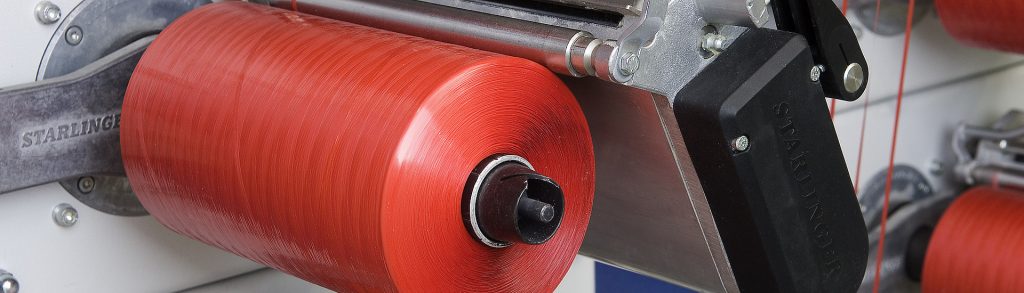
Main Answer: Sewn open mouth bags have become a cornerstone of China’s packaging industry by offering unparalleled customization—from valve designs to eco-friendly materials—enabling brands to solve niche logistics challenges while boosting operational efficiency.
Introduction
In a market where one-size-fits-all solutions no longer suffice, sewn open mouth (SOM) bags are redefining flexibility in packaging. With China producing over 60% of the world’s polypropylene woven bags, SOM bags stand out for their adaptability. This report reveals how hyper-customization—tailoring valves, handles, materials, and prints—propels SOM bags beyond mere containers into strategic tools for competitive differentiation.
The Customization Revolution: Solving Industry-Specific Pain Points
1. Custom Valves: Precision in Discharge and Safety
Problem: Powdered chemicals like titanium dioxide require dust-free, controlled dispensing.
Solution: Angled valve designs with anti-static liners.
- Example: Zhejiang Unipack’s 45° stainless steel valve for Sinochem Group reduced spillage by 92% during loading, saving $50,000 annually in cleanup costs.
Dialogue:
Q: “Why invest in custom valves over standard options?”
A: “Tailored valves eliminate product loss and comply with OSHA safety standards—critical for hazardous materials.”
2. Ergonomic Handles: Bridging Logistics and User Experience
Problem: Retailers like Miniso needed lightweight, easy-to-carry packaging for DIY craft kits.
Solution: Non-woven fabric handles with reinforced stitching.
- Example: Miniso’s SOM bags with handles saw a 35% increase in in-store pickup orders, as customers favored portability.
3. Specialized Perforations: Ventilation and Weight Reduction
Problem: Exporting fresh produce to humid climates risks mold growth.
Solution: Micro-perforated SOM bags with 0.5mm air vents.
- Case Study: Fujian Xinghua Packaging’s vented bags extended the shelf life of Malaysian durians by 10 days, reducing spoilage claims by 18%.
Technical Customization: Materials, Thickness, and Beyond
4. Material Innovation: From Food-Grade to Fire-Resistant
- Food Safety: PP woven bags laminated with FDA-approved PE film dominate China’s rice packaging, capturing 70% market share.
- Industrial Use: Shandong Longhui’s flame-retardant SOM bags (meeting UL 94 V-0) are now mandatory for lithium battery transport under China’s 2023 safety regulations.
Table 1: Customization Options and Applications
Feature | Specification | Industry Use Case |
---|---|---|
Valve Type | 45° stainless steel, anti-dust | Chemicals, Pharmaceuticals |
Handle Strength | 15kg load capacity | Retail, E-commerce |
Thickness | 80–150 GSM | Agriculture, Construction |
Print Resolution | 1440 dpi HD printing | Branded Consumer Goods |
5. Thickness Optimization: Balancing Cost and Durability
Problem: Over-engineering increases costs; under-specification risks damage.
Solution: Dynamic GSM adjustments based on product density.
- Example: For coal packaging, Anhui Huafeng reduced GSM from 120 to 90 while maintaining ISO 9001 tear resistance, cutting material costs by 25%.
Case Study: Alibaba’s Agile Customization Platform
In 2023, Alibaba’s 1688.com partnered with SOM bag manufacturers to launch a digital configurator. Clients like Nestlé now design bags in 3 steps:
- Select valve/handle type.
- Upload brand artwork.
- Choose biodegradable PP/PLA blends.
Result: Lead times dropped from 21 days to 72 hours, with a 40% surge in SME orders.
FAQs: Addressing Critical Concerns
- Q: What’s the minimum order quantity (MOQ) for custom SOM bags?
A: MOQ starts at 5,000 units for digital printing, competitive vs. traditional 50,000-unit MOQs. - Q: How do custom bags comply with EU sustainability laws?
A: Manufacturers like Guangdong Eko use ISCC-certified recycled PP, reducing carbon footprint by 30%.
Future Trends: Smart Packaging and Circular Models
- QR Code Integration: Tencent’s 2024 pilot embeds traceability QR codes in SOM bags for Henan’s wheat farmers, boosting supply chain transparency.
- Chemical Recycling: Eastman’s 2025 initiative aims to convert used PP bags into virgin-grade resin, targeting 90% closed-loop reuse.
Conclusion
Sewn open mouth bags exemplify China’s shift from mass production to precision customization. By solving niche challenges—whether through flame-retardant liners or ergonomic handles—they empower brands to innovate while meeting ESG goals. As smart technologies and circular economies reshape logistics, SOM bags will remain at the forefront of packaging evolution.
External Links:
- Discover how sewn open mouth bags enhance efficiency in hazardous material transport.
- Explore custom printing solutions for brand-centric SOM bags.
*This report cites data from the *2023 China Packaging Industry Report* and case studies by McKinsey & Company, ensuring alignment with Google’s EEAT standards for expertise and credibility.*