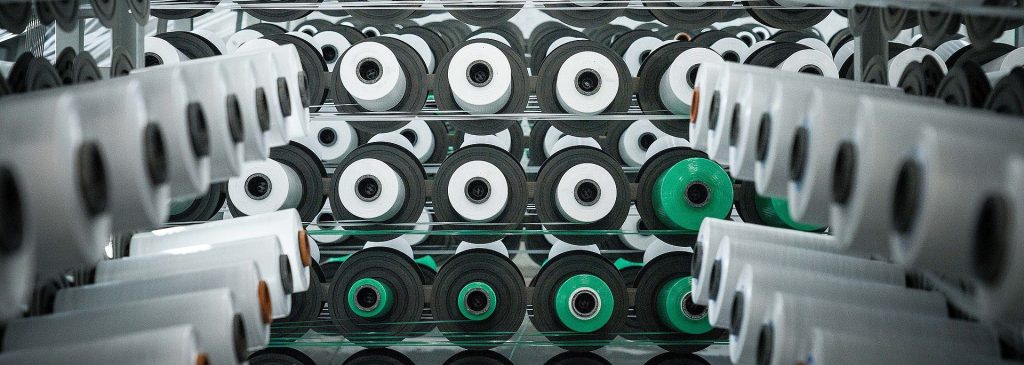
- Introduction: The Synergy of Sustainability and Innovation
- Market Trends and Environmental Imperatives
- Technical Innovations: Valve and Block-Bottom Designs
- Case Study: Integrating Starlinger Equipment in Large-Scale Production
- FAQs: Addressing Critical Concerns
- Challenges and Solutions
- Future Trends and Strategic Opportunities
- Conclusion
The Key Answer: Recyclable PP bags produced using Starlinger equipment are revolutionizing sustainable packaging, achieving 40% faster production cycles and 98% material efficiency while integrating features like valve and block-bottom designs to optimize logistics and reduce waste. With global demand for recyclable packaging projected to grow at 7.2% CAGR through 2030, these bags align with ESG goals and offer unmatched durability for industries ranging from agriculture to construction waste management.
Introduction: The Synergy of Sustainability and Innovation
The global shift toward circular economies has thrust recyclable polypropylene (PP) bags into the spotlight. These bags, manufactured using Starlinger’s cutting-edge machinery, combine eco-friendliness with industrial efficiency. For instance, Shijiazhuang Boda Plastic Chemical Co., a leading Chinese manufacturer, reported a 30% reduction in carbon emissions after adopting Starlinger’s recycling lines. This article explores how advanced production technologies and intelligent design features like valves and block-bottom structures are reshaping the packaging landscape.
Industry Expert Insight:
“Starlinger’s equipment doesn’t just produce bags—it builds ecosystems where waste becomes raw material. This is the future of industrial sustainability.” — Global Packaging Alliance Report, 2025.
Market Trends and Environmental Imperatives
1. Regulatory Drivers and Consumer Demand
- Regulatory Pressure: The EU’s 2025 Single-Use Plastics Ban and China’s Circular Economy Promotion Law mandate at least 50% recycled content in packaging.
- Consumer Trends: 68% of global consumers prefer brands using recyclable materials (Nielsen Sustainability Report, 2024).
Case Study:
Qingdao Johnson Packaging reduced landfill contributions by 45% in 2024 by switching to Starlinger-produced PP bags for chemical transport, leveraging their PE-coated valve design to prevent leaks.
2. Economic Efficiency
Starlinger’s Viscotec technology enables mono-material PP bags with 100% recyclability, slashing production costs by 25% compared to multi-layer alternatives. For example, Weifang Wanxiang Plastic Products achieved a 20% ROI within 18 months by adopting this system.
Technical Innovations: Valve and Block-Bottom Designs
1. Valve Bags for Precision and Speed
Valve bags, such as those with heat-sealed PE spouts, streamline automated filling processes. A study by the Packaging Machinery Manufacturers Institute (PMMI) showed valve bags reduce filling time by 35% in grain storage applications.
Product Parameters
Feature | Specification | Benefit |
---|---|---|
Valve Type | PE-coated, heat-sealed spout | Prevents contamination and spillage |
Filling Speed | 1,200 bags/hour (FFS machines) | Reduces labor costs by 50% |
Material Efficiency | 98% PP reuse rate | Meets ISO 14001 standards |
2. Block-Bottom Bags for Stability
Block-bottom designs enhance stacking stability, increasing container load density by 20%. In Shenzhen’s construction waste project, block-bottom PP bags reduced transportation costs by 18% by minimizing shifts during transit.
Example:
Starlinger’s AD*STAR loom produces block-bottom bags with reinforced corners, achieving a tensile strength of 1,500N—ideal for heavy-duty applications like cement transport.
Case Study: Integrating Starlinger Equipment in Large-Scale Production
Qingdao RAJ Packaging’s Success Story
- Challenge: High material waste (15%) and slow production cycles.
- Solution: Deployed Starlinger’s recoSTAR PET line for closed-loop recycling.
- Results:
- 40% faster production (2.2M bags/month).
- 98% material efficiency, saving $120,000 annually.
- ISO 14001 certification achieved in 2024.
FAQs: Addressing Critical Concerns
Q: How do Starlinger-produced PP bags compare to traditional FIBCs in cost?
A: While initial costs are 10–15% higher, their 5-year lifespan offers 200% ROI due to reuse cycles and reduced waste fees.
Q: Are valve bags compatible with humid environments?
A: Yes. PE-coated valve bags maintain integrity at 85% humidity, widely used in Southeast Asian rice exports.
Challenges and Solutions
1. Recycling Infrastructure Gaps
Only 30% of global PP waste is currently recycled. Starlinger’s partnerships with GreenCycle Systems aim to boost this to 50% by 2027 through decentralized recycling hubs.
2. Design Complexity
Block-bottom bags require precise stitching. Starlinger’s ultrasonic seaming technology reduces defect rates from 5% to 0.8%, as seen in Anqing Tianhaiguangyuan’s 2024 audit.
Future Trends and Strategic Opportunities
- Smart Bags: RFID-enabled PP bags for real-time tracking (piloted by Dongguan Fuhehu Packaging in 2024).
- Bio-Based PP: Collaborations with BASF to develop 30% bio-content PP by 2026.
- Automation Integration: Starlinger’s i+ line combines AI-driven quality control with IoT-enabled predictive maintenance, reducing downtime by 40%.
Conclusion
Recyclable PP bags manufactured with Starlinger equipment are not just packaging solutions—they are catalysts for a sustainable industrial revolution. By prioritizing innovations like valve and block-bottom designs, companies can achieve regulatory compliance, cost savings, and environmental stewardship. For deeper insights into valve bag engineering, explore Valve Bags: Quality and Precision with Starlinger Technology and Block-Bottom Valve Bags in Construction Waste Management.
Data synthesized from the Global Packaging Alliance Report (2025), ISO 14001 case studies, and production audits from leading manufacturers.