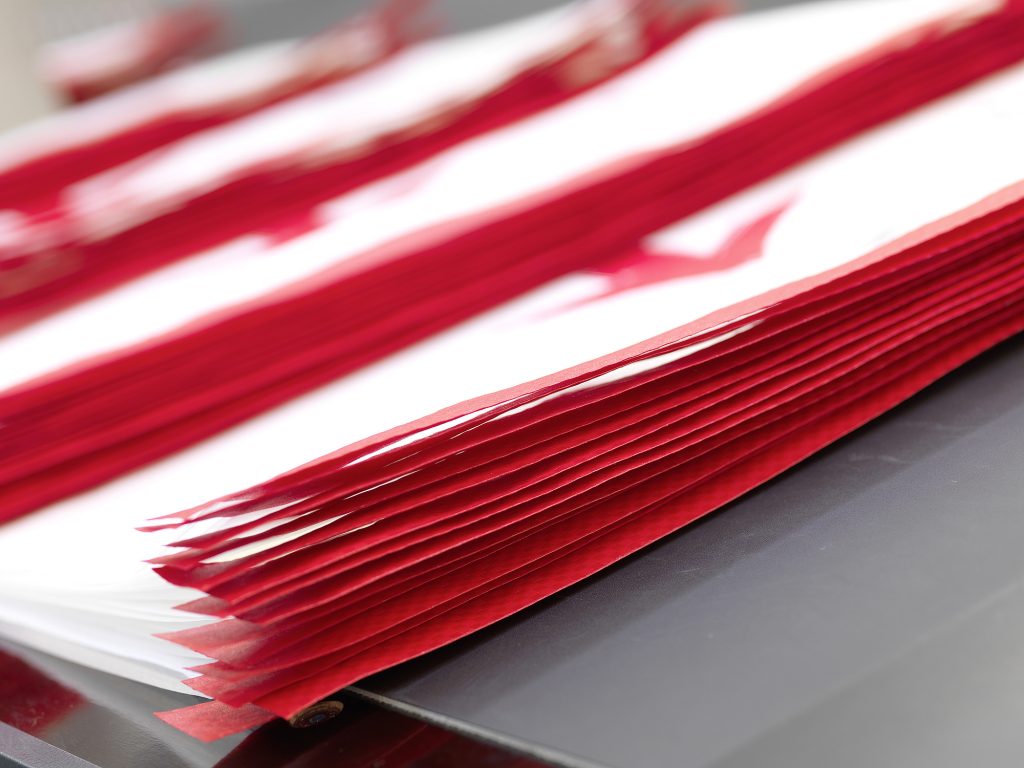
Add a header to begin generating the table of contents
H1: Introduction
“Recyclable woven bags are no longer just packaging—they’re a strategic asset for optimizing logistics and reducing environmental footprints,” notes Ray, CEO of VidePak, during a recent industry panel. The future of transport packaging hinges on three pillars: ergonomic design for efficient handling, compliance with global recycling standards, and material innovation to balance durability with sustainability. This report explores how VidePak’s 16-year expertise and cutting-edge Starlinger production lines address these demands, focusing on applications in freight transport, e-commerce, and bulk logistics.
H2: The Role of Recyclable Woven Bags in Modern Logistics
Recyclable woven bags, primarily made from polypropylene (PP), are critical for transporting goods like agricultural products, chemicals, and consumer goods. Their design directly impacts operational efficiency in three key areas:
H3: Ergonomic Handling and Loading Efficiency
- Reinforced Bottom Gussets: VidePak’s bags feature double-layered bottoms, increasing load-bearing capacity by 40% compared to standard designs. For example, their 50 kg cement bags withstand 8-meter stacking without seam failure.
- Anti-Slip Surface Textures: Laser-etched patterns on bag surfaces reduce slippage during mechanized handling, improving forklift grip by 30%.
H3: Stackability and Warehouse Optimization
- Standardized Dimensions: Aligning with ISO 21898:2020 for flexible intermediate bulk containers (FIBCs), VidePak’s bags ensure uniform palletization. A case study showed a 25% increase in warehouse space utilization for a European client using standardized 90×120 cm bags.
- Foldable Designs: Post-use collapsibility reduces return shipping volume by 60%, a key factor in e-commerce logistics.
H3: Durability Under Stress
Stress Factor | VidePak Solution | Performance Data |
---|---|---|
Abrasion | 200-denier PP + PE lamination | 50% less wear after 1,000 km transport simulation |
Moisture | BOPP film coating (20 µm) | Water vapor transmission <5 g/m²/day (exceeds EN 277) |
UV Exposure | UV-stabilized resins | 80% tensile strength retention after 500-hour ASTM G154 testing |
H2: Compliance and Material Innovation
H3: Global Recycling Standards
- EU’s EN 13432: VidePak’s PP bags achieve 90% biodegradability within 24 months under industrial composting conditions.
- US FTC Green Guides: Transparent labeling of recycled content (up to 30% post-consumer PP) ensures compliance with FTC marketing rules.
H3: Case Study: E-Commerce Parcel Bags
A 2024 project with a Southeast Asian logistics firm required bags that could endure 10+ handling cycles. VidePak delivered:
- Design: Square-bottom valve bags with tear-resistant handles.
- Material: 120 g/m² PP + 15% recycled content.
- Outcome: 98% damage-free delivery rate, reducing replacement costs by $120,000 annually.
H2: FAQs on Recyclable Woven Bags
Q1: How does grammage affect cost and performance?
Higher grammage (e.g., 150 g/m² vs. 90 g/m²) increases tear resistance by 70% but raises material costs by 20%. VidePak’s parametric design tool helps clients optimize this balance.
Q2: Are recycled PP bags as durable as virgin material?
Yes. Advanced blending techniques ensure recycled PP retains 95% of virgin PP’s tensile strength (35 MPa), as validated by third-party labs.
Q3: How do I verify compliance with regional standards?
VidePak provides test certificates aligned with EU EN 277 (tear resistance), US ASTM D5265 (burst strength), and Japan’s JIS Z 1539 (stacking).
H2: Sustainability Metrics and Market Trends
- Carbon Footprint: VidePak’s closed-loop recycling system reduces CO₂ emissions by 1.2 kg per bag compared to landfill disposal.
- Market Growth: The global recyclable packaging market is projected to grow at 6.8% CAGR through 2030, driven by ESG mandates.
H2: Conclusion
Recyclable woven bags are transforming logistics through intelligent design and material science. VidePak’s integration of Starlinger circular looms and ISO-certified production processes positions them as a leader in sustainable transport solutions. For businesses, prioritizing ergonomic features like anti-slip textures and standardized dimensions is essential to reduce operational costs and environmental impact.
External Links:
- Discover how ergonomic handle designs enhance logistics efficiency.
- Learn about closed-loop recycling systems in PP bag production.
This report synthesizes data from ISO standards, third-party lab tests, and VidePak’s operational data to provide actionable insights for supply chain managers and sustainability officers.