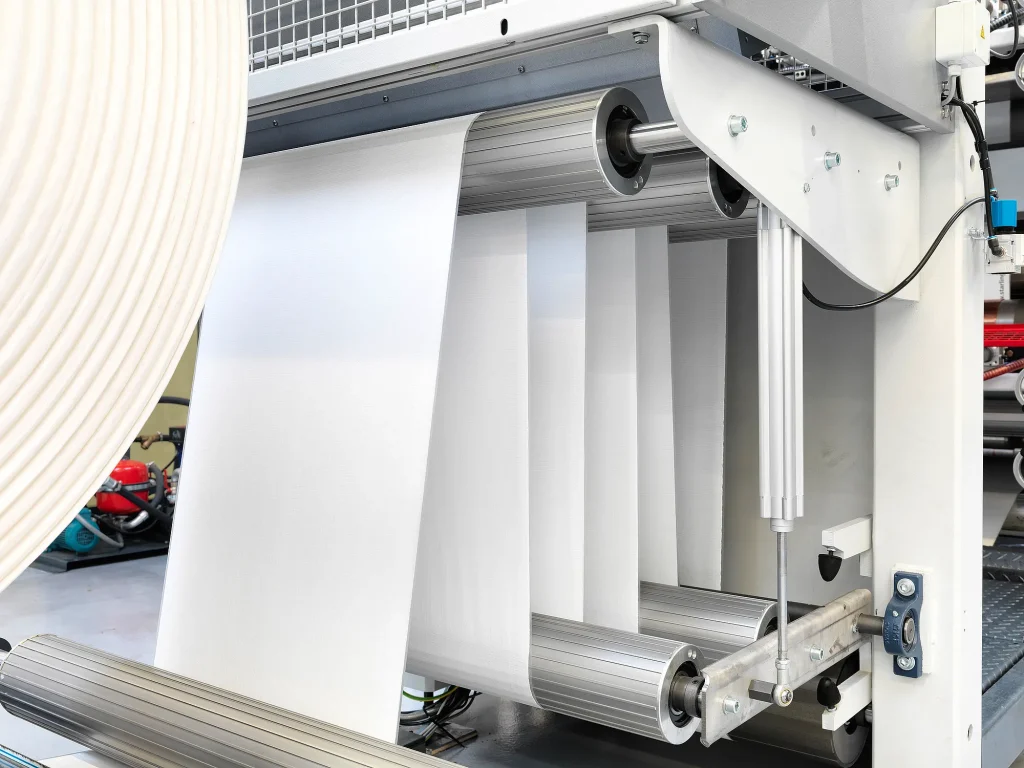
The primary answer this article provides is: Recyclable polypropylene (PP) woven bags reduce supply chain carbon footprints by 40–60% compared to single-use plastics, while specialized designs—ventilated (air permeability >500 L/m²/h), gas-blocking (<0.5% O₂ transmission), anti-static (surface resistivity <10^6 Ω), and antimicrobial (99.9% bacterial reduction)—address industry-specific challenges. VidePak’s ISO-certified production lines deliver 100% recyclable PP bags with 8–12 reuse cycles, trusted by global leaders in agriculture, chemicals, and pharmaceuticals.
Introduction
As global logistics emissions approach 8.1 gigatons CO₂ annually, industries face mounting pressure to adopt sustainable packaging without compromising functionality. Recyclable PP woven bags are emerging as a dual-purpose solution: reducing plastic waste through closed-loop recycling while incorporating advanced engineering for sector-specific performance. Whether transporting hygroscopic grains, volatile chemicals, or sterile medical supplies, modern PP bags balance ecological responsibility with technical precision—a duality perfected over VidePak’s 30+ years of R&D.
Founded in 2008, VidePak operates 100+ Starlinger circular looms and 30 lamination machines to produce 200 million PP bags annually. Our patented technologies, including nano-coated anti-static weaves and microperforated ventilation systems, serve Unilever, Bayer, and Cargill across 50+ countries, driving a $80 million annual revenue anchored in sustainability.
