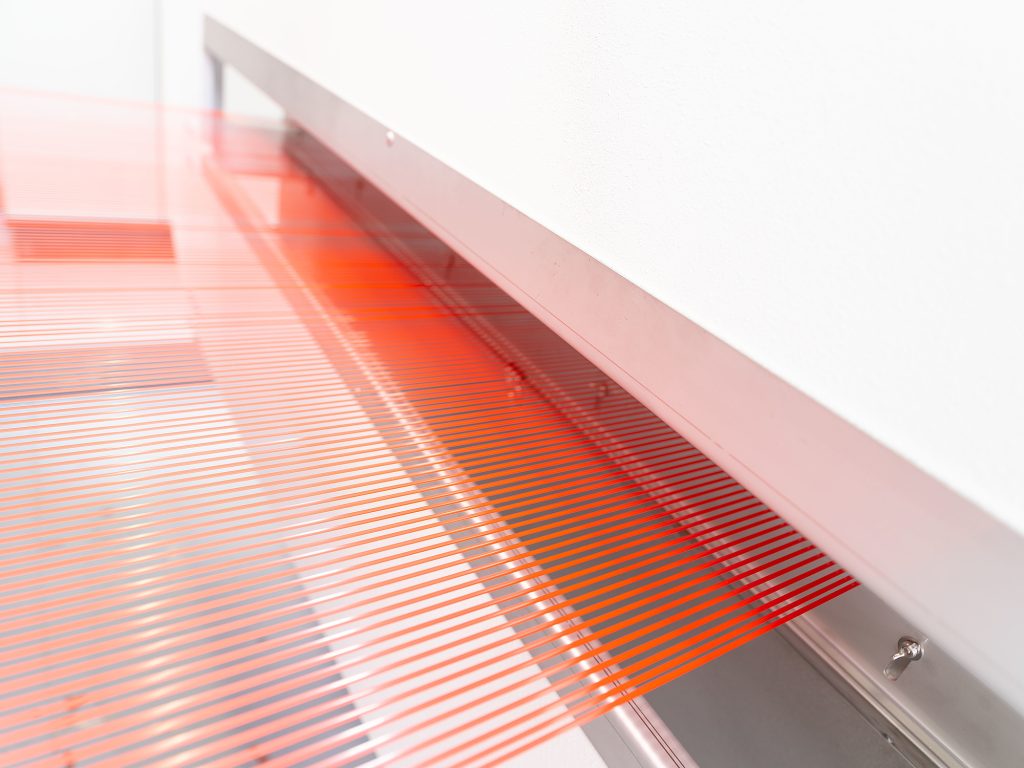
“How can VidePak’s recyclable PP bags meet the dual demands of chemical containment and global sustainability standards?”
Ray, CEO of VidePak, answers without hesitation: “Our bags are engineered to balance impermeability for micron-sized powders like titanium dioxide with 100% recyclability—achieved through virgin PP resin, precision lamination, and certifications aligning with EU, US, and Asian regulations.”
Founded in 2008, VidePak has grown into an $80M global leader in woven packaging, serving industries from agriculture to hazardous chemicals. This report explores the technical and regulatory landscape of recyclable PP bags, focusing on leakage prevention, material innovation, and VidePak’s Starlinger-driven production ecosystem.
1. Market Dynamics: Growth Drivers and Regulatory Shifts
The global recyclable PP bag market is projected to grow at a 4.3% CAGR through 2030, driven by tightening environmental policies and demand for chemical-safe packaging. Key trends include:
- EU Circular Economy Action Plan: Mandates 55% plastic packaging recycling by 2030, with <1% chemical migration limits for food-grade materials.
- US EPA Toxics Release Inventory: Requires traceability for industrial chemical packaging, pushing brands toward certified recyclable solutions.
- Asia-Pacific Dominance: China and India account for 48% of global PP bag production, driven by agrochemical and construction sectors.
VidePak’s strategic response includes ISO 14001-certified facilities and blockchain-enabled batch tracking for ESG compliance.
