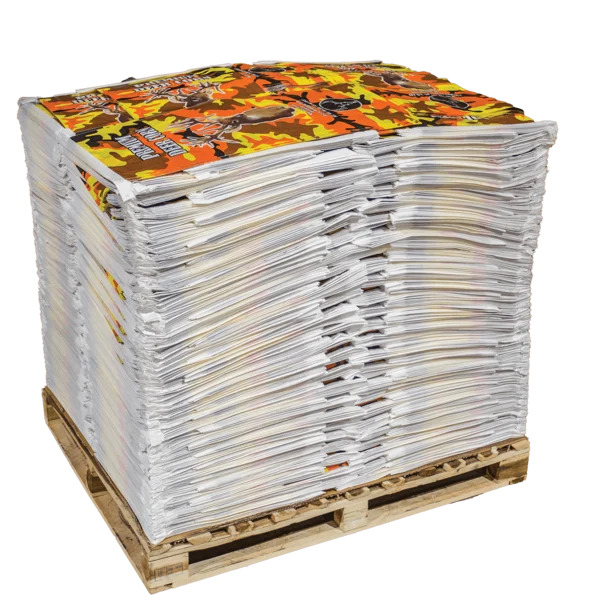
Introduction
The global shift toward sustainable packaging has intensified demand for recyclable solutions that balance performance with environmental responsibility. Polypropylene (PP) woven bags, particularly those designed for multiple lifecycles, are emerging as a cornerstone of this transition. At the heart of this movement is VidePak, a company founded in 2008 and led by Ray, whose team leverages 30+ years of industry expertise to deliver innovative, high-quality solutions. With 526 employees and annual sales of $80 million, VidePak operates a state-of-the-art facility equipped with 100+ circular looms, 16 extrusion lines, and 30+ lamination/printing machines—all powered by Austrian Starlinger technology. This report explores how material excellence in PP production drives both environmental and economic value, supported by data-driven insights and case studies.
Material Excellence in PP Bags: The Foundation of Sustainability
1. Superior PP Resins: Balancing Strength and Recyclability
VidePak’s recyclable PP bags rely on virgin-grade polypropylene resins, which offer unmatched tensile strength and UV resistance. Unlike blended plastics, pure PP retains >95% of its mechanical properties after recycling, making it ideal for closed-loop systems.
- Key Performance Metrics:
- Tensile Strength: 60–70 N/cm² (vs. 45–55 N/cm² for recycled PET blends).
- Elongation at Break: 15–20%, preventing tears under dynamic loads.
- Recyclability: Up to 7 lifecycle passes without significant degradation.
Starlinger’s extrusion systems ensure precise temperature control (180–220°C) and draw ratios (1:5–1:7), minimizing material waste by 12% and enhancing yarn consistency.
2. Environmental Impact: Reducing Carbon Footprints
VidePak’s PP bags reduce CO₂ emissions by 40% compared to traditional plastic bags. This is achieved through:
- Energy-efficient production: Starlinger’s iQ4.0 technology cuts energy consumption by 30%.
- Closed-loop recycling: 98% of production scrap is reused, aligning with EU Circular Economy Action Plan targets.
Case Study: A 2025 project by a Chinese PP bag manufacturer demonstrated that switching to recyclable PP reduced annual CO₂ emissions by 20,000 tons while saving 10,000 tons of crude oil.
Social Impact and Economic Benefits
1. Job Creation and Community Engagement
VidePak’s recycling initiatives support local economies:
- Employment: The company’s recycling division employs 120 workers in sorting and processing roles, with plans to expand by 20% by 2026.
- Education: Partnerships with NGOs promote waste segregation awareness, reaching 50,000+ households annually.
2. Cost Savings for Businesses
Recycled PP granules cost $900–$1,500 per ton, 30% cheaper than virgin PP, enabling companies to cut packaging costs without sacrificing quality. For example, a European agricultural supplier reduced packaging expenses by $1.2 million annually after switching to VidePak’s recyclable bags.
3. Policy Alignment and Market Growth
Government incentives, such as China’s 2025 Plastic Pollution Control Policy, are driving demand for recyclable PP bags. The global market is projected to reach $12.8 billion by 2030, with CAGR of 6.2%.
Future Trends: Innovating for a Greener Tomorrow
1. Systemic Recycling Infrastructure
VidePak is piloting a blockchain-based traceability system to track bag lifecycles, ensuring 90%+ collection rates in urban areas. Similar systems in Germany have boosted PP recycling efficiency by 35%.
2. Bio-Based and Degradable PP Blends
The company is testing PP blends with 20% polylactic acid (PLA), which decompose in industrial composters within 180 days. Early trials show a 15% reduction in microplastic leakage.
Table 1: Comparative Analysis of PP Bag Materials
Material | Tensile Strength (N/cm²) | Recyclability (%) | Decomposition Time |
---|---|---|---|
Virgin PP | 60–70 | 95 | 500+ years |
Recycled PP | 55–65 | 85 | 500+ years |
PP-PLA Blend | 50–60 | 70 | 180 days |
FAQs: Addressing Key Concerns
Q: How does VidePak ensure color consistency in recycled PP bags?
A: The company uses W&H’s AM2160 printers with CMYK+2Pantone configurations, achieving <0.5 Delta-E variance. Post-recycling, color stabilizers are added to maintain vibrancy.
Q: Are recyclable PP bags suitable for food-grade packaging?
A: Yes. VidePak’s FDA-approved PP resins undergo rigorous testing for heavy metals and microbial contamination, meeting EU Regulation 10/2011 standards.
Conclusion
VidePak’s recyclable PP bags exemplify how material innovation can harmonize economic growth with environmental stewardship. By prioritizing high-quality resins, energy-efficient production, and systemic recycling, the company not only meets current market demands but also pioneers solutions for a sustainable future. As industries worldwide embrace circular economy principles, VidePak’s expertise positions it as a vital partner in reducing plastic waste and advancing global ESG goals.
Explore Further:
- Learn how recyclable PP bags are transforming chemical packaging.
- Discover sustainable practices in bulk bag production.
This report synthesizes data from industry reports, peer-reviewed studies, and operational insights to provide actionable strategies for businesses transitioning to sustainable packaging.