Sector-Specific Engineering: Beyond Basic Recycling
1. Ventilated Designs for Agricultural Logistics
- Microperforation Tech: Laser-drilled 0.5–1.0 mm pores enable airflow of 500–800 L/m²/h, reducing grain moisture by 15% during tropical transit.
- Case Study: A Vietnamese rice exporter cut spoilage rates from 8% to 1.2% using VidePak’s 140 g/m² ventilated bags with HDPE liners.
2. Gas & Moisture Barrier Systems
- Multi-Layer Lamination: BOPP/EVOH/Aluminum composites achieve:
- Oxygen Transmission Rate (OTR): <0.5 cm³/m²/day (vs. 1,200 for standard PP).
- Water Vapor Transmission Rate (WVTR): <0.1 g/m²/day.
- Application: Nitrogen-flushed coffee beans retain freshness for 18+ months.
3. Anti-Static Solutions for Hazardous Environments
- Carbon Fiber Weaves: Surface resistivity reduced to 10^5–10^6 Ω (vs. 10^12 Ω for standard PP), meeting IEC 61340-4-4 standards.
- Conductive Coatings: Graphite-doped PE layers dissipate charges in <2 seconds.
4. Antimicrobial Protection
- Silver Ion Integration: AgNPs (50–100 ppm) inhibit E. coli and S. aureus by 99.9% (ISO 22196).
- FDA-Compliant Coatings: Triclosan-free formulations for food/pharma use.
Technical Specifications by Application
Application | Design | Key Parameters | Certifications |
---|---|---|---|
Grains | Ventilated | 140 g/m², 600 L/m²/h airflow | FDA 21 CFR 177.1520 |
Chemicals | Anti-Static | 180 g/m², 10^6 Ω resistivity | IEC 61340-4-4, UN Certified |
Pharmaceuticals | Antimicrobial | 120 g/m², AgNP 75 ppm | ISO 13485, USP Class VI |
Electronics | Moisture-Blocking | 0.08 mm AlOx coating, WVTR <0.05 g/m²/day | JEDEC MSL 1 |
Recyclability & Lifecycle Analysis
- Closed-Loop Recycling: VidePak’s PP bags achieve 95% material recovery via Starlinger RECO granulators.
- Carbon Savings: Each reused bag reduces emissions by 1.2 kg CO₂ vs. virgin plastic.
- Case Data: A German automaker saved €480,000/year using VidePak’s 8-cycle PP totes for parts transport.
FAQs: Addressing Sustainable Procurement
Q1: How many reuse cycles do PP bags withstand?
VidePak’s 180 g/m² bags endure 12+ cycles (ISO 22442), with <5% tensile strength loss per cycle.
Q2: Are antimicrobial additives food-safe?
Yes. Our silver-ion coatings comply with EU 10/2011 and FDA CFR 175.300 for direct food contact.
Q3: Can ventilated bags withstand -20°C storage?
PP remains flexible at -30°C, but microperforations may ice over. Use <500 L/m²/h airflow for sub-zero environments.
Q4: What certifications validate recyclability?
UL ECOLOGO, EU REACH SVHC <0.1%, and APR Design® for Plastics Recyclability.
VidePak’s Manufacturing Excellence
- Starlinger Technology: 16 extruders produce 2.4-meter-wide PP fabric with ±0.05 mm thickness tolerance.
- Circular Economy: 30% post-industrial recycled content, UL-certified.
- Custom Printing: 10-color HD flexo with Pantone ±0.5 ∆E accuracy.
References
- VidePak Corporate Profile: https://www.pp-wovenbags.com/
- Industry Standards: ISO 22442, IEC 61340-4-4, FDA 21 CFR 175.300.
- Research: PP Recycling in Closed-Loop Systems (Plastics Europe, 2024).
For inquiries, contact info@pp-wovenbags.com.
External Resources:
- Explore anti-static packaging innovations: Anti-Static FIBC Bags: Health and Safety Performance Evaluation.
- Learn about advanced recycling systems: Sustainable FIBC Bulk Bags: Compliance and Ethical Practices.
Authored by VidePak’s Sustainability Engineering Team | Updated: March 2025