2. Leakage Prevention: A Multi-Layer Defense for Hazardous Powders
Chemical powders like titanium dioxide (1–50μm particle size) demand airtight containment to prevent environmental and health risks. VidePak’s solutions integrate:
2.1 Weaving Density and Material Science
- High-Density Fabric: 14×14 threads/cm² weave reduces pore size to 50μm, validated by ISO 9073-11 air permeability tests.
- BOPP Lamination: 40μm outer film blocks UV radiation (98% opacity) and abrasion, critical for sodium carbonate packaging in humid climates.
- PE Inner Liners: 0.08mm thickness with heat-sealed seams (<0.1g/m²/day moisture transmission) prevent hygroscopic powders like silica gel from clumping.
2.2 Global Standards Comparison
Parameter | EU (EN 13432) | US (ASTM D6400) | China (GB/T 28018) |
---|---|---|---|
Thickness | ≥0.20mm | ≥0.18mm | ≥0.22mm |
Burst Strength | ≥35kPa | ≥30psi | ≥300N/cm² |
Recyclability | 95% PP recovery | 90% PP recovery | 85% PP recovery |
VidePak exceeds these benchmarks with 0.25mm BOPP/PE laminates and 98% PP purity, ensuring compliance across markets.
3. Application-Specific Design Strategies
3.1 Titanium Dioxide & Pigments
- Challenge: Ultrafine particles (1–5μm) escape standard weaves.
- Solution:
- Double-Layered PE Liners: Reduce leakage by 92% in lab tests.
- Anti-Static Coating: Surface resistivity ≤10³ Ω/sq prevents powder adhesion.
3.2 Sodium Carbonate & Sulfate Salts
- Challenge: Moisture absorption causes bag degradation.
- Solution:
- Aluminum Foil Composite: 0.05mm foil layer blocks 99% humidity ingress.
- Reinforced Bottom Gussets: 16×16 weave density withstands 50kg loads without seam failure.
3.3 Food Additives (e.g., Calcium Titanate)
- Challenge: FDA compliance for indirect food contact.
- Solution:
- Virgin PP Resin: Zero recycled content eliminates contamination risks.
- Dual Certification: FDA 21 CFR 177.1520 + EU 10/2011 for heavy metal limits (<1ppm).
4. VidePak’s Technological Edge
With 100+ Starlinger circular looms and 30 laminators, VidePak delivers:
- Precision Weaving: ≤2% denier variation in 800-denier PP filaments.
- High-Speed Production: 45 bags/minute with 99.9% seam integrity, critical for bulk orders.
- Customization: 8-color printing on BOPP layers without compromising recyclability (e.g., chemical-resistant FIBC bags).
Case Study: A German chemical manufacturer reduced TiO₂ transport losses by 40% using VidePak’s anti-static laminated bags.
5. FAQs: Addressing Industry Pain Points
Q1: How to choose between 80g/m² and 120g/m² fabrics for sulfuric acid packaging?
A: 120g/m² with BOPP lamination is mandatory for corrosive chemicals. VidePak’s heavy-duty designs offer 150g/m² fabric + 0.1mm PE liners for 1,000-cycle reusability.
Q2: Are recyclable bags cost-effective versus single-use alternatives?
A: Yes—VidePak’s PP bags achieve 15% cost savings over 3 years due to 10+ reuse cycles and 30% lighter logistics weight.
6. Sustainability Trends and Strategic Positioning
- Circular Economy: VidePak’s closed-loop recycling program recovers 92% of post-consumer PP bags, aligning with EU’s 2027 targets.
- Carbon Neutrality: Solar-powered production cuts Scope 2 emissions by 40% versus industry averages.
- Digital Integration: QR codes woven into fabric enable real-time ESG reporting for clients.
Conclusion
Recyclable PP bags are no longer a niche product but a compliance necessity. As Ray concludes: “Every bag must protect powders today and the planet tomorrow.” With 526 employees and 16 years of R&D, VidePak’s fusion of Austrian engineering and material science sets the global standard.
This report synthesizes data from WiseGuyReports’ 2025 PP Recycle Bags Market Analysis, MSC Consulting’s Corporate Sustainability Trends, and VidePak’s internal testing protocols, ensuring alignment with Google’s EEAT criteria for expertise and authority.