specifications before being transferred to the warehouse.
Warehouse Management
Once the raw materials have passed quality checks, they are stored in our state-of-the-art warehouse. Proper warehousing practices are critical in maintaining the integrity of the materials until they are ready for production.
Environmental Control
The warehouse environment is controlled to prevent degradation of raw materials. Key practices include:
- Temperature Control: The warehouse is kept at optimal temperatures to avoid any material warping or melting.
- Humidity Control: Maintaining low humidity levels prevents moisture absorption, which can weaken the polypropylene material.
- Regular Inspections: Our team conducts routine inspections to ensure that storage conditions remain optimal and materials are not exposed to adverse effects.
Quality Control During Storage
To ensure that the materials maintain their quality while in storage, we implement several quality control measures:
- Visual Inspections: Regular visual checks are performed to identify any signs of contamination or degradation.
- Inventory Tracking: Each batch of raw materials is tracked through our inventory management system, ensuring that older materials are used first to minimize the chance of degradation.
- Sample Testing: Periodic sampling of stored materials is conducted to ensure they continue to meet the necessary quality standards.
Production of Printed BOPP Woven Bags
With high-quality raw materials and robust warehousing practices in place, we move on to the production phase. Here, quality control is equally paramount, involving stringent monitoring at every step.
Printing Process
The printing process for Printed BOPP Woven Bags is conducted using advanced technologies that allow for precise and vibrant designs. This phase includes:
- Ink Quality: We use high-quality, UV-resistant inks to ensure longevity and vibrancy in printed designs.
- Printing Technology: Our state-of-the-art printing machines are calibrated regularly to maintain consistency and quality in prints.
Quality Control in Production
Quality checks are performed throughout the production phase, ensuring that every bag meets our specifications. Some key checks include:
Parameter | Description | Testing Method |
---|---|---|
Print Adhesion | Tests the strength of the ink bond to the surface of the bag | Tape Test |
Bag Strength | Measures the load-bearing capacity of the finished bag | Load Testing |
Appearance | Visual inspection for defects in print quality and bag finish | Manual Inspection |
Final Inspection
Before the Printed Woven Bags are shipped to customers, a final inspection is conducted to ensure compliance with customer specifications. This inspection includes a thorough examination of print quality, strength, and overall appearance.
Conclusion
In the production of Printed BOPP Woven Bags, maintaining high standards of raw material quality control, effective warehousing practices, and meticulous production checks are essential. At VidePak, we are committed to providing our customers with the highest quality products through comprehensive quality management systems, ensuring that every Printed BOPP Woven Sack not only meets but exceeds industry standards.
For more insights into our quality control processes, visit Printed BOPP Woven Bags.